Runway overrun
Flair Airlines Ltd.
Boeing 737-800, C-FFLC
Kitchener/Waterloo Airport (CYKF), Ontario
The Transportation Safety Board of Canada (TSB) investigated this occurrence for the purpose of advancing transportation safety. It is not the function of the Board to assign fault or determine civil or criminal liability. This report is not created for use in the context of legal, disciplinary or other proceedings. See Ownership and use of content. Masculine pronouns and position titles may be used to signify all genders to comply with the Canadian Transportation Accident Investigation and Safety Board Act (S.C. 1989, c. 3).
Executive summary
On 24 November 2022 at 1850 Eastern Standard Time (EST), the flight crew of a Flair Airlines Ltd. Boeing 737-800 aircraft (registration C-FFLC, serial number 37758) began their duty period during which they would conduct 2 instrument flight rules flights: flight FLE500 from Kitchener/Waterloo Airport (CYKF), Ontario, to Vancouver International Airport (CYVR), British Columbia; and flight FLE501, a return flight to CYKF that would arrive the morning of 25 November.
The aircraft was dispatched with the No. 1 (left) thrust reverser inoperative, which was allowable per the minimum equipment list. To comply with the requirements of the minimum equipment list, the No. 1 reverse thrust lever was locked in the stowed position, and a placard was attached within view of the pilots. There had been a history of reported defects concerning the No. 1 thrust reverser on the occurrence aircraft dating back to May 2022. Although early troubleshooting efforts had identified a specific part that had to be replaced to rectify the situation, the replacement part was not procured until early November 2022 and had not been installed at the time of the occurrence. The investigation determined that Flair Airlines Ltd.’s maintenance, repair, and overhaul tracking system was capable of identifying recurring defects as defined by regulations, but its capabilities did not extend to identifying defects such as the left thrust reverser fault in this occurrence, which did not meet the definition of a recurring defect. The defect had been reported 23 times during the 6 months leading to the occurrence. If the underlying issue behind a persistent maintenance defect is not addressed in a timely manner, there is a risk that it may compound, resulting in a serious consequence.
The 1st flight was uneventful, departing CYKF at 2013 EST and arriving at CYVR at 0118 EST. The return flight departed at 0238 EST with 6 crew members and 134 passengers onboard. During the cruise portion of the flight, a passenger medical issue occupied the flight crew’s attention for a significant length of time, preventing them from having an opportunity to obtain controlled rest on the flight deck during the flight.
During the week leading up to the occurrence, the captain of the occurrence flight had conducted 2 other overnight flights. Although he had been scheduled appropriate time free from duty according to the regulations, and he had carried out a self-assessment and determined that he was fit for duty at the beginning of the scheduled flight on 24 November 2022, the captain had accrued a significant sleep debt in the week before the occurrence and was operating the aircraft after a nearly 18-hour wake period, at the end of a circadian low. As a result, at the time of the occurrence, the captain’s level of fatigue decreased his attention and vigilance and increased the likelihood of a slip. The investigation found that if pilots do not monitor their rest to assess if they have accrued a sleep debt, there is an increased risk of fatigue going undetected and unmitigated.
During the descent, the flight crew obtained the latest weather information from the automated weather observation system at CYKF, which reported ceilings of approximately 600 feet above ground level, light rain, and reduced visibility. The flight was cleared for an instrument landing system approach to Runway 26. During the approach, with the autopilot and autothrottle engaged and the captain as pilot flying, the aircraft descended through 600 feet above ground level but remained in cloud. As a result, the captain mentally rehearsed the actions that would be required for a go-around.
The aircraft broke out of the cloud shortly afterward, and the approach continued. At approximately 300 feet above ground level, the captain disconnected the autopilot. The captain, who was the pilot flying, left the autothrottle engaged after disengaging the autopilot as a result of a habit formed from past flying experience where the practice was permitted.
Shortly before landing, the captain intended to press the autothrottle disengage switch, but inadvertently pressed the takeoff/go-around switch. This slip likely occurred due in part to the captain’s level of fatigue, and because he was primed to press the takeoff/go-around switch, having mentally rehearsed a go-around earlier in the approach. In addition, the inadvertent takeoff/go-around selection at 70 feet above ground level occurred during a period on the approach when the flight crew’s primary focus was outside of the flight deck. Therefore, with the indications of the takeoff/go-around selection insufficiently salient to alert the crew, the flight mode annunciator and engine thrust display indications for mode change went unnoticed by the flight crew. Although the autothrottle commanded both thrust levers towards go-around thrust temporarily, the captain held both of them at or near the idle position during the flare and landing.
At 0624 EST, the aircraft touched down on Runway 26. The left reverse thrust lever had been locked in the stowed position per the minimum equipment list. When selecting the right reverse thrust lever following touchdown, the pilot removed his hand from the forward thrust levers, allowing the left one to advance, undetected, as commanded by the autothrottle. This had a number of consequences: the advancing thrust lever caused the speed brakes, which had briefly deployed, to retract and resulted in the deactivation of the auto-braking system, significantly reducing deceleration during the initial ground roll.
The captain immediately encountered difficulty with directional control of the aircraft and initiated manual braking. The captain stowed the No. 2 thrust reverser and was able to keep the aircraft on the runway surface while applying manual braking. When the captain applied maximum braking, there was 2500 feet of runway remaining, and the aircraft was travelling at a ground speed of 115 knots with no speed brakes, one engine at near maximum thrust, and the other nearing maximum reverse thrust. At this speed and in this configuration, there was insufficient runway remaining to stop the aircraft and it overran the end of the runway at 0625 EST. The aircraft overran the paved surface of Runway 26 at a ground speed of 45 knots, entered a soft, grassy area, and came to a stop approximately 300 feet from the pavement edge and 500 feet from the runway end.
There were no injuries and no apparent damage to the aircraft. After receiving information from responders on the ground regarding the condition of the aircraft, the flight crew elected to start the aircraft’s auxiliary power unit to keep the passengers comfortable on board until mobile airstairs and buses could be brought to the aircraft to facilitate the transfer of passengers to the terminal building.
1.0 Factual Information
1.1 History of the flight
At 1850All times are Eastern Standard Time (Coordinated Universal Time minus 5 hours). on 24 November 2022, the occurrence flight crew began their duty day at Kitchener/Waterloo Airport (CYKF), Ontario. The flight crew had been scheduled to conduct 2 instrument flight rules flights on the Flair Airlines Ltd. (Flair) Boeing 737-800 aircraft: flight FLE500 from CYKF to Vancouver International Airport (CYVR), British Columbia, followed by flight FLE501, the return flight to CYKF, which would depart and arrive the morning of 25 November.
The Boeing 737-800 had been dispatched with the No. 1 (left) thrust reverser inoperative, which was allowed under the airline’s approved minimum equipment list (MEL).The minimum equipment list (MEL) is “[a] list which provides for the operation of aircraft, subject to specified conditions, with particular equipment inoperative, prepared by an operator in conformity with, or more restrictive than, the MMEL [master minimum equipment list] established for the aircraft type” (Source: International Civil Aviation Organization [ICAO], Doc 9868, Procedures for Air Navigation Services—Training, Third edition [2020], part I: General Procedures, chapter 1: Definitions and acronyms, p. I-1-3). Per the MEL, the left reverse thrust lever was locked in the stowed position, preventing it from moving out of the forward thrust position (Figure 1), and a placard was affixed to it.
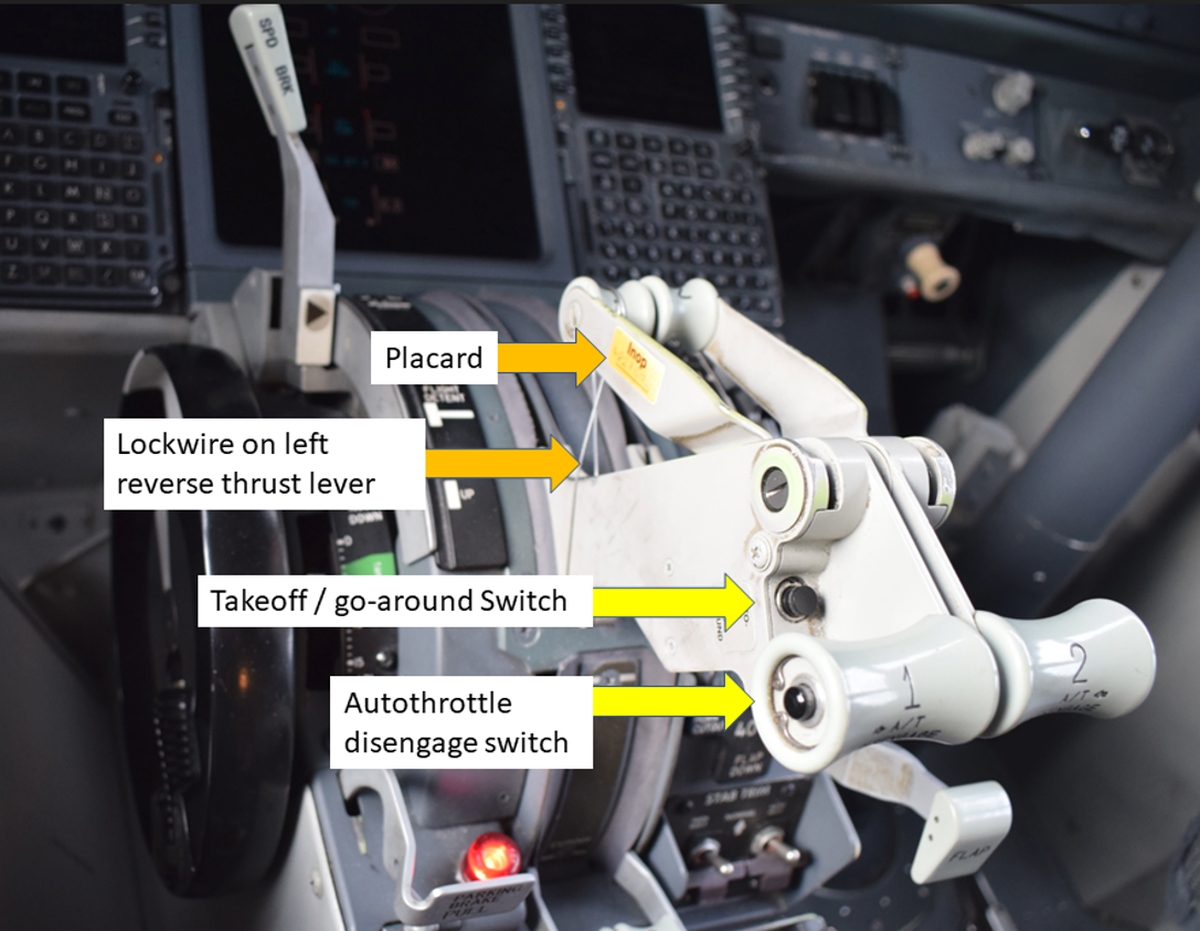
The 1st flight was uneventful; flight FLE500 departed CYKF at 2013 and arrived at CYVR at 0118 on 25 November.
At 0238, the return flight, flight FLE501, departed CYVR bound for CYKF with 2 flight crew members, 4 cabin crew members, and 134 passengers on board. The captain was seated in the left seat and was the pilot flying (PF), and the first officer, who was in the right seat, was the pilot monitoring (PM). The entire flight took place during the hours of darkness. During the cruise portion of the flight, the flight crew spent a significant amount of time responding to a passenger medical emergency that had arisen.
At 0603, during the descent, weather conditions were obtained from the CYKF automated weather observation system (AWOS) in preparation for the approach and landing. The reported weather indicated overcast ceilings at 600 feet above ground level (AGL) and visibility of 2 statute miles in light rain and mist, along with strong and gusty westerly winds. As a result, the flight crew determined that an instrument landing system (ILS) approach to Runway 26 would be most suitable. They received clearance for this approach from the Toronto Area Control Centre (ACC).
The CYKF control tower did not open until 0700, so the flight crew broadcasted their intentions on the CYKF mandatory frequency once they had been assigned to it by the arrival controller at the Toronto ACC.
As part of the descent checklist, the autobrake select switch was set to 3. During the landing checklist, the speed brake lever was placed in the ARMED position, arming the automatic speed brake system, which would move the speed brake lever to the UP position automatically upon touchdown.
After the aircraft flew past the final approach fix, the PF began looking out the window, expecting to make visual contact with the ground as the approach progressed. However, the cloud ceilings were lower than reported on the AWOS, and after the aircraft had descended through 600 feet AGL, the PF was still unable to obtain visual contact with the ground as he had expected, prompting him to mentally rehearse the steps required in case a go-around became necessary. Shortly afterward, he made visual contact with the ground, followed soon after by visual contact with the approach lighting for Runway 26.
At 0624:13, while the aircraft was at approximately 300 feet AGL, the PF disengaged the autopilot. He left the autothrottle engaged.
At 0624:29, as the aircraft descended through 70 feet AGL, the PF, intending to disengage the autothrottle, instead pressed the takeoff/go-around (TO/GA) switch (Figure 1).
The autothrottle, which was still engaged, was applying force to the forward thrust levers, driving them towards go-around thrust for 4 to 5 seconds before they were moved to the idle position by the PF, where he held them during the flare and landing; he did not detect the force that was being applied by the autothrottle.
At 0624:36, the aircraft touched down firmly approximately 1400 feet past the runway threshold at a ground speed of 142 knots. The speed brakes deployed, and the PM made a verbal callout stating that they had done so. The PF removed his hand from both forward thrust levers to grip the No. 2 (right) reverse thrust lever and actuate that thrust reverser.When a reverse thrust lever is used, a mechanical locking device prevents movement of the forward thrust lever on which the reverse thrust lever is mounted. Given that the PF was no longer holding the left forward thrust lever at idle, the autothrottle, which was still engaged, could now move it forward towards go-around thrust, causing the speed brakes to retract, and deactivating the auto-braking system. There was approximately 5600 feet of runway remaining at this time.
The PF did not realize that the left forward thrust lever was advancing, and he was having difficulty maintaining directional control of the aircraft because the left engine was advancing towards maximum forward thrust while the right thrust reverser was being deployed. The aircraft’s path began to deviate towards the right edge of the runway.
At 0624:41, 5 seconds after touchdown, the PF began to apply manual braking using the toe brakes on the rudder pedals while he continued to try to keep the aircraft on the runway laterally. The aircraft’s ground speed was approximately 132 knots, and there was approximately 4600 feet of runway remaining.
At 0624:44, the PF increased reverse thrust on the right side, while the autothrottle continued to advance the left forward thrust lever towards maximum thrust.
At 0624:48, having noted the unusual aircraft behaviour and lack of deceleration, the PM scanned the flight deck and noticed that the left forward thrust lever was not in idle as expected. He reached under the right hand of the PF and pulled the left forward thrust lever back to idle. When he released it, it began to move back towards maximum forward thrust; however, neither crew member noticed this because they were focused on the directional control of the aircraft.
At 0624:52, 16 seconds after touchdown, full brake pressure was applied. The aircraft’s ground speed was approximately 115 knots, and there was approximately 2500 feet of runway remaining.
At 0624:55, the PF stowed the right thrust reverser using the reverse thrust lever, and by 0624:57, both forward thrust levers were moved back towards idle by the PF; they remained at idle for the rest of the landing roll. This action coincided with the aircraft’s maximum lateral deviation from the centreline. The ground speed was approximately 100 knots, and there was approximately 1700 feet of runway remaining.
At 0625:05, the aircraft slowed below 80 knots and the autothrottle disengaged automatically. There was approximately 300 feet of runway remaining, plus approximately 200 feet of paved surface beyond the end of the runway. One second later, the PF deployed the right thrust reverser again.
At 0625:09, the aircraft overran the runway onto the paved surface beyond the runway end. Three seconds later, 36 seconds after the initial touchdown, the aircraft overran the paved surface at a ground speed of approximately 45 knots. It entered the soft, grassy area beyond the runway’s end before coming to a stop approximately 300 feet beyond the paved surface (approximately 500 feet beyond the end of Runway 26) (Figure 2).
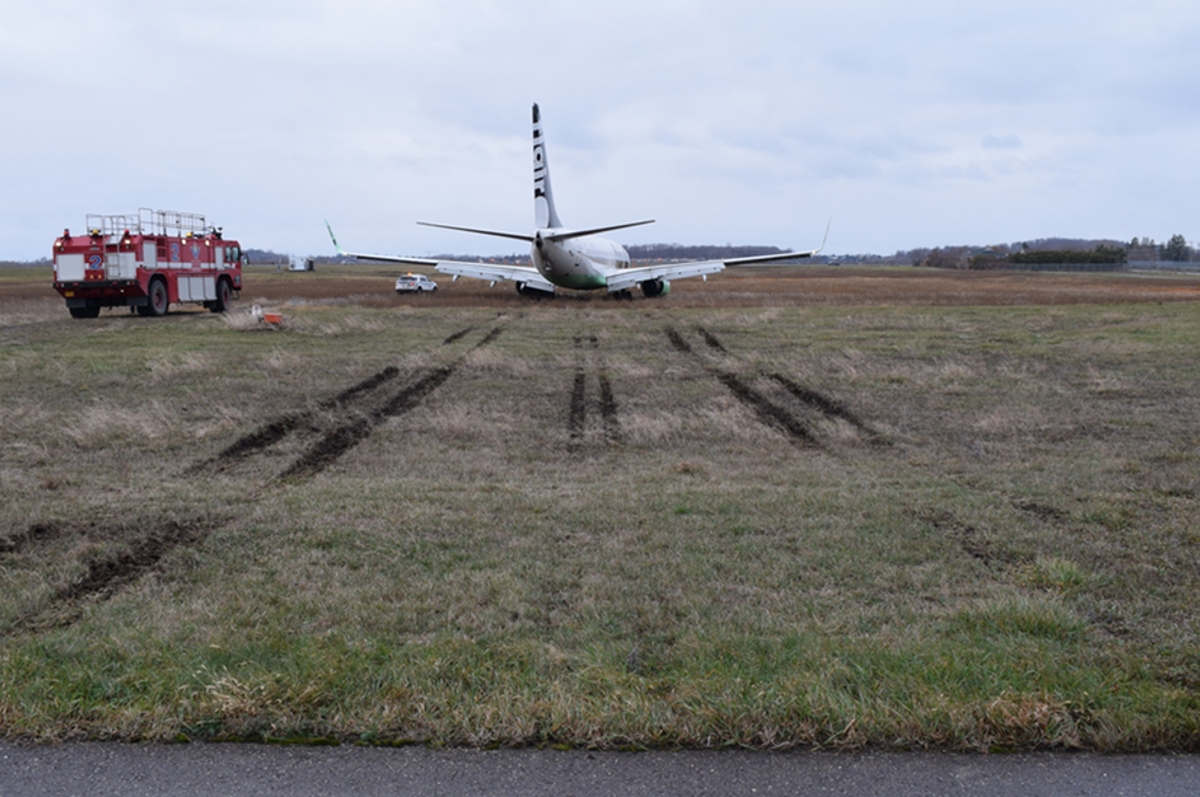
The PM contacted both CYKF aircraft rescue and fire fighting (ARFF) personnel and the Toronto ACC to inform them of the overrun. ARFF personnel had already noticed that the aircraft had overrun the runway, and they had initiated their response. Shortly after the aircraft came to a stop, the flight crew started the auxiliary power unit to supply power to the aircraft and allow the cabin to be kept warm for passenger comfort.
Within a few minutes, an aircraft maintenance engineer from Flair’s contracted approved maintenance organization (AMO) arrived at the aircraft after having witnessed the overrun. He was able to speak to the flight crew through the flight deck window, and after walking around the aircraft, he indicated that there did not appear to be any significant damage to the aircraft, or any fluid leaks. Moments later, the ARFF and other airport personnel arrived at the aircraft.
Due to the cold and rainy weather conditions, the flight crew elected to keep the passengers on board until airstairs could be transported to the aircraft, which enabled the passengers to disembark normally. They were transported to the terminal building by airport personnel.
1.2 Injuries to persons
There were no injuries among the 6 crew members and 134 passengers on board.
1.3 Damage to aircraft
The aircraft was inspected for a high drag/side load landing. The engines were inspected for foreign object debris both visually and internally with a borescope per the applicable procedures in the aircraft maintenance manual.
There was no damage to either engine. However, cleaning and lubrication procedures were completed on the engines, fuselage, and landing gear to remove foreign object debris contamination.
Displaced washers were found at the left main landing gear forward trunnion and fuselage attachment pin during an inspection, necessitating the replacement of the upper and lower pins.
1.4 Other damage
There was no other damage.
1.5 Personnel information
Captain | First officer | |
---|---|---|
Pilot licence | Airline Transport Pilot | Airline Transport Pilot |
Medical expiry date | 01 April 2023 | 01 May 2023 |
Total flying hours | 24 200 | 2762 |
Flight hours on type | 542.7 | 182.7 |
Flight hours in the 24 hours before the occurrence | 9.5 | 9.5 |
Flight hours in the 7 days before the occurrence | 22.4 | 19.1 |
Flight hours in the 90 days before the occurrence | 201 | 182.7 |
Flight hours on type in the 90 days before the occurrence | 201 | 182.7 |
Hours on duty before the occurrence | 11.7 | 11.7 |
Hours off duty before the work period | 18.5 | 132 |
The flight crew held the appropriate licences and ratings for the flight in accordance with existing regulations.
The captain joined Flair as a direct-entry captain in May 2022, and his Boeing 737 training began shortly afterward. Before joining Flair, he had accumulated more than 25 years of flight experience as an airline captain on several Boeing and Airbus aircraft types, although he did not have any Boeing 737 experience. He received his 737 type rating in April 2022. His 1st flight as a flight crew member on the 737 was on 24 May 2022, and his 1st flight as pilot-in-command on the 737 was on 31 July 2022.
The first officer joined the airline in August 2022 and received his 737 type rating in August 2022. His 1st flight as first officer on the 737 was on 15 September 2022, the date on which his line indoctrination began.
1.6 Aircraft information
1.6.1 General
Manufacturer | Boeing |
---|---|
Type, model, and registration | 737-86J, C-FFLC |
Year of manufacture | 2010 |
Serial number | 37758 |
Certificate of airworthiness issue date | 16 August 2019 |
Total airframe time | 25542.1 hours |
Engine type (number of engines) | CFM56-7B26/3 (2) |
Maximum allowable take-off weight | 174 200 lb (79 015.79 kg) |
Recommended fuel type(s) | Jet A, Jet A-1, Jet B |
Fuel type used | Jet A |
The aircraft’s weight and centre of gravity were within the prescribed limits.
1.6.2 Left thrust reverser deferred defect
The flight departed with a deferred defect related to the left thrust reverser. The MEL required the affected reverse thrust lever to be locked in the stowed position to prevent it from being actuated. The MEL also required a placard to be placed on the lever. The deferral and associated maintenance actions were recorded per the airline’s MEL and maintenance control manual requirements.
There had been 23 defects reported that were related to the left thrust reverser during the 6 months leading up to the occurrence. During that time the left thrust reverser defect had been deferred per the MEL on 6 occasions. Three of those deferrals were granted an extensionFlair Airlines Ltd., Maintenance Control Manual, Revision 39 (17 March 2022), 4.5.3 MEL Item(s) Repair Interval Extensions Procedure, p. 4-3., including the deferral in effect at the time of the occurrence, which was recorded on 10 November 2022. It was required per the MEL to be fixed within 10 days, but due to an issue with parts availability, an extension was granted for an additional 10 days on 20 November 2022.
The required replacement part was delivered on 18 November 2022, but because of a change in the aircraft schedule, the aircraft and the replacement part were not in the same location in time to make the repair before the occurrence flight.
1.6.3 Automatic flight system
The Boeing 737-800 automatic flight system consists of the autopilot flight director system (AFDS) and the autothrottle.
The AFDS is a dual system consisting of 2 individual flight control computers and a single mode control panel (MCP), which houses the mode selector switches used by pilots to select desired command modes for the AFDS and autothrottle. The AFDS system incorporates both the autopilot and the flight director.
The autopilot, when engaged, physically moves the pilot’s control wheels (see Figure 7 in Section 1.6.3.1 Autopilot) to the positions required to maintain the aircraft’s flight path based on the selected command modes. For redundancy, there are 2 identical autopilots, each with their own flight control computer. This is referred to as a dual-channel system. During the majority of flight operations, only a single channel of the autopilot is used.
The purpose of the flight director is to display command bars on each primary flight display if command pitch and roll modes are engaged. The flight director command bars are a visual cue for pilots, and they indicate whether any pitch or roll adjustments are necessary to maintain the aircraft’s position based on the selected command modes.
The autothrottle provides automatic thrust control for takeoff, climb, cruise, descent, approach, and go-around or landing. When engaged, the autothrottle physically moves the forward thrust levers using a separate servo motor on each thrust lever.
Most autopilot and autothrottle modes are selected by the pilots using the MCP located just below the glareshield (Figure 3).
The go-around mode can only be selected using one of the TO/GA switches located on the thrust levers (see Figure 1 in Section 1.1 History of the flight).
Pilots input the desired route of flight, altitudes, and speeds using the flight management computer (FMC), which continuously computes the pitch, roll, and airspeed inputs required to maintain that path.
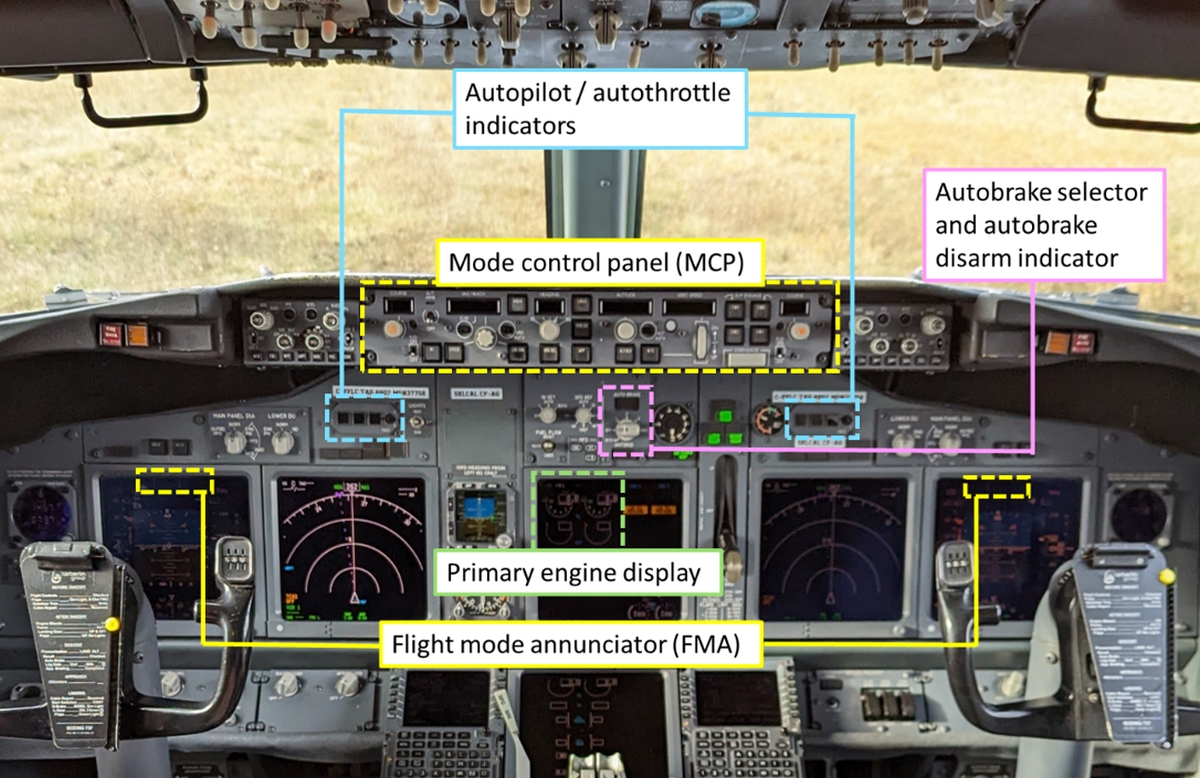
The armed or engaged status of the autothrottle and autopilot modes are displayed on the flight mode annunciator (FMA) on each pilot’s primary displayFlair Airlines Ltd., B737-800 Flight Crew Operating Manual, Volume 2, Revision 21 (02 August 2022), Autopilot Flight Director System (AFDS), p. 4-20-1. above the attitude indicator. The FMA, which is divided into 3 parts, indicates the engaged modes in green, and armed modes in white, for the autothrottle, roll, and pitch, from left to right respectively (Figure 4).
When a mode change occurs, the newly engaged mode is surrounded by a green box for 10 seconds after activation.
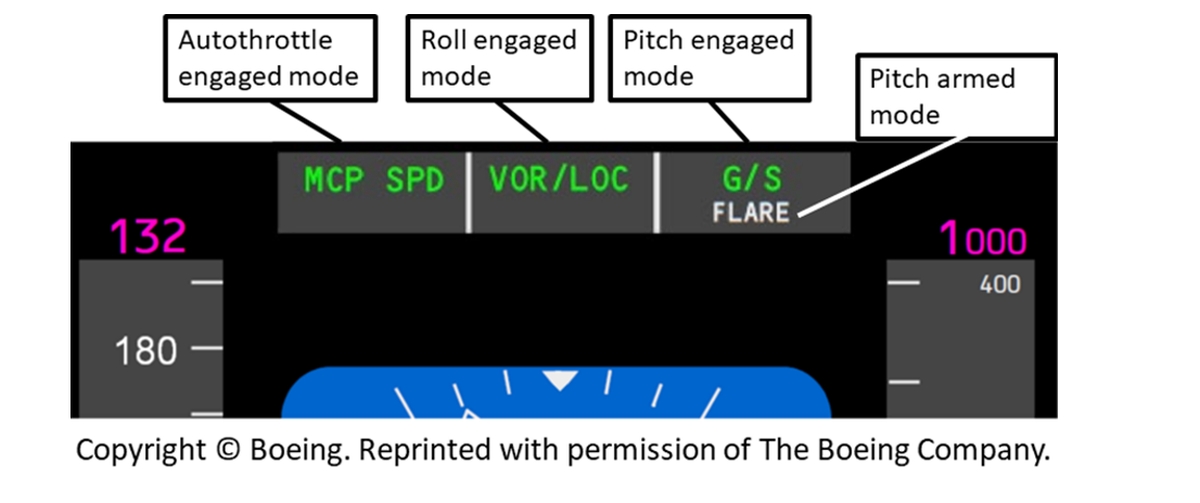
The autopilot and the autothrottle use servo motors to drive their respective controls to the positions required to achieve the flight path commanded by the FMC. The movements generated by the servo motors also drive the flight-deck controls to give feedback to the pilots.
1.6.3.1 Autopilot
The Boeing 737-800 autopilot can control the aircraft flight path in all phases of flight and is engaged using either or both of the 2 autopilot command (CMD) engage switches on the MCP, located on the glareshield. Controlling the various autopilot modes of operation is accomplished using a series of switches and selectors located on the MCP (Figure 5).
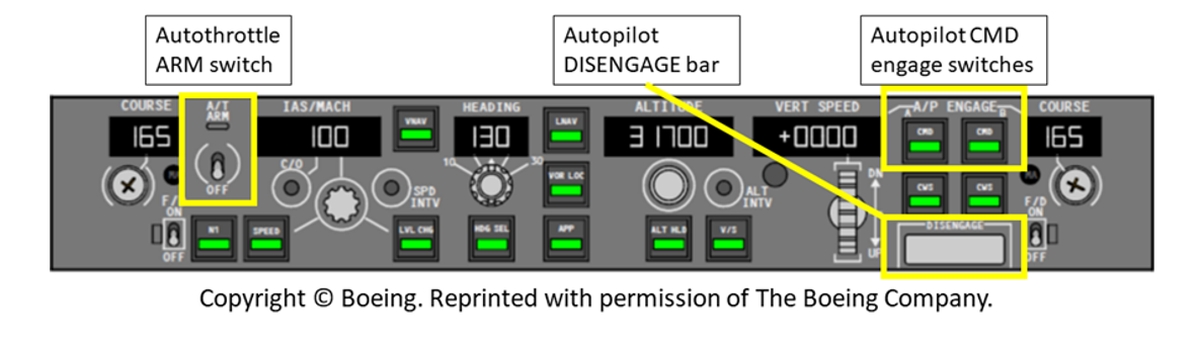
With single channel autopilot engaged, pilots can manually override the autopilot servo motors for the control column (pitch) inputs, which requires approximately 20 pounds of force, or for the control wheel (roll) inputs, which require approximately 10 pounds of force. In either case, manually overriding the autopilot will result in an autopilot disengagement, although this is not an approved method for disengaging the autopilot.
When the autopilot is disengaged by any means, a distinct aural warning tone will sound on the flight deck and the autopilot disengage light, located above each pilot’s inboard display, will flash (Figure 6).
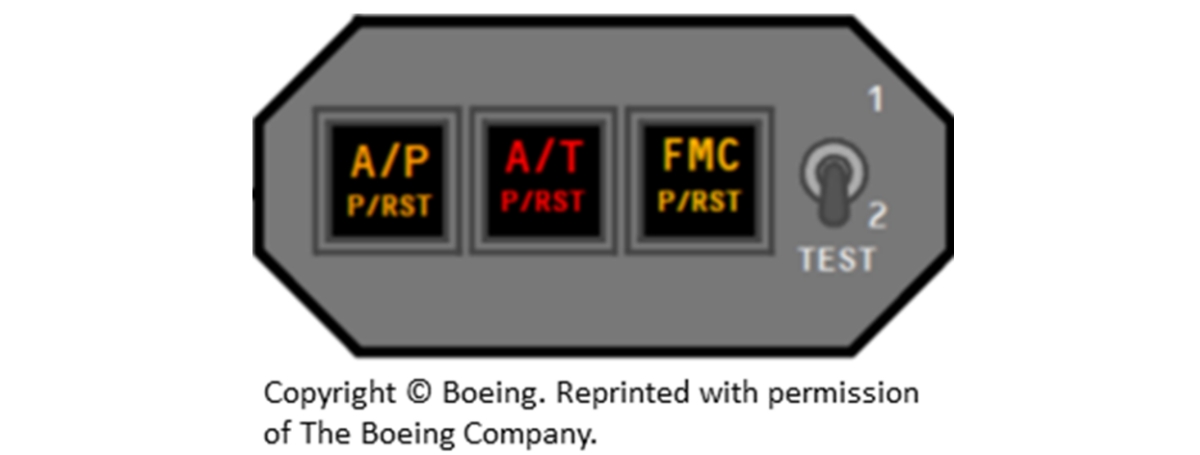
This indicator light can be extinguished by pressing the autopilot disengage switch on the pilot’s control wheel (Figure 7) or pressing the light itself.
The most common method for disengaging the autopilot is a double press of the autopilot disengage switch on the PF’s control wheel; the 1st press will disengage the autopilot, and the 2nd press will extinguish the autopilot disengage light and silence the aural warning.
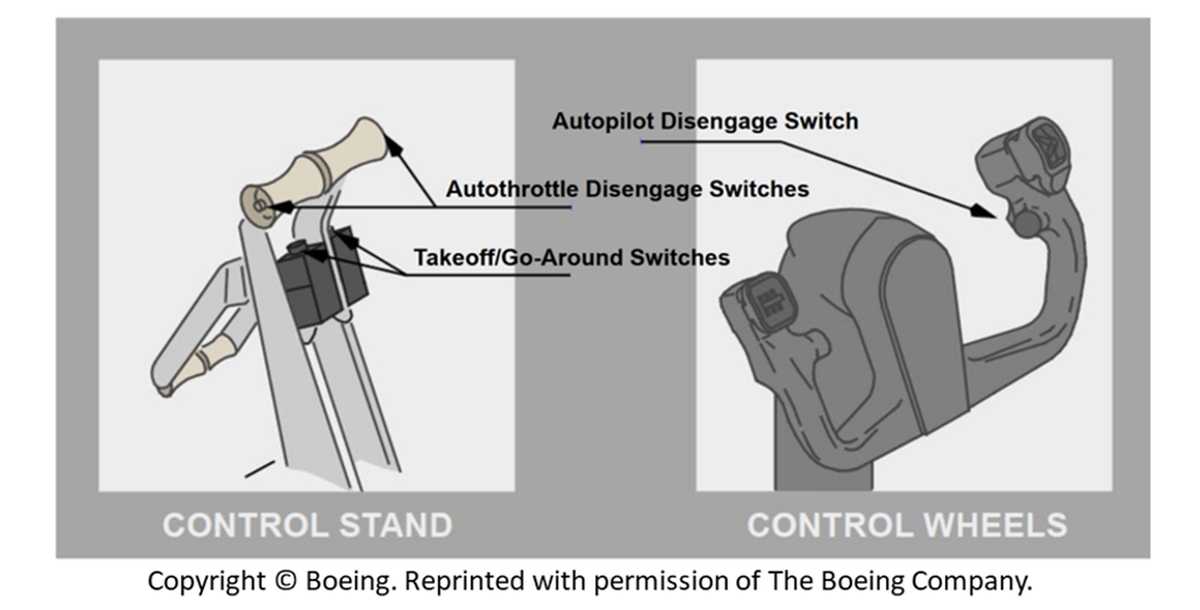
1.6.3.2 Autothrottle
The autothrottle is armed by positioning the autothrottle ARM switch on the MCP to the ARM position, where it is magnetically held until the autothrottle is disengaged (Figure 5). A green light illuminates above the ARM switch when it is moved to the ARM position. When the autothrottle is armed, it will engage automatically when an applicable mode becomes engaged.
Flight crews can override the thrust lever movement by manually positioning the levers, which requires approximately 3.5 pounds of force per thrust lever. Once the pilot releases the forward thrust levers, the autothrottle may automatically reposition the forward thrust levers to comply with computed thrust requirements.Ibid., Autothrottle System - Boeing, p. 4-20-21.
Unlike the autopilot, overriding the autothrottle servo motors does not result in disengagement of the autothrottle.
Also, unlike the autopilot, there is no aural warning when the autothrottle is disengaged. Instead, the autothrottle disengage lights will flash red. This lighted switch is located above each pilot’s inboard display (Figure 3), next to the autopilot disengage light (Figure 6).
The most common method for disengaging the autothrottle is a double press of the autothrottle disengage switch on the side of the thrust lever; the first press disengages the autothrottle, and the second press extinguishes the disengage light.
The flight crew can also disengage the system by moving the A/T ARM switch to OFF.
According to Flair’s Flight Crew Operating Manual (FCOM), any of the following conditions or actions will always result in a disengagement of the autothrottle:
- moving the A/T Arm switch to OFF;
- pressing either A/T Disengage switch;
- an A/T system fault is detected;Ibid., Automatic Flight – System Description, Autothrottle Disengagement, p. 4-20-9.
In addition, the FCOM states that the autothrottle will disengage automatically in the following conditions, in any mode other than go-around mode:
- two seconds have elapsed since landing touchdown. […]
- thrust levers become separated more than 10 degrees;
- significant thrust difference along with control wheel roll input of 10 degrees or more at any point throughout the entire flight envelope.Ibid., pp. 4-20-9 to 4-20-10.
When the autothrottle go-around mode is engaged, the autothrottle will only disengage automatically if a system fault is detected, or if the aircraft slows below 80 knots. Although the 80-knot disengagement is by design, this condition is not described in the manufacturer’s or operator’s manuals.
Autothrottle disengagement is followed by the A/T ARM switch releasing to OFF and the flashing red A/T Disengage lights. The A/T Disengage lights do not illuminate when the autothrottle automatically disengages after touchdown.Ibid., p. 4-20-10.
In the occurrence flight, the autothrottle disengaged when the indicated airspeed dropped below 80 knots during the landing roll.
1.6.3.2.1 Autothrottle switchpack
There are 2 autothrottle switchpacks located below the control stand, 1 for each thrust lever assembly. Each switchpack contains 9 switches, 3 of which are part of the thrust reverser system: an arming switch, a stowing switch, and a synchronous shaft-lock switch.
These switches sense the position of the reverse thrust lever and supply signals to other systems related to the operation of the associated thrust reverser.The Boeing Company, 737-600/700/800/900 Aircraft Maintenance Manual, Chapter 78: Engine Exhaust, Thrust Reverser Control System – Arm, Stow and Sync Lock Switches.
Servicing or replacing an autothrottle switchpack requires access to the underside of the control stand through the forward access door on the exterior of the aircraft, in front of the nose wheel well.
Repairing or replacing the switchpack can, therefore, be a time-consuming task, requiring work in a confined space. This part was replaced after the occurrence, and it was reported that the ongoing issues with the left reverse thrust system were resolved as a result.
1.6.3.3 Automatic flight system’s go-around mode
The go-around (GA) mode of the automatic flight system is engaged when either TO/GA switch is pressed (Figure 7), and it will be indicated on the FMA; the autothrottle engaged mode changes to GA provided that the autothrottle is armed, and the pitch engaged mode changes to TO/GA. These mode changes appear on the FMA on each pilot’s primary flight display, with green boxes appearing for the first 10 seconds around the changed modes (Figure 8).
In addition, the engagement of TO/GA will result in navigation cues displayed on the primary flight displays. The pitch cue will indicate the desired pitch attitude to be flown to maintain the programmed rate of climb, the roll cue will indicate the correct control inputs for the pilot to maintain the current ground track, and the command airspeed cursor will indicate a target airspeed for the existing aircraft configuration.Flair Airlines Ltd., B737-800 Flight Crew Operating Manual, Volume 2, Revision 21 (02 August 2022), Automatic Flight – System Description, Go-Around, p. 4-20-21.
On approach, with the autothrottle in the ARM position, the autothrottle GA mode is armed automatically when descending below 2000 feet radio altitudeRadionavigation equipment on board an aircraft makes use of the reflection of radio waves from the ground to determine the height of the aircraft above the surface of the earth (Source: Termium Plus)., with or without the autopilot engaged.
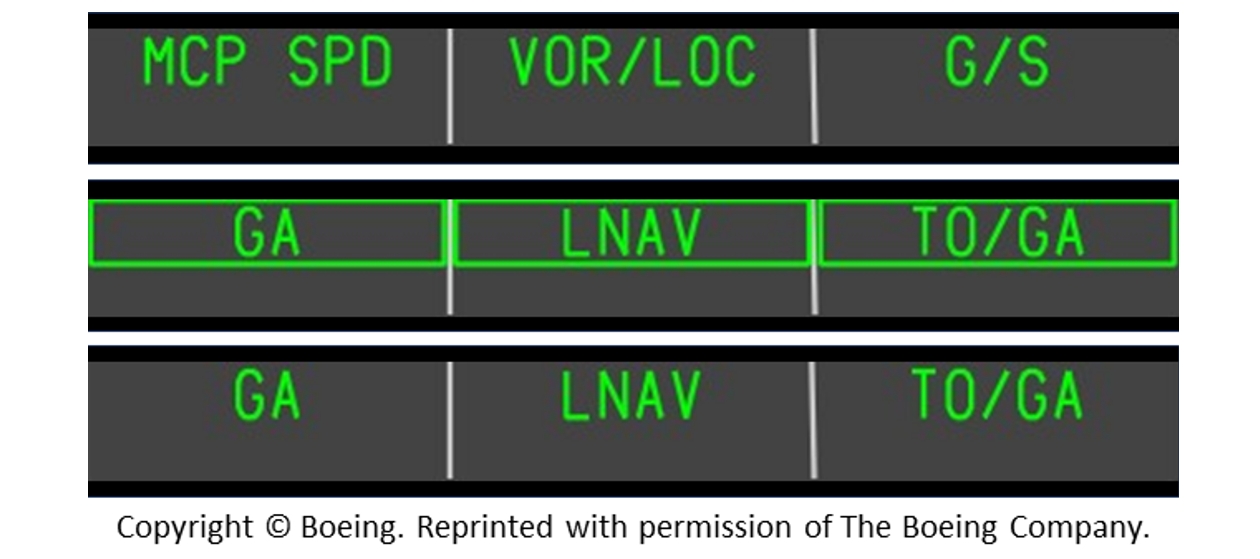
1.6.4 Autobrake system
The autobrake system supplies braking at a constant deceleration rate without manual input from the flight crew.
The autobrake control panel contains a rotary selector switch that can be set to RTO (rejected takeoff), OFF, 1, 2, 3, or MAX. The rate of deceleration depends on the switch position.
After landing, the selected autobrake application begins when both forward thrust levers are retarded to idle and the main wheels spin up.
After braking has started, any of the following pilot actions disarm the system immediately:
- moving the SPEED BRAKE lever to the down detent;
- advancing the forward thrust lever(s), except during the first 3 seconds after touchdown for landing;
- applying manual brakes.Flair Airlines Ltd., Flight Crew Operating Manual, Volume 2, Revision 21 (02 August 2022), Autobrake System, pp. 14-20-4 and 14-20-5.
The AUTO BRAKE DISARM light (Figure 10) indicates that the system has become disarmed. It is located above the autobrake selector, which is located on the centre instrument panel above the upper display unit where the primary engine information is displayed.
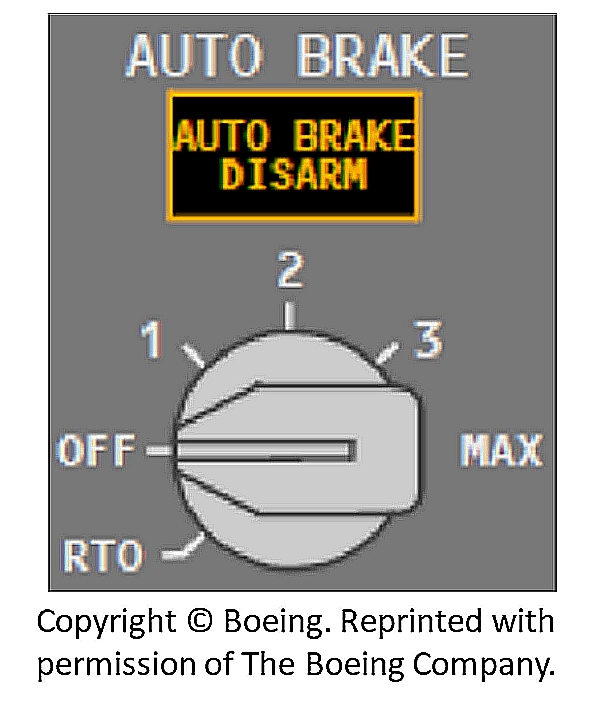
1.6.5 Automatic speed brake system
The Boeing 737-800 incorporates an automatic speed brake system that uses both flight spoilers and ground spoilers to aid in the deceleration of the aircraft after landing. The automatic speed brake operates when these conditions occur:
- SPEED BRAKE lever is in the ARMED position;
- SPEED BRAKE ARMED light is illuminated;
- radio altitude is less than 10 ft;
- landing gear strut compresses on touchdown; […]
- both thrust levers are retarded to IDLE;
- main landing gear wheels spin up (more than 60 kts).
The SPEED BRAKE lever automatically moves to the UP position and the spoilers deploy.
Note: Following an all flaps up (no flap) landing, the SPEED BRAKE lever will not move beyond the FLIGHT DETENT and the spoilers will not fully deploy. […]
After […] landing, if either thrust lever is advanced, the SPEED BRAKE lever automatically moves to the DOWN detent and all spoiler panels retract.Ibid., Speed Brakes, Ground Operation, pp. 9-20-14 and 9-20-15.
The speed brake handle is located to the left of the thrust levers. There are 3 indicator lights associated with the speed brake system. The SPEED BRAKE ARMED and SPEED BRAKE DO NOT ARM lights are located below the left autopilot/autothrottle indicators, and the SPEEDBRAKES EXTENDED light is located below the right autopilot/autothrottle indicators (Figure 11).
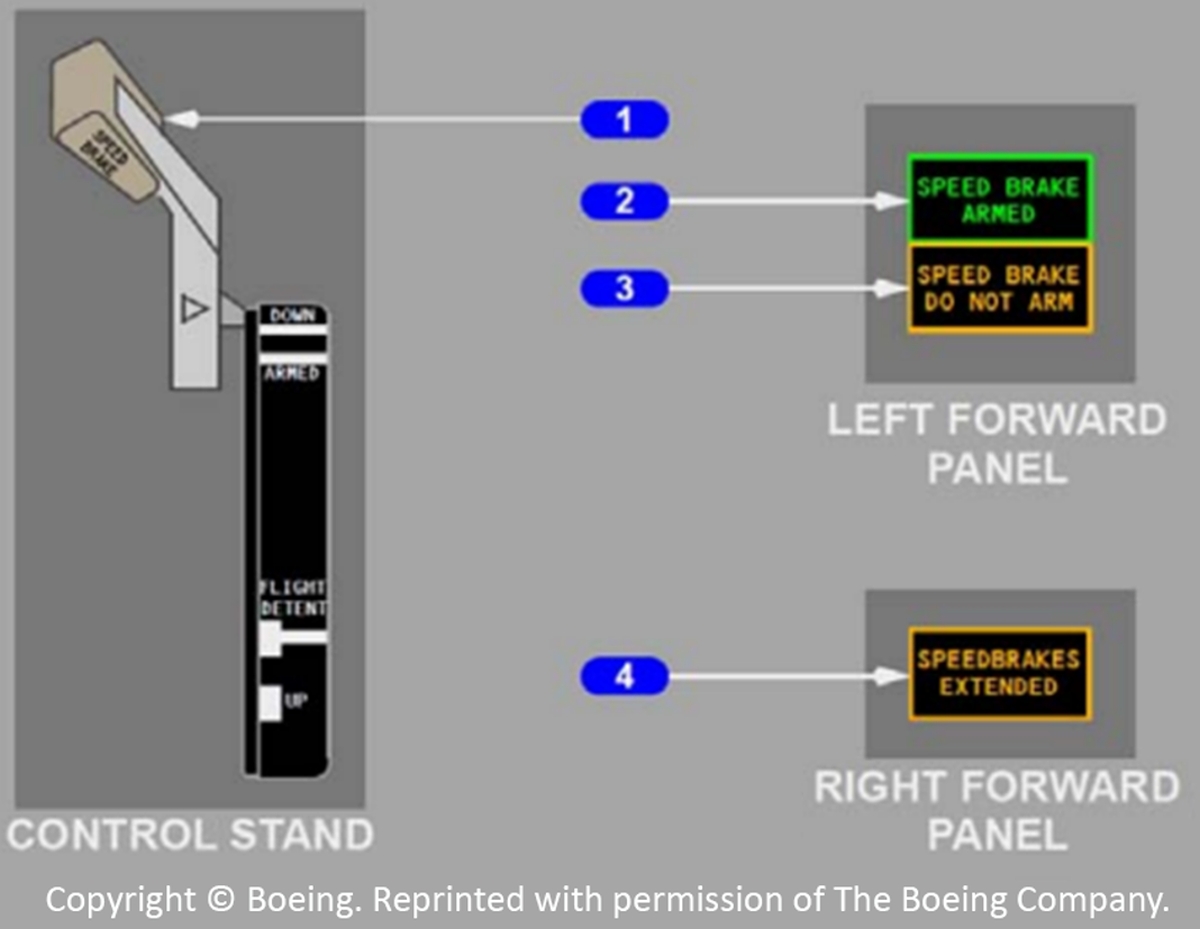
1.7 Meteorological information
During the hours that CYKF is uncontrolled, weather information is obtained via an AWOS, which provides limited information compared to an aerodrome routine meteorological report (METAR).
The AWOS sensors are not regularly monitored, so they can become contaminated and provide inaccurate weather information, especially when there is precipitation or other obscuring phenomena such as fog or mist in the area.
The AWOS at CYKF reported the following conditions at 0624:
- Winds from 300° true at 16 knots, gusting to 23 knots
- Visibility of 2½ statute miles in light rain and mist
- Overcast cloud ceiling at 600 feet AGL
- Temperature 5 °C, dew point 4 °C
- Altimeter setting 29.83 inches of mercury
The runway was wet at the time of the occurrence, although there was no reported standing water on the runway surface.
There was no current runway surface condition report available at the time of the occurrence.
1.8 Aids to navigation
Not applicable.
1.9 Communications
Not applicable.
1.10 Aerodrome information
CYKF is located in Breslau, Ontario, approximately 35 NM west-southwest of Toronto/Lester B. Pearson International Airport (CYYZ).
CYKF’s longest runway is Runway 08/26, which is 7003 feet long and 148 feet wide. Runway 26 is served by an ILS approach, while all runways at the airport have at least 1 area navigation (RNAV/GNSS) approach available.
Both ends of Runway 08/26 contain runway end safety areas (RESAs). According to the Canada Flight Supplement, the departure end of Runway 26, where the occurrence took place, has a RESA that is approximately 90 m (295 feet) long, the first 60 m (196 feet) of which is paved, while the opposite end has a paved RESA that is 60 m (196 feet) long.
Following the TSB’s investigationTSB Aviation Investigation Report A05H0002. into a runway overrun involving an Airbus A340-313 aircraft in 2005 at Toronto/Lester B. Pearson International Airport (CYYZ), Ontario, the Board recommended that
the Department of Transport require all Code 4 runways to have a 300 m runway end safety area (RESA) or a means of stopping aircraft that provides an equivalent level of safety.
TSB Recommendation A07-06
In response to the recommendation, Transport Canada (TC) updated regulations to require Canadian-certified aerodromes that are demonstrated to have a passenger count for scheduled service of 325 000 or more over a period of 2 years increase the length of their RESAs to a minimum of 150 m.
In its September 2023 response, TC indicated that no further action will be taken to address the residual risk represented by the gap between TC’s regulations and the International Civil Aviation Organization (ICAO) standard and recommendation.The current ICAO standard for all runways greater than 1200 m requires a RESA that is a minimum of 90 m (300 feet) beyond the runway strip, which must extend at least 60 m (196 feet) beyond the runway end including any stopway, both of which must total a minimum of 150 m (496 feet) in length where the surface is cleared, graded, and devoid of non-frangible objects. Therefore, in March 2024, the Board considered TC’s response to be Satisfactory in Part and the deficiency file was closed.TSB Recommendation A07-06: Runway end safety area (RESA) requirements, at www.tsb.gc.ca/eng/recommandations-recommendations/aviation/2007/rec-a0706.html (last accessed on 15 December 2025).
Airports in Canada that exceed the passenger count criteria for scheduled service will have 3 years to comply with the updated RESA requirements, which came into force in December 2021. Since the passenger count at CYKF exceeded 325 000 in 2022 and 2023, the airport will be required to comply by 2026 if its passenger count continues to exceed 325 000 per year.
The RESAs for Runway 08/26 at CYKF met the requirements at the time that the runway was built. It should be noted that beyond either end of Runway 08/26 there is a relatively flat, grassy area extending in excess of 150 m from the end of the paved surfaces, effectively acting as a RESA.
There is a control tower at the airport, which operates daily during the hours of 0700 to 2300. When the tower is not open, the airport is uncontrolled.
1.11 Flight recorders
The aircraft was equipped with a solid-state flight data recorder, which contained approximately 27 hours of flight data, covering the occurrence flight and 6 previous flights. The flight data recorder data was successfully downloaded.
The aircraft was also equipped with a cockpit voice recorder, which had a recording capacity of 120 minutes. Its recorded data was successfully downloaded and contained good-quality audio of the occurrence flight.
1.12 Wreckage and impact information
The aircraft exited the runway onto wet grass. The wheels created ruts in the surface that caused the aircraft to decelerate more quickly. The underside of the aircraft was splashed with mud and dirt.
1.13 Medical and pathological information
1.13.1 Fatigue
Sleep-related fatigue is a phenomenon widely reported in the transportation industry, including aviation. Fatigue is due to insufficient good-quality sleep. Generally, adults need from 7 to 9 consecutive hours of sleep each night to feel well-rested.M. Hirshkowitz, K. Whiton, S.M. Albert et al., “National Sleep Foundation’s sleep time duration recommendations: methodology and results summary,” Journal of the National Sleep Foundation by Elsevier Inc. in Sleep Health 1 (2015), pp. 40-43.
Sleep is a fundamental biological need that must be satisfied. If it is not, a sleep debt can result, either because of the significant reduction of a single sleep period (acute sleep disruption) or because of a sleep debt that is built up over time (chronic sleep disruption).
A pilot’s work may involve irregular and lengthy duty hours, night flights, unpredictable duty rosters, and commutes of various distances to and from their work. These factors can contribute significantly to fatigue by affecting how much restorative sleep the pilots obtain.
Non-work-related factors (e.g., personal issues, aging, medical problems, and alcohol use) can also limit a pilot’s opportunity to obtain restorative sleep.
An examination of the sleep history of both pilots indicated that the captain was likely fatigued during the occurrence approach and landing. This was largely due to irregular and insufficient rest before the occurrence, which happened during a circadian low, late in the shift.
Although both pilots had been awake for approximately 18 hours before the occurrence, the captain had not had sufficient restorative sleep in the days leading up to the event, exacerbating his level of fatigue.
The flight crew hours of work and methods used to evaluate the presence of fatigue are described in more detail in sections 1.13.1.2 Flight crew hours of work and rest periods and 1.13.1.3 Fatigue risk factors.
1.13.1.1 Circadian rhythm, alertness, and vigilance
The time of day has a strong effect on an individual’s alertness and performance because of changes in body physiology that are synchronized to a circadian (daily) rhythm. The human body is physiologically ready for sleep at night and for wakefulness during the day.
Consequently, overall performance and cognitive functioning are at their worst during the night, particularly from around 0200 to 0600. This period, known as the window of circadian low, aligns with the daily minimum in core body temperature when sleepiness is greatest.International Civil Aviation Organization (ICAO), Doc 9966, Manual for the Oversight of Fatigue Management Approaches, Second Edition, Version 2 (2020), Glossary, p. xix.
Alertness changes with the time of day and in conjunction with the body’s temperature cycle, peaking in the daytime and decreasing to its lowest during nocturnal hours.S. Saba Naz, M. Muddassar Shafiq, and M. Albreiki, “Interaction between Melatonin, Sleepiness-Alertness and Body Temperature,” in Sleep Medicine – Asleep or Awake? (24 July 2023). This decrease during nighttime hours affects most types of human cognitive performance, including processing speed, working memory, visual attention, and vigilance.T. Vlasak, T. Dujlovic, and A. Barth, “Neurocognitive impairment in night and shift workers: a meta-analysis of observational studies,” in Occupational and Environmental Medicine (2022), Vol. 79, Issue 6, pp. 365-372.,S.L. Chellappa, C.J. Morris, and F. Scheer, “Daily circadian misalignment impairs human cognitive performance task-dependently,” in Sci Rep, (14 February 2018).
Vigilance is associated with a state of sufficient alertness to monitor the environment effectively, with a particular emphasis on scanning for stimuli that signal a potential hazard.B.S. Oken, M.C. Salinsky, and S.M. Elsas, “Vigilance, alertness, or sustained attention: Physiological basis and measurement,” in Clinical Neurophysiology (2006), Vol. 117, pp. 1885–1901. Decreased vigilance has been shown to reduce the overall detection rate of critical stimuli over the duration of a task.J. Deaton and R. Parasuraman, “Effects of task demands and age on vigilance and subjective workload,” in Proceedings of the Human Factors and Ergonomics Society Annual meeting (1997), Vol. 32, pp. 1458–1462.
Vigilance, especially psychomotor vigilance in which people have to respond to a stimulus with some form of body movement (for example, pressing a button as soon as a light appears), is known to be impaired by fatigue.M. Ingre, T. Åkerstedt, B. Peters, et al., “Subjective sleepiness, simulated driving performance and blink duration: Examining individual differences,” in Journal of Sleep Research, Vol. 15 (2006), pp. 47-53.
1.13.1.2 Flight crew hours of work and rest periods
While the work histories for the flight crew in the week preceding the occurrence met the requirements of the Canadian Aviation Regulations (CARs),Transport Canada, SOR/96-433, Canadian Aviation Regulations, Subpart 700, Division III: Flight Crew Member Fatigue Management. the captain had accumulated a significant sleep debt during the week before the occurrence and had been awake for almost 18 consecutive hours at the time of the occurrence.
The occurrence flight was the captain’s 3rd overnight flight assignment in the 4 days leading up to the occurrence. His schedule was as follows:
- he was on flight duty from 1845 on Monday to 0654 on Tuesday;
- he had 2 short naps during the daytime hours on Tuesday, after his duty was over;
- his duty on Wednesday morning began at 0045 and ended at 0749;
- once off duty on Wednesday, he remained awake until midnight;
- on Thursday, he slept intermittently for 12 hours beginning at midnight and waking at 1230; and
- his duty on Thursday night started at 1850 and continued until the occurrence at 0625 Friday.
The captain had a period of approximately 20 consecutive hours (Monday afternoon to Tuesday morning) without sleep 3 days before the occurrence and a period of approximately 25 consecutive hours (beginning late Tuesday night and spanning most of Wednesday) without any sleep 2 days before the occurrence.
While the captain’s time off duty was in compliance with the regulations and should have allowed for sufficient rest, his schedule, including reserve duty time and delayed flights, combined with personal commitments and a 90-minute commute, may have affected his ability to prioritize rest effectively during this period. Before the beginning of his duty day, the captain carried out a self-assessment and determined that he was fit for duty.
The first officer had 4 days off before the flight and was likely well-rested. Although the occurrence happened late in the shift and after 18 hours of wakefulness, the first officer had taken measures to reduce fatigue by adjusting his sleep/wake pattern during the days leading up to the occurrence flight. The first officer had not accrued any sleep debt and was likely not fatigued during the occurrence.
Appendix A shows the work–rest schedules leading up to the occurrence for the captain and first officer.
1.13.1.3 Fatigue risk factors
There are 6 risk factorsTransportation Safety Board of Canada, Guide to Investigating Sleep-related Fatigue (February 2022). that can cause fatigue: acute sleep disruptions, chronic sleep disruptions, continuous wakefulness, circadian rhythm effects, sleep disorders and other medical and psychological conditions, and illnesses or drugs that affect sleep or sleepiness (Appendix B).
The TSB investigated each of the 6 risk factors to determine whether they were present at the time of the occurrence.
The TSB investigation found that the following fatigue-inducing factors existed for the captain at the time of the occurrence:
- Acute sleep disruptions
- Chronic sleep disruptions
- Continuous wakefulness
- Circadian rhythm effects
All 4 fatigue risk factors were present at a level sufficient to cause fatigue.
First, the captain experienced both acute and chronic sleep disruptions, having periods during the week before the occurrence of up to 25 consecutive hours without sleep.
Second, the captain had been awake for nearly 18 consecutive hours at the time of the occurrence, increasing the risk of performance decrements, as continuous wakefulness for over 17 hours is known to heighten fatigue.
Third, the occurrence happened during the nighttime circadian low, when overall performance and cognitive functioning are at their lowest. Considering the number, magnitude, and combination of fatigue risk factors, the captain was likely fatigued during the occurrence approach and landing.
1.14 Fire
There was no indication of fire either before or after the occurrence.
1.15 Survival aspects
Not applicable.
1.16 Tests and research
1.16.1 TSB laboratory reports
The TSB completed the following laboratory reports in support of this investigation:
- LP124/2022 – Flight Data Analysis
- LP125/2022 – CVR Data Recovery
- LP127/2022 – NVM Recovery – AACU [antiskid/autobrake control unit]
1.17 Organizational and management information
Launched in 2017, Flair is based in Edmonton, Alberta. At the time of the occurrence, its fleet included 22 Boeing 737 aircraft, of which 3 (including the occurrence aircraft) were 737-800 models, and 19 were 737-MAX 8 models.
1.17.1 Fatigue management
The CARs offer prescriptive requirements to mitigate the risks and effects of fatigue. In 2018, there was a significant update to the CARs, introducing both prescriptive and performance-based approachesThis performance-based approach specifies objectives, or output standards, and allows the regulated entity to determine the means of compliance. to fatigue management that were in force at the time of the occurrence.
Under the prescriptive approach, which Flair has incorporated into its Company Operations Manual (COM), the flight-time limits are 1000 hours in any 365 consecutive days, 300 hours in 90 consecutive days, and 112 hours in 28 consecutive days.
The flight-duty period was adjusted to a maximum of 9-to-13 hours, depending on the start time and sectors flown. Rest periods were extended to 12 hours, or 11 hours plus travel time if the pilot is resting at home, or 10 hours if the pilot is in suitable accommodation provided by the air operator.
The regulations also extended the previous 8-hour limit for alcohol use, by prohibiting pilots from working within 12 hours of consuming alcohol.
Additionally, the new regulations introduced an option for air operators to develop and use a fatigue risk management system, under the performance-based approach, as an alternative for air operators that may have constraints in meeting the prescribed flight and duty time limits.
Major airlines were given 2 years, and smaller air operators 4 years, to implement these changes. Flair does not use a fatigue risk management system because it intends to continue complying with the prescriptive approach as noted above.
Beginning in September 2021, under the CARs Subpart 705 (Airline Operations), air operators were required to have in place a fatigue management training program for flight crew members that contains the following elements:
(a) personal fatigue management strategies relating to
(i) sleep hygiene,
(ii) lifestyle, exercise and diet, and
(iii) the consumption of alcohol and drugs;
(b) the impact of fatigue on aviation safety;
(c) sleep requirements and the science relating to fatigue;
(d) the causes and consequences of fatigue;
(e) how to recognize fatigue in themselves and in others;
(f) sleep disorders, their impact on aviation safety and treatment options; and
(g) human and organizational factors that may cause fatigue, including
(i) sleep quality and duration,
(ii) the impact of shift work and overtime,
(iii) the circadian rhythm, and
(iv) the effects of changes of time zones.Transport Canada, SOR/96-433, Canadian Aviation Regulations, subsection 705.124(4), (effective 20 September 2021).
Flair has implemented an online training module to satisfy the requirements listed above, although the onus still remains largely on flight crew members to be rested and fit for duty.
Flair’s safety management system (SMS)Flair Airlines Ltd., Safety Management System, Policy and Procedures, Revision 26 (01 November 2022). outlines an online training curriculum focusing on human factors in aviation, the impact of individual performance on the system, and the tools available to employees for error prevention. However, this document does not reference any training specifically tailored to fatigue management.
Similarly, Flair’s COMFlair Airlines Ltd., Company Operations Manual, Revision 53 (01 September 2022). addresses fatigue management for flight crew members by establishing a system that monitors flight times, duty periods, hours of work, rest periods, and time free from duty.
1.17.2 Reserve schedule
Similar to most other airlines, Flair schedules a number of pilots to be “on reserve” at any given time, to ensure that there are pilots available should the airline need to replace a scheduled crew member due to illness or other operational reasons, such as a crew member not having enough remaining time in the duty day to complete a flight.
Within Flair’s seniority-based bidding system, a reserve schedule is typically held by pilots with lower seniority because being on reserve is considered to be less desirable for most pilots.
At Flair, pilots on reserve may not know whether they will be flying until up to 90 minutes before they are required to report for duty, making it difficult to plan for appropriate rest. Their potential duty period could last as many as 18 hours from the beginning of their reserve period, although the actual flight duty maximum is 12.5 hours.
Pilots holding a fixed schedule know well in advance which flights they will be operating, so they are able to plan a personal schedule around their work schedule.
1.17.2.1 Flair’s reserve availability periods
At Flair, pilots on reserve can be scheduled for 1 of 3 reserve availability periods (RAPs). The RAP is a period of time of up to 14 hours during which a flight crew member must be available and ready to report for flight duty within 90 minutes.
The 3 standard RAPs assigned to Flair pilots are as follows:
- Reserve A is from 0400–1400
- Reserve B is from 1400–2359
- Reserve C is from 1300–2359
It is sometimes necessary for Flair to adjust the timing of a pilot’s reserve schedule, and there are regulations in place to ensure that this does not compromise the pilot’s ability to be sufficiently rested before the beginning of the adjusted RAP.
If Flair wishes to change a pilot’s RAP, it must give 12 to 32 hours’ notice, depending on the start time of the updated RAP. For example, when the amended reserve period falls during the pilot’s window of circadian low then 32 hours’ notice is required.Ibid., Appendix D: Flight Crew Member Fatigue Management, D.1: Definitions, pp. APP D-2, D-3.
For the same reason, flight crews must be notified between 12 and 32 hours in advance of being placed on reserve, again depending on whether the RAP spans the pilot’s window of circadian low.
The onus is on the reserve pilots to ensure that they can report for duty within 90 minutes during their RAP. While on reserve, it is not uncommon for pilots who are not able to travel from their home to the airport within 90 minutes to find accommodation closer to the airport at their own expense in order to meet this requirement.
1.17.2.2 Maximum reserve- and flight-duty periods
According to the Flair COM, a reserve duty period is the total time from the start of the reserve availability period to the end of an assigned flight-duty period. Total duty may not exceed either 14 or 18 hours, depending on the start time of the reserve period.
For example, if reserve duty begins between 0200 and 1759, the maximum duty is 18 hours, and if reserve duty begins between 2300 and 0159, which includes the window of circadian low, the maximum duty is 14 hours.Ibid., D.19: Flight Crew Member On Reserve, p. APP D-21.
Since flight duty can be assigned after the reserve availability period has already begun, the maximum length of a flight-duty period can be different from the maximum length of a reserve duty period, which includes both the RAP and the flight duty.
The maximum flight-duty period varies from 9 to 12.5 hours depending on the start time of the flight-duty period and the number of flights to be flown during that period.
According to the Flair COM, the maximum flight duty for the occurrence flight assignment was 12 hours because the start time was between 1700 and 2159 and the assignment included fewer than 5 flights.Ibid., Table D.1: Maximum Flight Duty Period (Average Flight Duration 50 Minutes or More), p. APP D-6. At the time of the occurrence, the flight crew had been on duty for 11.4 hours.
1.17.3 Controlled rest on the flight deck
The Flair COMIbid., D.21: Controlled Rest on the Flight Deck, p. APP D-23. allows for controlled rest on the flight deck during which 1 flight crew member may obtain rest with their eyes closed for a maximum of 45 minutes during flight.
During the occurrence flight, the flight crew was unable to utilize controlled rest because a passenger medical issue requiring the attention of the flight crew arose during the cruise portion of the flight, when controlled rest would have been possible.
Regarding the purpose and permitted usage of controlled rest on the flight deck, TC indicated the following in an Advisory Circular published May 2022:
The opportunity for FCMs [flight crew members] to take controlled rest on the flight deck cannot be guaranteed; therefore it cannot be planned by an air operator as an ongoing fatigue risk control or mitigation measure to address the causes of the fatigue-related hazards produced by the variance.Transport Canada, Advisory Circular (AC) 700-045: Exemption and Safety Case Process for Fatigue Risk Management Systems (Issue 03: 02 May 2022), paragraph 6.3.4(2)(c).
1.17.4 Standard operating procedures
The Flair Flight Crew Operating Manual (FCOM) is based on Boeing’s FCOM. Included are standard operating procedures (SOPs) designed to ensure flight crews are conducting flight operations according to a common standard.
For manually or automatically selected AFDS mode changes, flight crews are required to use the FMA to verify these changes.
Announcing changes on the FMA and thrust mode display when they occur is considered a good crew resource management (CRM) practice.Flair Airlines Ltd., B737-800 Flight Crew Operating Manual, Volume 1, Revision 21 (02 August 2022), Chapter NP: Normal Procedures, Introduction, Autopilot Flight Director System (AFDS) Procedures, p. NP-11-12.
The procedure for a normal approach requires pilots to disengage the autothrottle at the same time that they disengage the autopilot.Ibid., Amplified Procedures, Landing Procedure – ILS CAT I, p. NP-21-56.
Data captured as part of Flair’s flight data monitoring program showed many instances in which Flair pilots had continued to allow the autothrottle to manage thrust well after disengaging the autopilot during approaches, often until they were ready to retard the throttles for landing.
Following the occurrence, Flair reminded its pilots of the SOP requirement to disengage the autothrottle at the same time as the autopilot.
Many other transport-category aircraft operators do allow for the autothrottle to be used during approach after the autopilot has been disengaged. The captain of the occurrence flight had significant experience working with other operators where this was common practice.
1.17.5 Operations with single thrust reverser available
There are only 2 items in either Flair’s FCOM or COM pertaining to operating with 1 thrust reverser inoperative: a limitation preventing dispatch to runways less than 148 feet wide with 1 thrust reverser inoperative,Ibid., Chapter L: Limitations, Limitations and Operational Information, Aircraft General, p. L-10-2. and a reminder that the wet runway/obstacle limited weight and V1 must be reduced to account for the effects of having only one thrust reverser available on accelerate-stop performance.Ibid., Chapter PI: Performance Inflight, Text, Thrust Reverser Inoperative, p. PI-27-4.
The MEL requires an inoperative thrust reverser to be locked in the forward thrust position and placarded as noted in the aircraft’s MELFlair Airlines Ltd., Minimum Equipment List (MEL): Boeing 737-800, Revision 10 (29 September 2022), item 78-01, p. 78-1., and that performance considerations be made by pilots when calculating takeoff-related performance parameters. Lockwire, which was used in this case, is one way to ensure that the requirement to lock the thrust reverser is met.
1.17.5.1 Training
While pilots have the opportunity to practise using a single thrust reverser during 1-engine inoperative landings in the simulator, they do not practise landings with both engines operating and 1 reverse thrust lever locked in the stowed position, nor do they practise any scenarios involving inadvertent mode selections.
Boeing’s 737 NG Flight Crew Training Manual includes a diagramThe Boeing Company, 737 NG Flight Crew Training Manual, Revision 21 (30 June 2022), Chapter 6: Landing, Landing Roll, Reverse Thrust Operation, p. 6.44. depicting the pilot’s hand position when operating the reverse thrust levers (Figure 12).
Flair pilots are trained to maintain physical contact with the forward thrust levers using the palm of their hand or their forearm when operating the reverse thrust levers, although it is not a comfortable or natural hand position to maintain while using reverse thrust, especially while using only a single reverse thrust lever.
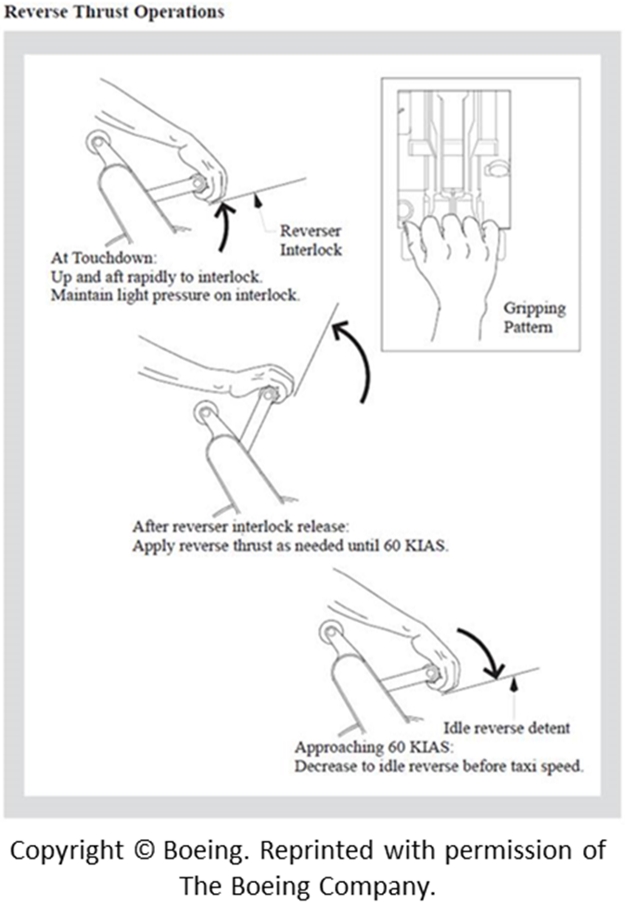
There are no instructions in the Flair FCOM regarding the pilot’s hand positioning while manipulating the reverse thrust levers.
According to Boeing’s 737 NG Flight Crew Training Manual and 737-600/-700/-800/-900/-900ER Flight Crew Operations Manual, a full-stop landing must be made after reverse thrust has been initiated.Ibid., p. 6.43.,The Boeing Company, 737-600/-700/-800/-900/-900ER Flight Crew Operations Manual, Revision 51 (30 September 2022), Landing Roll Procedure, Warning, p. NP.21.76.
1.17.6 Flair’s approved maintenance organization
Flair is approved by TC to perform maintenance under an AMO certificate. The certificate authorizes the AMO to conduct maintenance on the Boeing 737 series aircraft with a limited scope of work and perform non-specialized maintenance up to, but not including, C-checks.A comprehensive aircraft inspection conducted at a specific calendar interval (roughly every 20-24 months), or after a specific number of flight hours as defined by the manufacturer.
Flair operates approved maintenance facilities in Calgary, Alberta, and Edmonton, and has access to a full-sized hangar at CYKF for maintenance on an ad-hoc basis. The company also subcontracts scheduled and unscheduled maintenance to third-party AMOs at various other airports.
The occurrence aircraft was maintained under a TC-approved maintenance schedule, issued pursuant to CARs Standard 625, appendices C and D.
1.17.6.1 Maintenance control
The main functions of Flair’s maintenance control centre are maintenance planning and coordination. There are normally 8 maintenance controllers, working in pairs on 12-hour shifts, to ensure availability 24 hours a day, 7 days a week.
Each maintenance controller is also authorized by Flair as an aircraft certification authorityAn individual authorized to sign a maintenance release for work performed on an aircraft. and holds an aircraft maintenance engineer licence in the applicable category.
The group maintains communication with subcontracting AMOs with regards to defect rectification or deferral. The maintenance controller ensures that correct parts are ordered, tracked, and scheduled for delivery to the applicable location where the part is needed to rectify or troubleshoot a maintenance issue.
All information related to maintenance planning and tracking is updated daily in Flair’s maintenance, repair, and overhaul tracking system.
1.17.6.2 Defect reporting
The company-approved maintenance control manual states that all discrepancies must be documented in the discrepancy field of the aircraft’s journey log by either maintenance personnel or the flight crew.Flair Airlines Ltd., Maintenance Control Manual, Revision 39 (17 March 2022), Section 4: Maintenance Reporting and Rectification, Subsection 4.4: Unplanned Maintenance – Discrepancies, p. 4-2.
The CARsTransport Canada, SOR/96-433, Canadian Aviation Regulations, section 605.94, Division IV, Schedule 1, item 9. state that the pilot-in-command is responsible for entering in this log the particulars of any defect in any part of the aircraft that becomes apparent during flight operations as soon as is practicable and, at the latest, before the next flight.
Once a discrepancy is entered in the journey log, it must be either rectified or deferred before the aircraft can be dispatched on a flight.
1.17.6.3 Deferred and recurrent defects
The CARs require an air operator’s defect recording system to include a method of highlighting recurring defects so they are readily identifiable by flight crews and maintenance personnel at all bases where the air operator’s aircraft operate.
In the Commercial Air Service Standards (CASS), it is also stated that the air operator is responsible for ensuring that its maintenance personnel are aware of recurring defects to avoid duplication of unsuccessful attempts at rectification.Transport Canada, Commercial Air Service Standards, section 726.05: Defect Recording and Control.
The regulations define a recurring defect as one in which “a failure mode is repeated three times on a particular aircraft, within 15 flight segments of an approved repair made in respect of that failure mode.”Ibid., subsection 726.05(3).
The Flair maintenance, repair, and overhaul tracking systemAMOS is the maintenance, repair, and overhaul tracking system used by Flair Airlines Ltd. It is developed and supplied by Swiss Aviation Software. will generate an alert if 3 defects in the same 2-digit Air Transport Association chapter numberThe Air Transport Association numbering system is a common reference standard used in commercial aircraft documentation. occur within 15 flight segments of the aircraft. The alert will be evaluated to determine if the defects are related so that appropriate maintenance action can be initiated through the issuance of a work order.
The Flair Maintenance Control Manual indicates that a recurring defect exists only when a related discrepancy occurs a fourth time in 15 flights (3 re-occurrences),Flair Airlines Ltd., Maintenance Control Manual, Revision 39 (17 March 2022), Section 4: Maintenance Reporting and Rectification, Subsection 4.8: Recurring Discrepancy Procedure, p. 4-6. as per the regulations.
The system does not generate a notification if a defect re-occurs outside of these parameters.
1.17.6.4 Left thrust reverser fault history
Beginning in May 2022, a defect with the left thrust reverser on the occurrence aircraft was reported by flight crews, and the most common report was that the left REVERSER indicator light remained ON on the overhead engine panel after the thrust reversers were stowed (deactivated), indicating a fault with the system.
The aircraft Fault Isolation Manual (FIM)The Boeing Company, Fault Isolation Manual (15 June 2016), Section 801: Engine Accessory Unit (EAU) Bite Procedure. is used by maintenance personnel during the troubleshooting process. In the case of a thrust reverser issue, the FIM requires checking the engine accessory unit (EAU), which provides an indication of which part of the system is faulty. Once the results of the test have been recorded, the fault code history is reset, which also resets the REVERSER indicator light on the overhead panel on the flight deck.
To confirm that the fault is no longer present, maintenance personnel can cycle the thrust reversers on the ground after performing this reset. If the REVERSER indicator light does not re-activate, the defect is no longer present and can be considered resolved, even though no part of the system has been cleaned, adjusted, repaired, or replaced by maintenance.
This reset procedure is the fastest way to get the aircraft back into service while complying with regulations, although it does not address the underlying issue that caused the indicator light to illuminate.
It is also common to return an aircraft to service by deferring an item, provided that it may be deferred according to the aircraft’s MEL. The MEL also details the maintenance and operational procedures to be used while the defect is deferred, and provides a timeframe within which the defect must be repaired.
Between 09 May 2022 and 24 November 2022, there were 23 defects recorded in the aircraft journey log related to the left thrust reverser.
During this time period, there were 18 occasions where the only maintenance action taken was to reset the EAU and cycle the reverse thrust levers. These resets were performed by 6 different AMOs at 10 different Flair destinations.
The MEL was applied on 6 occasions, although in one instance the only action taken before clearing the MEL was to reset the EAU. In 3 instances, a 10-day MEL extension was applied, including the extension in effect at the time of the occurrence due to the replacement parts being unavailable. The left thrust reverser had been deactivated and locked in the stowed position for a total of approximately 50 days between the time the defect was first reported and the day of the occurrence.
Records indicate that, on 09 May 2022, when the first defect related to the left thrust reverser was recorded in the aircraft journey log, a subcontracting AMO identified the likely cause of the defect to be a failure of the left autothrottle switchpack, based on guidance found in the FIM.
Parts requisitions were submitted to Flair on 20 May 2022 with a “rush” designation, meaning the part was required within 3 to 5 days. There was no documented action on the part of the Flair AMO to fulfill or approve the request.
On 12 June 2022, an identical request was made, again with no documented action taken to fulfill or approve the request. The investigation could not determine why these requests were not actioned.
On 17 June 2022, after 6 system resets and 10 days on the MEL, the first recorded maintenance action beyond a system reset was performed on the left thrust reverser system: an electrical connector was cleaned, but the autothrottle switchpack was not ordered. Three other parts were replaced during the next 4 months in an attempt to resolve the issue.
On 10 November 2022, the part order for the autothrottle switchpack, which was first requested in May 2022, was approved by the Flair AMO. After the occurrence, the replacement of the left autothrottle switchpack resolved the persistent issue with the left engine thrust reverser.
A table containing a detailed timeline of the left thrust reverser defect can be found in Appendix C.
The CARs require that air operators include in their maintenance control system a means to record aircraft defects, ensure that defects are rectified in accordance with the requirements of the regulations, and detect and identify those defects that recur.Transport Canada, SOR/96-433, Canadian Aviation Regulations, section 706.05.
Further details regarding the handling of recurring defects are found in the CASS:
(1) Pursuant to section 706.05 of the CARs, the defect recording system has to include a method to highlight defects that recur, so that they are readily identifiable by flight crews and the maintenance organization at all bases where the aircraft is operated. The air operator is responsible for identifying defects as recurring defects to maintenance personnel in order to avoid the duplication of unsuccessful attempts at rectification.
(2) Pursuant to section 706.05 of the CARs, the defect control system has to ensure that the rectification of a defect identified as a recurring defect will take into account the methodology used in previous repair attempts.
(3) For the purposes of these standards, defects are recurring defects if a failure mode is repeated three times, on a particular aircraft, within 15 flight segments of a previous repair made in respect of that failure mode.Transport Canada, Commercial Air Service Standards, section 726.05: Defect Recording and Control.
Finding: Other
Flair Airlines Ltd’s maintenance, repair, and overhaul tracking system was capable of identifying recurring defects as defined by regulations, but its capabilities did not extend to identifying defects such as the left thrust reverser fault in this occurrence, which did not meet the definition of a recurring defect. The defect had been reported 23 times during the 6 months leading up to the occurrence.
1.17.6.5 Continuity in system troubleshooting
A review of technical records showed that, starting in May 2022, the reported defects related to the left thrust reverser were addressed by 6 AMOs.
While Flair’s maintenance control centre received technical records generated by each subcontracting AMO, those records are not required to have, and often do not include, a detailed account of unsuccessful troubleshooting attempts or steps taken to rectify a defect. As a result, there was little or no information available about previous troubleshooting efforts when the same defect occurred at a different location.
Throughout this time period, each AMO conducted troubleshooting according to the FIM. In the absence of information from previous troubleshooting efforts at other AMOs, they were compelled to follow the FIM from the beginning, duplicating the efforts of previous troubleshooting efforts without progressing towards a better understanding of the nature of the defect.
1.17.7 Safety management system
As an airline and an AMO operating and maintaining aircraft under subparts 705 and 573 of the CARs, Flair is required to establish and maintain an SMS. Flair’s safety management policy manualFlair Airlines Ltd., SMS Policy Manual, Revision 26 (01 November 2022). describes the airline’s SMS.
Under its SMS, the company is required to identify hazards and carry out risk management analysis of those hazards.
The SMS also includes requirements to investigate, analyze, and identify the cause or probable cause of all hazards, incidents, and accidents, as well as provide a method for monitoring and evaluating the results of corrective actions with respect to these hazards, incidents, and accidents.
Employees and applicable subcontractors are expected to report on hazards, incidents, and accidents related to Flair’s operations.
1.17.7.1 Examination of safety management system reports
The investigation examined Flair’s SMS reports for the year leading up to the occurrence to identify whether issues similar to the occurrence flight had been adequately resolved by the SMS. The results of the examination are discussed in the following sections.
1.17.7.1.1 Inadvertent takeoff / go-around selections
Flair SMS reports dating back to January 2021 were examined to determine whether there were any previously reported instances of inadvertent TO/GA selections during approach. The investigation determined that 3 instances had been reported, and in each case, the flight crew became aware of the inadvertent activation shortly after it occurred:
- During the 1st occurrence, the inadvertent activation occurred at approximately 425 feet AGL, and the PF disconnected the autothrottle and continued to a normal landing.
- During the 2nd occurrence, the PF pressed the TO/GA button instead of the AT DISC switch while on short final, and the aircraft continued to a normal landing.
- The 3rd occurrence happened at approximately 500 feet AGL when a first officer undergoing line indoctrination pressed TO/GA instead of AT DISC after having been briefed that a go-around may be necessary due to the spacing of the aircraft ahead. The flight crew initiated a go-around followed by a 2nd successful approach and landing.
All 3 occurrences were classified by Flair as low risk, given that the inadvertent mode selection was identified quickly, and adequate steps were taken to continue the flight safely. Flair noted that its SOPs are designed to mitigate the risk by requiring that the autothrottle be disengaged at the same time as the autopilot.
1.17.7.1.2 Persistent thrust reverser defect
The investigation determined that the persistent issue with the left thrust reverser, which began in May 2022, had not been entered in the SMS as an identified hazard for risk analysis, although it was reported that the issue was known and being managed by Flair’s maintenance control centre in coordination with the contracted AMOs. Aircraft defects are not normally entered into the SMS.
The associated risks of prolonged operation of an aircraft with an inoperative system such as a thrust reverser had not been assessed for potential mitigations and/or corrective actions.
1.18 Additional information
1.18.1 Transport Canada
1.18.1.1 Surveillance activity
The investigation examined TC surveillance records of Flair for a period dating back to 2 years before the occurrence. During those 2 years, TC conducted 1 planned Process InspectionA process inspection (PI) is “an in depth review of an enterprise process utilised to produce an output to verify whether it functions or not.” (Source: Transport Canada, Staff Instruction [SI] SUR-001: Surveillance Procedures, Issue 06 [22 June 2016], section 2.3.) (PI), 1 reactive PI, and 1 targeted inspection related to mitigating risks during the COVID-19 pandemic.
Frequency of inspection is determined by a risk evaluation carried out by TC that takes into account the size and scope of an operation, its area of operations, previous occurrence history, and other factors.
The planned PI was conducted in October 2020 and was limited to operational dispatch, cabin safety requirements, and AMO quality assurance. Flair was found to be in compliance in all areas examined during the PI.
The reactive PI was conducted in May 2022 and was related to safety oversight and flight-duty times. A corrective action plan was agreed upon in August 2022 and the PI was closed on 21 December 2022.
There were no records to indicate that the operator’s maintenance control system had been examined as part of TC surveillance during the 2-year period. TC’s surveillance planning policy does not require inspectors to examine any specific portions of an operation.
Decisions concerning areas of the operation to be inspected are made by the technical team leaders responsible for the air operator in question and are often based on other information gathered by inspectors or trends found in TC’s Civil Aviation Daily Occurrence Reporting System.
Shortly after the occurrence, TC conducted a reactive PI focused on operational dispatch as it applied to the flight crew during the week leading up to the occurrence flight. The limited scope PI did not find any discrepancies.
1.18.2 Human factors
1.18.2.1 Crew resource management
The objective of CRM is to reduce human error in aviation. The definition of CRM is widely accepted to mean the use of all human, hardware, and information resources available to the flight crew to ensure safe and efficient flight operations.
In a multi-crew aircraft such as the Boeing 737-800, pilots must successfully interact with each other, their aircraft, and their environment, using associated checklists and company SOPs to effectively manage any threats, errors, or undesired aircraft states that may be encountered.
Researchers have recommended that CRM training should be based on the underlying premise that human error is inevitable and cannot be entirely eliminated and therefore CRM is used as “a set of error countermeasures with three lines of defense.”R.L. Helmreich, A.C. Merritt and J.A. Wilhelm, “The Evolution of Crew Resource Management Training in Commercial Aviation,” University of Texas at Austin Human Factors Research Project 235 (1999).
The 1st defence is avoiding error; the 2nd defence is trapping errors before they lead to adverse consequences; and the 3rd defence is mitigating the consequences of errors that occurred but were not trapped.
Modern CRM theory and training now include this premise, and TC defines a contemporary CRM as a method that:
integrates technical skill development with communications and crew coordination training and operational risk management by applying threat and error management (TEM) concepts.Transport Canada, Advisory Circular (AC) 700-042: Crew Resource Management (CRM), Issue 02 (14 March 2020), section 2.3.
1.18.2.2 Threat and error management
TEM is now considered a key component of effective CRM. The TEM framework has several potential applications, including organizational safety management and flight crews conducting risk assessments.
The key principles of TEM are anticipation of, recognition of, and recovery from threats and errors. It advocates carefully analyzing potential hazards and taking appropriate steps to avoid, trap, or mitigate threats and errors before they lead to an undesired aircraft state.
Flight crews may trap an error by identifying and correcting it, exacerbate an error by making a subsequent error, or have no effect on the error as a result of not detecting it or ignoring it.International Civil Aviation Organization (ICAO), document no. 9803, Line Operation Safety Audit (LOSA), First Edition (2002), p. 2–4.
The TEM model identifies 5 types of errors:Ibid., p. 2-3.
- intentional non-compliance errors ([deviations from] SOPs)
- procedural errors (slips and lapses in the application of procedures)
- communication errors (information is incorrectly transmitted or interpreted)
- proficiency errors (skill or knowledge is lacking to manage the aircraft)
- operational decision errors (where a decision is taken that increases the risk of the flight)
Error management on the flight deck involves vigilance, assertiveness, and continuous inquiry. Although threats and errors are common in flight operations, they rarely carry significant consequences because they are effectively managed by the crew.
The effective management of risks on the flight deck is inextricably linked to effective CRM.
When managing errors:
[r]egardless of the type of error, an error’s effect on safety depends on whether the flight crew detects and responds to the error before it leads to an undesired aircraft state and to a potential unsafe outcome. This is why one of the objectives of TEM is to understand error management (i.e., detection and response), rather than solely focusing on error causality (i.e., causation and commission).D. Maurino, “Threat and Error Management (TEM),” presented at the Canadian Aviation Safety Seminar, Vancouver, BC (April 2005).
1.18.2.3 Crew resource management training
Subsection 725.124(39) of the CASS requires airline operators covered under Subpart 705 of the CARs to provide all crew members (flight crew, flight attendants, dispatchers/flight followers, ground crew, and maintenance personnel) with both initial and annual recurrent CRM training. Initial CRM training is required to cover the following subjects:
(i) threat and error management;
(ii) communications;
(iii) situational awareness;
(iv) pressures and stress;
(v) fatigue;
(vi) workload management;
(vii) decision making;
(viii) leadership and team building;
(ix) automation and technology management; and
(x) relevant case study.Transport Canada, Commercial Air Services Standards, subsection 725.124(39).
Flair provided initial and recurrent CRM training to all crew members in accordance with the existing regulations.
A review of the captain’s training record showed that he completed his initial CRM training on 01 March 2022 during his initial training at Flair.
A review of the first officer’s training record showed that he completed his initial CRM training on 20 May 2022 during his initial training at Flair.
1.18.2.4 Pilot decision making and situational awareness
Decision making in general is a cognitive process that involves identifying and choosing a course of action from several alternatives.American Psychological Association, APA Dictionary of Psychology, https://dictionary.apa.org (last accessed on 22 January 2025). Decision making for pilots occurs in a dynamic environment and includes 4 steps: gathering information, processing information, making a decision, and acting on that decision.
Situational awareness is integral to pilot decision making. Pilots need to have an understanding of the relevant elements involved, a comprehension of their meaning, and the ability to project their future state.M.R. Endsley, “Design and evaluation for situation awareness enhancement,” in Proceedings of the Human Factors Society: 32nd Annual Meeting (Santa Monica, California: 1988), pp. 97–101.
It is important that each pilot establish this situational awareness, but it is also important that flight crew members communicate effectively to establish and maintain a common, shared situational awareness.
1.18.2.5 Shared situational awareness and mental models
Flight crew members must have a common, shared situational awareness;M.R. Endsley, "Toward a Theory of Situation Awareness in Dynamic Systems," in Human Factors, Volume 37, Issue 1 (1995), pp. 32-64. ,E. Salas, C. Prince, D.P. Baker, and L. Shrestha, "Situation Awareness in Team Performance: Implications for Measurement and Training," in Human Factors, Volume 37, Issue 1 (1995), pp. 123–136. that is, one pilot’s awareness of the situation is consistent with that of the other pilot’s. With a common understanding, flight crews can effectively anticipate and coordinate their actions and perform in an efficient and safe manner to manage threats.
SOPs and checklists are critical information resources that provide procedural guidance to pilots for the operation of an aircraft. They assist with pilot decision making and establishing shared mental models by providing pilots with predetermined successful solutions to various situations while also accounting for risk factors that may not be readily apparent to a pilot during normal operations or an abnormal/emergency situation.
1.18.2.6 Adaptations (deviations from standard operating procedures)
Adaptations are decisions to deviate from formalized rules or procedures. They are intentionally performed, with the individual being aware that such actions are contrary to the rules.
Adaptations are often a result of not fully understanding the purpose of the rule or procedure, not anticipating the potential consequences of deviating from the rule or procedure, or from perceiving that the work can be accomplished more efficiently through an adaptation. Adaptations can be systemic practices not unique to one person or one crew.
While companies prescribe policies and SOPs to set boundaries for safe operations, individuals may occasionally make decisions to not stay within those limits. When these decisions are repeated over time, this variance results in adaptations of the procedures themselves and in deviation from prescribed limits, leading to unsafe practices.J. Rasmussen, “Risk Management in a Dynamic Society: A Modeling Problem,” in Safety Science, Volume 27, Issue 2/3 (1997), pp. 183–213.
Without intervention, the communication of successful adaptations between crew members tends to lead to the spread of adaptations throughout an organization. Such adaptations are unlikely to be recognized as deviations by those within the group employing them. The adaptations slowly become normal behaviour, and the risk associated with them is unlikely to be recognized, particularly when there are no adverse consequences.S. Dekker, Drift into Failure (Ashgate Publishing, 2011), p. 111.
1.18.2.7 Skill-based performance (slips in the application of procedures)
There are 3 general ways to classify human performance from an information-processing perspective: skill-, rule-, and knowledge-based performance.J. Rasmussen, “Skills, Rules, and Knowledge; Signals, Signs and Symbols, and Other Distinctions in Human Performance Models,” in IEEE Transactions on Systems, Man, and Cybernetics, Volume SMC-13, No. 3, (May/June 1993), pp. 257-266.
Skill-based performance is observed in familiar situations and tasks that require very little attention to perform. Typically, these tasks are relatively routine, predictable, and highly practised.
The benefit of skill-based performance is that it is very fast and requires very little attention, freeing information-processing resources for other things. However, these benefits make it susceptible to slips, when the automatic routine is interrupted or disrupted during its execution and the interruption or disruption is not detected.
Slips occur when an individual intends to perform a specific action, but inadvertently carries out a different, unintended action. Slips resulting from attentional failures are likely to happen due to automatic or habitual sequences of action taking over.J. Reason, Human Error, Cambridge: Cambridge University Press (1990), pp. 68-72. Fatigue can further increase the likelihood of slips by reducing an individual’s attentional abilities and making it harder to detect or correct unintended actions, especially during routine tasks.
1.18.2.8 Priming effect
The priming effect happens when a stimulus in the environment affects a subsequent response by activating mental constructs without conscious realization.E. Weingarten, Q. Chen, M. McAdams, et al. (2016) “From primed concepts to action: A meta-analysis of the behavioral effects of incidentally presented words,” Psychological bulletin,142(5), p. 476. Priming occurs through a 3-step process.C. Loersch, and B.K. Payne, “Demystifying priming,” in Current Opinion in Psychology, Vol. 12 (December 2016), pp. 32-36.
First, a stimulus is perceived in the environment. This stimulus can be visual, auditory, or conceptual in nature.
Second, once the stimulus is perceived, it triggers the activation of related information stored in memory.
Third, the information is quickly activated in memory and subsequently affects an individual’s behaviour or response. This influence can manifest in various ways, such as altering decision making, judgement, or actions, often outside conscious awareness.
1.18.2.9 Design of controls and displays
The consequences of unintentional activation or movement of a control can create confusion or distraction. Design measures to reduce the likelihood of unintentional activation or movement are as follows:
- Visual and shape cues
- Adequate separation between controls
- Location and orientation of controls
- Sufficient control resistance
- Operation sequencing
- Locking or interlocking mechanisms
- Restricted access via a physical guard, recess, or position outside the normal reach of the pilotD. Harris, Human Performance on the Flight Deck (Ashgate Publishing, Ltd., (01 October 2012), pp. 97–98. , P.M., Burcham, US Army Research Laboratory, ARL-MR-337, Inadvertent Activation of Controls, Literature Search (October 1996).
The layout of flight-deck displays is designed to improve situational awareness and efficiency while reducing pilot workload. This takes into account several factors, including the ease of detection and salience of signals, prioritization of information based on its importance, and the intuitive grouping of controls and displays to facilitate quick and accurate responses.Federal Aviation Administration (FAA), HF-STD-001, Human Factors Design Standard for Acquisition of Commercial-Off-The-Shelf Subsystems, Non-Developmental Items, and Developmental Systems (May 2003), Section 3.7.15: Consider potential vigilance decrements, Section 5.1: Displays, Section 6.3.2.10: Arrangement by importance or frequency of use, and Section 6.1.1.3: Arrangement and grouping.
Another aspect of flight-deck layout design is the standardization of control and switch locations, along with their respective indicators. Standardization aims to enhance usability and reduce the potential for error by providing a consistent interface for pilots.Ibid., Section 2.4: Standardization and Section 2.5: Safety. However, maintaining consistency can be challenging due to the unique requirements and constraints of different aircraft types. Even within the same manufacturer, there is variance in the location and functionality of the autothrottle and TO/GA controls.
Pilots switching between aircraft types must adjust to different control and display layouts, leading to increased cognitive demand and the likelihood of operational errors.
1.18.3 TSB Watchlist
The TSB Watchlist identifies the key safety issues that need to be addressed to make Canada’s transportation system even safer.
Runway overruns are a Watchlist 2022 issue. While this occurrence did result in a runway overrun, there were no injuries to the occupants, and minimal damage to the aircraft. The slope and size of the grassy area beyond the published RESA for the runway in use essentially met the ICAO standard for RESAs, even though it was not officially classified as one. This occurrence serves to highlight the effectiveness of RESAs in mitigating the risks of runway overruns.
ACTIONS REQUIRED: Runway overruns:
Despite the actions taken to date, the number of runway overruns in Canada has remained constant since 2005 and demands a concerted effort to be reduced.
The issue of runway overruns will remain on the TSB Watchlist until
TC demonstrates that the residual risk at airports with runways that are not required to comply with ICAO’s 150 m standard [for RESAs] is as low as reasonably practicable; and
TC requires operators of airports with runways longer than 1800 m that have a RESA shorter than ICAO’s recommended length of 300 m to conduct formal runway-specific risk assessments and to take action to mitigate the risks of overruns to the public, property, and the environment.
Fatigue management in air transportation is a Watchlist 2022 issue. As this occurrence demonstrates, even if air operators are in compliance with existing regulations, flights or duty assignments requiring periods of extended wakefulness may result in a higher likelihood of pilot fatigue.
In December 2018, TC published new prescriptive requirements for managing flight crew fatigue in the Canada Gazette, Part II. The regulations had a staggered implementation period. Air operators subject to CARs Subpart 705 had until December 2020 to comply with the new requirements.
ACTION REQUIRED
The issue of fatigue management in air transportation will remain on the Watchlist until the TSB assesses the effectiveness of these new regulations on air transportation operations in Canada through its investigations.
1.18.4 Similar occurrences
A review of historical accident investigation reports,,including a TSB report from 2005National Transportation Safety Board of the United States, Accident Report NTSB/AAR-20/02 PB2020-101004: Atlas Air Flight 3591, 23 February 2019; Aircraft Accident Investigation Commission of Japan, Aircraft Accident Investigation Report: China Airlines Flight 140, 26 April 1994; Accident Investigation Board, Finland, Major Accident Report Nr 2/1994, 03 November 1994; Australian Transport Safety Bureau, Aviation Occurrence Investigation AO-2016-042: Engine nacelle strike and continued operation involving Boeing 737-8FE, YH-YIW, 23 April 2016; Transportation Safety Board of Canada, Aviation Investigation Report A05A0161: Wing Contact with Runway During Landing, 25 December 2005., and information gathered after a 2018 accidentPegasus flight 8622,13 January 2018. involving a Boeing 737-800 at Trabzon Airport (LTCG), Turkey, for which a public report was not released, indicate that inadvertent TO/GA activation has been involved in accidents and incidents dating as far back as the 1990s.
A 2005 International Air Transport Association Safety Trend Evaluation, Analysis and Data Exchange System report on automation errors showed that 45% of the reported auto-handlingAuto-handling refers to the use of automated systems in aircraft operations. incidents occurred in the approach phase.
Of those auto-handling incidents, multiple event reports cited specific handling errors, with mis-selections being a prominent concern. Such mis-selections included “unintended activation of the TOGA [takeoff /go-around] feature while attempting to disconnect the autothrottles during the approach phase.”IATA Safety Trend Evaluation, Analysis and Data Exchange System (STEADES), Automation Errors, Issue 4, (2005).
2.0 Analysis
There was no indication that any previously unknown or undetected mechanical aircraft defects were present at the time of the occurrence.
The flight crew held the appropriate licences and ratings for the flight in accordance with existing regulations.
This analysis will focus on the sequence of events that led to the runway overrun, beginning with the operational factors, including standard operating procedures (SOPs), fatigue, and crew assignments. It will then focus on the aircraft controls and displays, such as system status and indicators, system logic, single thrust reverser usage and braking. Finally, the analysis will discuss the handling of aircraft defect reports.
2.1 Operational factors
2.1.1 Standard operating procedures
Although the Flair SOP did require the autothrottle to be disengaged at the same time as the autopilot during the occurrence approach, some Flair pilots had been leaving the autothrottle engaged after disengaging the autopilot during approach.
The captain, who was the pilot flying (PF), decided to leave the autothrottle engaged after disengaging the autopilot. This adaptation to the SOPs was likely based on the captain’s previous flying experience with other operators where this was normal procedure. Leaving the autothrottle engaged until a point in the flight when both flight crew members were focused on landing the aircraft made it difficult for each of them to visually confirm whether the autothrottle disengagement had occurred.
Finding as to causes and contributing factors
The captain, who was the PF, left the autothrottle engaged after disengaging the autopilot as a result of a habit formed from past flying experience where the practice was permitted.
2.1.2 Fatigue and priming effect
Fatigue influences performance and cognitive functioning and can lead to errors related to attention and decreased vigilance (slips).
The investigation determined that 4 fatigue risk factors were present at levels sufficient to impact the captain’s cognitive functions. Operating the aircraft after nearly an 18-hour wake period and at the end of a circadian low reduced the captain’s attention and vigilance. The captain’s acute and chronic sleep disruptions from the preceding days exacerbated his fatigue level.
The inadvertent pressing of the takeoff/go-around (TO/GA) switch instead of the autothrottle disengage switch—a slip—is attributed to the detrimental effects of fatigue on the captain’s cognitive functions, making it more challenging for him to remain focused and execute tasks accurately. This inadvertent automatic flight director system mode change went undetected by the flight crew.
Priming occurs when a stimulus in the environment affects a subsequent response by activating mental constructs without conscious realization. When the captain tried to disengage the autothrottle, the go-around procedure, which had been mentally rehearsed earlier on in the approach, likely served to prime his actions.
To mitigate slips and maintain precision and safety in aircraft operations, it is essential to implement a combination of administrative defences, including adherence to standardized procedures, fatigue management, and crew resource management/threat and error management training. Also needed are physical defences, such as ergonomic design considerations with respect to displays and controls within the flight deck, and prominent sensory feedback (aural and visual indicators).
Findings as to causes and contributing factors
The captain had accrued a significant sleep debt in the week before the occurrence and was operating the aircraft after a nearly 18-hour wake period, at the end of a circadian low. As a result, at the time of the occurrence, the captain’s level of fatigue decreased his attention and vigilance and increased the likelihood of a slip.
Shortly before landing, the captain intended to press the autothrottle disengage switch, but inadvertently pressed the TO/GA switch. This slip likely occurred due in part to the captain’s level of fatigue, and because he was primed to press the TO/GA switch, having mentally rehearsed a go-around earlier in the approach.
2.1.3 Fitness for duty
In a seniority-based bidding system, a reserve schedule is typically held by pilots with lower seniority because being on reserve is considered less desirable for most pilots.
Being on reserve results in a less predictable schedule, with shorter notice of the planned destinations and length of assignment, and this can make it more difficult for crew members to obtain ideal rest that is tailored to the flights they will be conducting. Pilots are responsible to use their time off or designated rest periods to get the necessary amount of rest to ensure that they are prepared for a duty period, particularly when they are on reserve. Additionally, there is subjectivity involved in determining fitness given that the amount of rest needed varies from person to person.
Finding as to risk
If pilots do not monitor their rest to assess if they have accrued a sleep debt, there is an increased risk of fatigue going undetected and unmitigated.
2.2 Aircraft systems
In this occurrence, the inadvertent and undetected autopilot flight director system mode change initiated a complex sequence of events, including an unexpected asymmetric thrust increase, the deactivation of the auto-braking system, and the auto speed brake disengaging after the aircraft landed.
Managing this complexity, especially when the flight crew were primarily focused on maintaining the aircraft's lateral path during landing, became challenging. These issues were exacerbated by the deactivated left thrust reverser. This complexity increased the risk of further confusion, distractions, and errors.
2.2.1 System status and indicators
For instance, disengaging the autopilot triggers an audible tone and flashing status light, whereas disengaging the autothrottle does not trigger an audible tone and is only indicated by a status light, making it easier to miss or overlook.
This variation in annunciating between 2 automatic flight systems can be a source of confusion for flight crews and may lead to a reduction in situational awareness with respect to the status of these systems. Relying on the absence of an indicator to confirm system status can be particularly challenging in a high-workload environment.
In addition, the ability that pilots have to override the autothrottle manually with the forward thrust levers without disengaging the autothrottle is not consistent with the way the autopilot system reacts to similar input, where manually overriding using the control wheel results in an autopilot disengagement.
This inconsistency introduces uncertainty into the behaviour of the system, potentially complicating the intended goal of reducing pilot workload.
In this case, when the TO/GA switch was unintentionally pressed, the autothrottle attempted to increase engine thrust to go-around thrust. The primary visual indications that this had occurred were the letters “TO/GA” displayed on the flight mode annunciator as the autothrottle engaged mode, along with the flight director cues indicating that pitch attitude must be increased to attain the programmed rate of climb for GA mode.
In situations where the flight crew’s attention is directed outside the flight deck, these indicators might not be sufficiently salient, posing a challenge to maintaining awareness of the system’s status and response.
Finding as to causes and contributing factors
The inadvertent TO/GA selection at 70 feet above ground level occurred during a period on the approach when the flight crew’s primary focus was outside of the flight deck. Therefore, with the indications of the TO/GA selection insufficiently salient to alert the crew, the flight mode annunciator and engine thrust display indications for mode change went unnoticed by the flight crew.
2.2.2 Single thrust reverser usage
Following touchdown, the PF released both forward thrust levers to grip and actuate the No. 2 (right) reverse thrust lever. Given that the PF was no longer holding the left forward thrust lever at idle, the autothrottle commanded it to move forward towards go-around thrust.
Although it was reported that pilots are trained to keep part of their hand in contact with the forward thrust levers during all reverse thrust operations, this requires an uncomfortable and awkward hand positioning, and the practice does not appear in Flair’s or Boeing’s documentation.
While there are many opportunities during simulator training for pilots to conduct landings with 1 engine inoperative, leading to the use of a single thrust reverser during landing, there is no related guidance in the Flight Crew Operating Manual , and training does not include operating with 1 reverse thrust lever that is locked in the stowed position.
Finding as to causes and contributing factors
The left reverse thrust lever had been locked in the stowed position per the minimum equipment list . When selecting the right reverse thrust lever following touchdown, the pilot removed his hand from the forward thrust levers, allowing the left one to advance, undetected, as commanded by the autothrottle.
With TO/GA mode selected, many of the conditions that would otherwise cause the autothrottle to disengage automatically were inhibited. There are no autothrottle disengage parameters linked to the use of thrust reversers, in any mode, and as a result it was possible for the autothrottle to command forward thrust while the flight crew was commanding reverse thrust.
Finding as to causes and contributing factors
Although the aircraft was on the ground and the right thrust reverser was deployed, the autothrottle permitted simultaneous operation of reverse thrust on 1 engine and forward thrust on the other. As a result, the autothrottle continued to command the engines towards go-around thrust until it disengaged automatically when the aircraft slowed below 80 knots.
2.2.3 Braking systems
The flight crew had set the autobrake switch to 3 and selected auto speed brakes during the approach per company SOPs, and they were expecting the aircraft to automatically decelerate after landing. However, following touchdown, when the autothrottle advanced the left forward thrust lever, these 2 automatic deceleration systems were disabled.
Finding as to causes and contributing factors
The advancing left forward thrust lever caused the speed brakes, which had briefly deployed, to retract and resulted in the deactivation of the auto-braking system, significantly reducing deceleration during the initial ground roll.
When handling difficulties arose shortly after touchdown because of the asymmetric thrust, the flight crew were occupied with maintaining directional control, and they did not initially realize that the aircraft was not decelerating as expected. By the time maximum manual braking was applied, it was unlikely that the aircraft could have been brought to a stop on the remaining runway available.
Finding as to causes and contributing factors
When the captain applied maximum braking, there was 2500 feet of runway remaining, and the aircraft was travelling at a ground speed of 115 knots with no speed brakes, one engine at near maximum thrust, and the other engine nearing maximum reverse thrust. At this speed and in this configuration, there was insufficient runway remaining to stop the aircraft and it overran the end of the runway.
2.3 Defect control
A defect with the left thrust reverser was first reported in May 2022, more than 6 months before the occurrence. During the intervening months, there were a further 22 reports of a defect with the thrust reverser, each report providing an opportunity to troubleshoot the problem. Despite this, the defect did not meet the regulatory definition of a recurring defect, and as a result, Flair’s maintenance control software did not identify it as such.
A complicating factor is that there were 6 approved maintenance organizations involved in the troubleshooting process, all of which were contracted by Flair to perform maintenance on Flair aircraft. Records show that some of the troubleshooting was duplicated because these AMOs did not have access to the results of previous troubleshooting efforts made by other AMOs.
A simple reset procedure had been used a number of times before the occurrence to clear the fault message and allow the aircraft to continue to be flown, although it was clear that the underlying issue with the system was not being addressed. The initial troubleshooting effort did indicate the likely cause of the issue, but a parts request was not approved for almost 6 months.
Finding as to risk
If the underlying issue behind a persistent maintenance defect is not addressed in a timely manner, there is a risk that it may compound, resulting in a serious consequence.
3.0 Findings
3.1 Findings as to causes and contributing factors
These are conditions, acts or safety deficiencies that were found to have caused or contributed to this occurrence.
- The captain, who was the pilot flying, left the autothrottle engaged after disengaging the autopilot as a result of a habit formed from past flying experience where the practice was permitted.
- The captain had accrued a significant sleep debt in the week before the occurrence and was operating the aircraft after a nearly 18-hour wake period, at the end of a circadian low. As a result, at the time of the occurrence, the captain’s level of fatigue decreased his attention and vigilance and increased the likelihood of a slip.
- Shortly before landing, the captain intended to press the autothrottle disengage switch, but inadvertently pressed the takeoff/go-around switch. This slip likely occurred due in part to the captain’s level of fatigue, and because he was primed to press the takeoff/go-around switch, having mentally rehearsed a go-around earlier in the approach.
- The inadvertent takeoff/go-around selection at 70 feet above ground level occurred during a period on the approach when the flight crew’s primary focus was outside of the flight deck. Therefore, with the indications of the takeoff/go-around selection insufficiently salient to alert the crew, the flight mode annunciator and engine thrust display indications for mode change went unnoticed by the flight crew.
- The left reverse thrust lever had been locked in the stowed position per the minimum equipment list . When selecting the right reverse thrust lever following touchdown, the pilot removed his hand from the forward thrust levers, allowing the left one to advance, undetected, as commanded by the autothrottle.
- Although the aircraft was on the ground and the right thrust reverser was deployed, the autothrottle permitted simultaneous operation of reverse thrust on 1 engine and forward thrust on the other. As a result, the autothrottle continued to command the engines towards go-around thrust until it disengaged automatically when the aircraft slowed below 80 knots.
- The advancing left forward thrust lever caused the speed brakes, which had briefly deployed, to retract and resulted in the deactivation of the auto-braking system, significantly reducing deceleration during the initial ground roll.
When the captain applied maximum braking, there was 2500 feet of runway remaining, and the aircraft was travelling at a ground speed of 115 knots with no speed brakes, one engine at near maximum thrust, and the other engine nearing maximum reverse thrust. At this speed and in this configuration, there was insufficient runway remaining to stop the aircraft and it overran the end of the runway.
3.2 Findings as to risk
These are conditions, unsafe acts or safety deficiencies that were found not to be a factor in this occurrence but could have adverse consequences in future occurrences.
- If pilots do not monitor their rest to assess if they have accrued a sleep debt, there is an increased risk of fatigue going undetected and unmitigated.
3.3 Other findings
These items could enhance safety, resolve an issue of controversy, or provide a data point for future safety studies.
- Flair Airlines Ltd.’s maintenance, repair, and overhaul tracking system was capable of identifying recurring defects as defined by regulations, but its capabilities did not extend to identifying defects such as the left thrust reverser fault in this occurrence, which did not meet the definition of a recurring defect. The defect had been reported 23 times during the 6 months leading up to the occurrence.
4.0 Safety action
4.1 Safety action taken
4.1.1 Flair Airlines Ltd.
Flair Airlines Ltd. adjusted the Standard Callouts subsection in its B737-800 Flight Crew Operating Manual, Volume 1. The “AUTOPILOT DISENGAGED” and “AUTOTHROTTLE DISENGAGED” callouts were replaced with a “MANUAL FLIGHT” callout in order to support the existing procedure, which requires both autopilot and autothrottle to be disengaged at the same time.
This report concludes the Transportation Safety Board of Canada’s investigation into this occurrence. The Board authorized the release of this report on 18 December 2024. It was officially released on 13 February 2025.
Appendices
Appendix A – Work–rest schedule
Date | Duty start | Duty end | Sleep history |
---|---|---|---|
Sunday, 20 November 2022 | No flight duty time. | Slept for about 8 hours. | |
Monday, 21 November 2022 | 1845 | Continued to next day | Slept for about 7 hours, awake for 3 hours, then slept for another 4 hours. |
Tuesday, 22 November 2022 | Continued from previous day | 0654 | Slept 2 split periods of nap (one period of about 2 hours and one period of about 2.5 hours). |
Wednesday, 23 November 2022 | 0045 | 0749 | No sleep reported. |
Thursday, 24 November 2022 | 1850 | Continued to next day | Slept for about 7 hours, awake for 1 hour and then slept again for about 4.5 hours. |
Friday, 25 November 2022 | Continued from previous day | Occurrence time 0625 | N/A |
Date | Time on duty | Time off duty | Sleep history |
---|---|---|---|
Sunday, 20 November 2022 | No flight duty time. | Slept for about 9 hours. | |
Monday, 21 November 2022 | No flight duty time. | Slept for about 9 hours. | |
Tuesday, 22 November 2022 | No flight duty time. | Slept for about 9 hours. | |
Wednesday, 23 November 2022 | No flight duty time. | Slept for about 9 hours. | |
Thursday, 24 November 2022 | 1850 | Continued to next day | Slept for about 11 hours. |
Friday, 25 November 2022 | Continued from previous day | Occurrence time 0625 | N/A |
Appendix B – Definitions of fatigue risk factors
- Acute sleep disruptions — Depending on the stage in which it occurs, sleep disruption may affect physiological functioning and/or cognitive functioning, and elevates the risk of fatigue. The risk increases when the quality or quantity of sleep has been reduced within the previous 3 days.
- Chronic sleep disruptions — Any disruptions to sleep quantity or quality that are sustained for periods longer than 3 consecutive days are considered chronic sleep disruptions. Comparing the amount of sleep obtained to the amount of sleep required for a given period of wakefulness can provide an estimate of a person's sleep debt.
- Continuous or prolonged wakefulness — Being awake for more than 17 hours heightens the risk of fatigue.
- Circadian rhythm effects — Changing sleep-wake patterns too quickly, or working at a time of day at which our body is expecting sleep, can cause circadian rhythms to desynchronize, leading to performance impairments.
- Sleep disorders — Many disorders result in higher than normal levels of fatigue if they are untreated or not managed properly. Three of the more common sleep disorders are insomnia, obstructive sleep apnea, and periodic limb movement disorder.
- Medical, psychological conditions, illnesses or drugs — A person's ability to obtain restorative sleep may be influenced by individual factors, including certain illnesses, the use of drugs or medication that affect sleep or sleepiness, or characteristics such as morningness/eveningness, or one's capacity to nap.
Source: Transportation Safety Board of Canada, Guide to Investigating Sleep-related Fatigue (February 2022).
Appendix C – Left thrust reverser maintenance history
Location | Maintenance activity or event related to left thrust reverser | Rectification | |
---|---|---|---|
09 May 2022 | CYHZ | Left thrust reverser did not deploy on landing. | Reset engine accessory unit (EAU), checked serviceable. |
15 May 2022 | CYWG | Left REVERSER indicator light after landing. | Reset EAU, checked serviceable. |
16 May 2022 | CYYC | Left REVERSER indicator light after landing. | Reset EAU, checked serviceable. |
17 May 2022 | CYYC | Left REVERSER indicator light after landing. | Reset EAU, checked serviceable. |
20 May 2022 | CYKF | Troubleshooting for repeat defect with left thrust reverser. Contracted approved maintenance organization submits parts requisition for an autothrottle switchpack assembly based on Fault Isolation Manual guidance. | No documented reply from Flair maintenance control regarding the part request. NOTE: This part was replaced on 27 November 2022, 2 days after the occurrence. As a result, the ongoing issue with the left thrust reverser was resolved. |
27 May 2022 | CYYZ | Left REVERSER indicator light after landing. | Reset EAU, checked serviceable. |
30 May 2022 | CYUL | Left REVERSER indicator light after landing. | Reset EAU, checked serviceable. |
31 May 2022 | CYYZ | Maintenance inspection of reverse thrust levers and targets, found that they were out of limits. | Minimum equipment list (MEL) applied, left thrust reverser deferred, due date 10 June 2022. |
09 June 2022 | CYKF | Maintenance logbook entry. | MEL extension applied for left thrust reverser, due date 20 June 2022. |
12 June 2022 | CYKF | Contract AMO submits follow-up (second) parts requisition for autothrottle switchpack assembly. | No documented reply from Flair maintenance control regarding the second request for the autothrottle switchpack assembly. |
17 June 2022 | CYHZ | Electrical connectors on the left thrust reverser control module cleaned and reconnected. | Reset EAU, checked serviceable. MEL deferral cleared. |
17 June 2022 | CYHZ | Left REVERSER indicator light after engine start. | Fault could not be cleared. MEL applied, left thrust reverser deferred, due date 27 June 2022. |
19 June 2022 | CYKF | Upper locking actuators replaced on left thrust reverser. | Left thrust reverser checked serviceable. MEL deferral cleared. |
21 June 2022 | CYOW | Left REVERSER indicator light during start. | Thrust reverser control valve connectors cleaned. Reset EAU, checked serviceable. |
22 June 2022 | CYOW | Left REVERSER indicator light after landing. | Reset EAU, checked serviceable. |
30 June 2022 | CYYZ | Left REVERSER indicator light after landing. | Reset EAU, checked serviceable. |
05 July 2022 | CYYZ | Left REVERSER indicator light after landing. | Reset EAU, checked serviceable. |
16 July 2022 | CYQQ | Left REVERSER indicator light after landing. | MEL applied, left thrust reverser deferred, due date 26 July 2022. |
17 July 2022 | CYQQ | N/A | Reset EAU, checked serviceable. MEL deferral cleared. |
25 July 2022 | CYVR | Left REVERSER indicator light after landing. | Reset EAU, checked serviceable. |
04 August 2022 | CYQG | Left thrust reverser failed to deploy during landing roll, left REVERSER indicator light. | Troubleshooting carried out; the only fault found was related to the right thrust reverser. Reset EAU, checked serviceable. |
12 August 2022 | CYVR | Left REVERSER indicator light after landing. | Reset EAU, checked serviceable. |
29 August 2022 | CYUL | Left REVERSER indicator light after landing. | MEL applied, left thrust reverser deferred, due date 06 September 2022. |
02 September 2022 | CYKF | Left thrust reverser control valve electrical connector replaced, left thrust reverser re-activated. | Reset EAU, checked serviceable. MEL deferral cleared. |
12 September 2022 | CYKF | Left REVERSER indicator light after engine start. | Reset EAU, checked serviceable. |
06 October 2022 | CYQG | Left REVERSER indicator light after landing. | Reset EAU, checked serviceable. |
22 October 2022 | CYYZ | Left REVERSER indicator light after landing. | Reset EAU, checked serviceable. |
24 October 2022 | CYQG | Left REVERSER indicator light after landing. | MEL applied, left thrust reverser deferred, due date 04 November 2022. |
25 October 2022 | CYYZ | Left thrust reverser re-activated for troubleshooting. | MEL deferral remains in effect, due date 04 November 2022. |
27 October 2022 | CYXX | During troubleshooting a broken circuit breaker was found, preventing further troubleshooting. New circuit breaker requested. | MEL deferral remains in effect, due date 04 November 2022. |
03 November 2022 | CYKF | Circuit breaker replaced. Troubleshooting indicates that left reverser sync lock needs to be replaced. | MEL deferral remains in effect, due date 04 November 2022. |
04 November 2022 | CYKF | Maintenance logbook entry. | MEL extension applied, due date 14 November 2022. |
04 November 2022 | CYKF | Left thrust reverser sync lock replaced. Left thrust reverser checked serviceable. | MEL deferral cleared. |
08 November 2022 | CYYZ | Left REVERSER indicator light during power up. | Reset EAU, checked serviceable. |
09 November 2022 | CYVR | Left REVERSER indicator light after landing. | Reset EAU, checked serviceable. |
10 November 2022 | CYYZ | Left thrust reverser slow to deploy, left REVERSER indicator light after landing. | MEL applied, left thrust reverser deferred, due date 20 November 2022. |
11 November 2022 | CYYZ | Troubleshooting left thrust reverser issues unsuccessful, further troubleshooting required. | MEL deferral remains in effect, due date 20 November 2022. |
20 November 2022 | CYVR | Maintenance activity. | MEL extension, due date 30 November 2022. |
25 November 2022 | CYKF | Runway overrun. | |
27 November 2022 | CYKF | Autothrottle switchpack replaced. | No further issues with left thrust reverser after aircraft was returned to service. |