Loss of containers overboard and subsequent fire
Container vessel ZIM Kingston
La Perouse Bank, British Columbia
The Transportation Safety Board of Canada (TSB) investigated this occurrence for the purpose of advancing transportation safety. It is not the function of the Board to assign fault or determine civil or criminal liability. This report is not created for use in the context of legal, disciplinary or other proceedings. See Ownership and use of content. Masculine pronouns and position titles may be used to signify all genders to comply with the Canadian Transportation Accident Investigation and Safety Board Act (S.C. 1989, c. 3).
Executive summary
On 21 October 2021, the container vessel ZIM Kingston, with 21 crew members on board, rolled 36° and lost 109 containers overboard while drifting at La Perouse Bank, about 27 nautical miles south of Ucluelet, British Columbia (BC). A number of containers on deck were also damaged.
The investigation determined that the ZIM Kingston experienced parametric rolling. Parametric rolling occurs when sea conditions converge with vessel-specific factors in a precise way, resulting in dangerous rolling motions. The forces created by the vessel’s extreme motions were the precipitating factor for the container loss.
Around 36 hours later, while the vessel was anchored off Victoria, BC, a fire broke out in a damaged container that held dangerous goods (potassium amyl xanthate). The fire then spread to 5 nearby containers, 2 of which also held xanthates and 3 of which held tires and other consumer items. The fire burned for 5 days before it was declared extinguished.
The on-board fire response followed industry and company guidelines and was conducted in an efficient manner. The ZIM Kingston had a contract with a U.S.-based emergency response company, which meant that the vessel had access to specialists who provided guidance throughout the emergency response and a team of trained personnel who were able to board the vessel to help contain the fire. The use of these shore-based specialized personnel, as well as vessels of opportunity, contributed to limiting the extent of the fire.
In November 2021, 4 of the containers lost overboard were recovered from the shores of northern Vancouver Island, along with various debris from the containers. In July 2023, an underwater survey located 29 containers on the ocean floor in proximity to the occurrence site. Ongoing beach cleanups have found debris that is likely from the ZIM Kingston washing up along large stretches of the BC coastline.
In order to better understand the motions that the ZIM Kingston experienced in this occurrence, the TSB contracted the National Research Council Canada to construct a scale model of the vessel. Testing with the scale model was then conducted in a basin where the occurrence conditions were simulated. The testing found that parametric rolling could develop regardless of whether the model was drifting or underway, and that the largest roll motions were observed when the model was in head and following sea conditions. The testing also found that parametric rolling could occur in significant wave heightsSignificant wave height is an average measurement of the largest 33% of waves (Source: National Oceanic and Atmospheric Administration, National Weather Service, “Significant Wave Height,” at https://www.weather.gov/mfl/waves [last accessed 17 July 2024]). as low as 2.6 m.
The investigation identified safety deficiencies that led the Board to issue 2 safety concerns: the first relates to the need for comprehensive guidance for managing the risk of parametric rolling and the second relates to Canada’s preparedness for marine emergencies.
Comprehensive guidance for managing the risk of parametric rolling
Managing the risk of parametric rolling is complex. Not only is it difficult to predict exactly when a parametric rolling event will occur, but once extreme rolling starts, it may not be possible to stop the dangerous motions before negative consequences occur, such as container loss. For this reason, there must be a focus on monitoring for the conditions that give rise to parametric rolling so that preventive measures can be taken when the conditions are present. Doing so requires bridge crew to have formal policies, comprehensive procedures, and effective tools for managing this risk.
The vessel owner had not developed procedures or provided specific tools to support the bridge crew on the ZIM Kingston in making assessments and managing the risk of parametric rolling; as a result, this risk was not being effectively monitored and no mitigation measures were put in place as the vessel held offshore.
The International Maritime Organization (IMO) is generally recognized as the international body best positioned to develop and disseminate guidance to the marine industry; however, its circular addressing the risk of parametric rolling has not been updated in over 17 years. Furthermore, the circular has only minimal operational guidance on parametric rolling and does not offer any guidance with respect to policies, procedures, training, tools, or services related to the management of risk associated with parametric rolling. Lastly, the circular also characterizes parametric rolling as a heavy weather phenomenon, whereas model testing of the ZIM Kingston conducted for the investigation determined that it could occur in moderate sea states.
The IMO recently published its Interim Guidelines on the Second Generation Intact Stability Criteria, which will minimize the risk of parametric rolling and will provide a consistent approach to address risk across the international shipping industry. However, the timeline for incorporation of these guidelines into the International Code on Intact Stability, 2008 is uncertain, and it is not clear whether the guidelines will apply to existing vessels. The guidelines also do not address the training of crew with respect to this issue.
The Board is concerned that the absence of up-to-date comprehensive industry guidance for the management of parametric rolling may cause company policies, procedures, tools, and training to be inconsistent, ineffective, or absent altogether, which could lead to more container loss occurrences, along with their associated negative outcomes for safety and the environment.
Canada’s preparedness for marine emergencies
On commercial vessels, crew are trained and equipped to handle many marine emergencies with on-board resources. However, an emergency can quickly shift to one where outside resources are needed. The occurrence involving the ZIM Kingston demonstrated some of the challenges involved in responding to a marine emergency in Canadian waters. It also raised questions about the availability and capability of Canadian resources to do so.
After the fire broke out on the vessel, it was largely due to fortuitous circumstances that a rapid and effective response using outside resources could be initiated. These same circumstances may not necessarily be present when responding to future occurrences, underscoring the need for a careful look at Canada’s preparedness.
Canada does not require pre-arranged plans for fire response or marine salvage, unlike the U.S. In addition, the Canadian Coast Guard does not directly participate in marine fire suppression activities as part of incident response, nor does it have fire suppression capabilities to directly respond to a vessel fire. While this occurrence took place at sea, previous TSB investigations have shown that there are also issues around preparedness when vessel fires occur in Canadian ports. Outside of ports and harbours, the options for responding to shipboard fires are even more limited should the on-board fire response be unsuccessful in suppressing the fire.
Canada’s preparedness for other types of marine emergencies, such as occurrences involving hazardous and noxious substances (HNS) is also a concern. Canada does not have a plan for how to respond to occurrences involving HNS, although it does have a plan for occurrences involving oil. Recognizing a need for improvement, the federal government has announced that it intends to develop a single system to respond to all marine pollution incidents regardless of their source, with a goal of responding to these incidents in a timely manner that minimizes impact on human health and the environment. In addition, Transport Canada (TC) intends to develop regulations to strengthen preparedness requirements for industry, for example, by requiring vessels to have arrangements for firefighting and salvage services, and by having a response specialist who could work with the federal departments and other partners to manage any incident.
This occurrence, and many others, have shown that while the Canadian Coast Guard has the capacity to evacuate crew members that are injured or at risk, there are systemic gaps in other aspects of responding to emergencies on vessels. While TC is proposing the above-noted changes to address these gaps, in practice the only concrete action that has been taken so far is the 2023 amendment to the Canada Shipping Act, 2001 that gives the Governor in Council the ability to make regulations regarding emergency arrangements. At June 2024, TC indicated that work to develop these regulations is expected to continue over the next 4 years, subject to the government’s regulatory priorities.
In the interim, the Board is concerned that there are gaps in Canada’s preparedness for marine emergencies that exceed the response capacity of a vessel’s crew, posing a risk to vessels, the environment, and the health and safety of the general public.
1.0 Factual information
1.1 Particulars of the vessel
Name of vessel | ZIM Kingston |
---|---|
International Maritime Organization (IMO) number | 9389693 |
Flag | Malta |
Type | Container |
Gross tonnage | 40 030 |
Length overall | 260.05 m |
Design draft | 12.62 m |
Deadweight | 50 782 t |
Built | 2008 by Samsung Heavy Industries Co. Ltd. |
Propulsion | 1 direct-drive diesel engine of 36 560 kW driving 1 fixed-pitch propeller |
Cargo capacity | 4253 twenty-foot equivalent units (TEU) |
Crew complement | 21 |
Charterer | ZIM Integrated Shipping Services Ltd. |
Ship manager / Disponent owner* | Danaos Shipping Co. Ltd. |
Registered owner | Balticsea Marine Inc. |
Classification society / Recognized organization | DNV** |
* A disponent owner is a person or company that has the possession and benefit of the vessel. (Source: Institute of Chartered Shipbrokers (2016), Legal Principles in Shipping Business).
** DNV has undergone 3 name changes since it was established in 1864. Originally known as Det Norske Veritas, it merged with Germanischer-Lloyd in 2013 to become DNV-GL and was renamed DNV in 2021. All references in this report will use the name DNV.
1.2 Description of the vessel
The ZIM Kingston (Figure 1) is a fully cellular container vessel with the accommodation located aft. The accommodation includes the navigational bridge deck and decks A to D. The wheelhouse, located on the navigational bridge deck, is equipped with all navigational equipment required under the International Convention for the Safety of Life at Sea (SOLAS).International Maritime Organization (IMO), International Convention for the Safety of Life at Sea (SOLAS) (1974, last amended 2020), Chapter V, Regulation 19. The vessel was fitted with an analog inclinometerIn June 2023, the IMO amended SOLAS Chapter V, Regulation 19, to include a requirement for the carriage of electronic inclinometers on container vessels and bulk carriers of 3000 GT and up that are built on or after 01 January 2026. and a voyage data recorder.
The vessel has a maximum cargo capacity of 4253 TEU,TEU (twenty-foot equivalent unit) is a measure of container vessel cargo-carrying capacity that uses 20-foot containers as a measure of volume. with 2669 TEU on deck and 1584 TEU in the cargo holds. Container locations are identified using a bay-row-tier system. Bays located forward of the accommodation are numbered 01 to 46 from forward to aft, and bays located aft of the accommodation are numbered 50 to 62 from forward to aft. Rows are numbered from the vessel’s centreline outwards. Tiers above deck are numbered from the deck level upward to the top of the container stack, with tier 82 always being the lowest container in the stack, typically located on the lower hold hatch covers.
At the time of the occurrence, the ZIM Kingston was on a trans-Pacific route, calling at ports in Taiwan, China, and South Korea, as well as on the west coast of Canada and the United States (U.S.). The vessel operated continuously, with bunkering, on-boarding of supplies, and crew changes done during cargo operations.
1.3 Container vessel traffic on Canada’s west coast
Most of the world’s manufactured goods are transported by container vesselsInternational Chamber of Shipping, “Container ships,” at https://www.ics-shipping.org/explaining/ships-ops/container-ships/ (last accessed on 17 July 2024). using 2 sizes of standardized containers: 20-foot or 40-foot equivalent units. These containers can be carried in holds below deck or secured on deck.
Container vessel traffic on Canada’s west coast has been growing at an average of 5% per year for the last decade,Port of Vancouver, “2021 trade through the Port of Vancouver steady despite supply-chain, extreme weather challenges,” at https://www.portvancouver.com/news-and-media/news/2021-trade-through-the-port-of-vancouver-steady-despite-supply-chain-extreme-weather-challenges/ (last accessed 03 July 2024). and is projected to continue rising in the coming years. In 2021, the Port of Vancouver, British Columbia (BC), handled 3.6 million TEUs of containers and received visits from 663 foreign container vessels.Port of Vancouver, “2021 Financial Report,” at https://www.portvancouver.com/wp-content/uploads/2022/05/2021-Financial-Report-English.pdf (last accessed 03 July 2024). The next largest port on Canada’s west coast, the Port of Prince Rupert, BC, handled 1.05 million TEUs of containers in 2021.Port of Prince Rupert, “2021 Annual Report,” at https://2021.rupertport.com/ (last accessed 03 July 2024). With continued growth, west coast terminals are expected to run out of capacity by the mid‑to‑late 2020s.Port of Vancouver, “2021 trade through the Port of Vancouver steady despite supply-chain, extreme weather challenges,” at https://www.portvancouver.com/news-and-media/news/2021-trade-through-the-port-of-vancouver-steady-despite-supply-chain-extreme-weather-challenges/ (last accessed 03 July 2024). This has resulted in planned expansions to the container terminals in both Vancouver and Prince Rupert.
In order to maximize the throughput of containers, operators usually schedule container vessels to arrive almost as soon as the previous one departs. Containers are then loaded or unloaded using port container cranes. If one vessel is delayed, it can cause a cascading effect that requires the following vessels to slow down at sea, maintain a holding pattern outside the port, or anchor as they wait for their turn at the berth.
In the shipping industry, it is common for a vessel’s estimated time of arrival (ETA) to change several times for various reasons including weather conditions, machinery limitations, equipment problems, berthing unavailability, cargo unavailability, and port congestion. When a container vessel arrives at a location earlier than its original ETA or scheduled berthing time, it may proceed to an anchorage and await berthing instructions. If anchorage space is unavailable, the vessel usually maintains a holding pattern offshore.
In the fall of 2021, ports around the world were experiencing significant supply chain congestion resulting from disruptions caused by the COVID-19 pandemic. In the Port of Vancouver, this congestion was exacerbated by wildfires and floods in BC. The congestion forced container vessels to either anchor or maintain holding patterns while waiting for a berth to become available.
1.4 History of the voyage
On 06 October 2021, the ZIM Kingston departed Busan, South Korea, bound for Vancouver. The vessel was loaded with 1965 containers, for a total of 3657 TEUs. Of the 1965 containers, 1273 containers were loaded above deck and 692 containers were loaded below deck. Some of the cargo was classified as dangerous goods (Appendix A), including 4 forty-foot containers that each held 23 800 kg of potassium amyl xanthatePotassium amyl xanthate, shipped as xanthates, is a hygroscopic substance that comes in the form of pellets, flakes, or powder. It is mostly used in mining. When mixed with water or water moisture, xanthates will emit carbon disulfide, which is flammable. The United Nations (UN) number for xanthates is 3342. and 1 twenty-foot container that held 18 000 kg of thiourea dioxide.Thiourea dioxide is a crystalline powder that is used as a bleaching agent for textiles, leather, paper, etc. The UN number for thiourea dioxide is 3341.
ZIM Integrated Shipping Services Ltd. (ZIM), the vessel’s charterer, had an operations department that had initially scheduled the ZIM Kingston to arrive at the pilot boarding station off Victoria, BC, on 19 October to pick up a pilot for berthing at the Port of Vancouver. However, during the voyage, the vessel’s scheduled arrival time at the pilot station was adjusted several times due to changes in berthing space availability, with the final scheduled arrival time at the pilot station being 0200All times are Pacific Daylight Time (Coordinated Universal Time (UTC) minus 7 hours), unless otherwise noted. on 24 October. To try to adjust to the changes, the master reduced the vessel’s speed to its minimum speed while underway. However, even at the minimum speed, the vessel’s ETA on its planned route was approximately 3 days before its scheduled arrival time.
Around 0300 on 21 October, the vessel arrived near La Perouse Bank, approximately 27 nautical miles south of Ucluelet, BC, and outside the Prince Rupert and Victoria Traffic Service zone. The master had been informed that there were no anchorages available, and so he contacted Marine Communication and Traffic Services (MCTS) in Prince Rupert and stated that the vessel would be drifting at La Perouse Bank. The waves and winds at this time were from the south. The forecast weather for the next 24 hours was 35- to 42-knot winds from the southeast with a swell height of about 5 m.
The master positioned the vessel with the bow oriented southwesterly into the waves, stopped the main engine,The ZIM Kingston’s propulsion system is direct drive and the main engine cannot run without propelling the vessel. and allowed the vessel to begin drifting northward. Once the ZIM Kingston had drifted northward for around 4 hours, the master used the engine to return the vessel to its original position. On the first drift, the master assessed the vessel’s performance by observing its drifting speed and any rolling and pitching. The vessel’s drifting speed was about 3 knots, and rolling did not exceed 10°.
There were a number of container vessels in proximity to the ZIM Kingston on October 21 while it was drifting.These vessels included the MV ZOI, with a length overall of 275 m; the YM Triumph, with a length overall of 333 m; the YM Upward, with a length overall of 334 m; the Seaspan Ganges, with a length overall of 336 m; and the APL Qingdao, with a length overall of 349 m. Some of these vessels were also drifting, while some were underway in holding patterns. The master was aware that these vessels were also holding offshore and he observed them as part of his assessment.
From 0300 to 1800, the ZIM Kingston drifted northward and returned to its original position twice. During this time, the winds ranged from 34 to 40 knots, and the wave heights from 5 to 6 m. At 1707, an anchorage became available and the master was informed. By this time, however, the vessel had nearly completed 2 drifts and its drifting performance was better than expected, which informed the master’s decision to keep drifting rather than go to anchorage.
At 1800, the vessel began drifting northward for the 3rd time with the bow oriented southwesterly into the waves. The master was still on the bridge but was resting, and the third officer was the officer of the watch. At around 2229, the winds were southeasterly at 42 knots and the waves were 5 to 6 m from the southwest. The bow was oriented west-southwesterly into the waves, and the vessel was drifting northward at 2.2 knots. At this time, the vessel experienced heavy rolling and pitching that lasted for about 1.5 minutes. The vessel rolled heavily to both port and starboard approximately 4 times, with the maximum roll being 36°. The vessel was in position 48°28.21' N, 125°39.67' W at the time of the heavy rolling (Figure 2) and the crew noted that some containers had been lost.
After the heavy rolling, the master immediately stationed himself near the steering controls and directed the third officer to start the main engine. The main engine was on 10 minutes’ notice for routine operations, but it was also on bridge control at the time of the occurrence, which meant that the engine room had made arrangements so that it could be started immediately from the bridge in the event of an emergency. After a call with the duty engineer, the third officer started the main engine from the bridge and made a few course adjustments that were ordered by the master.
From the bridge, it was apparent that the lost containers had fallen from bay 34. At around 2235, the master notified MCTS Prince Rupert that the vessel had lost containers. At 2238, the master made a security broadcast by VHF (very high frequency radiotelephone) to inform nearby vessels about the occurrence and to notify them of the potential hazard posed by containers that had gone overboard and were floating in the vicinity. The Canadian Coast Guard (CCG) subsequently issued a navigational warning for floating containers around the area of the occurrence.
At 2251, the master contacted Danaos Shipping Co. Ltd. (Danaos), the ZIM Kingston’s ship manager, and reported that the vessel had experienced parametric rolling (see Section 1.13 for details) and had lost some of its containers. At 2256, the master contacted ZIM and reported the same information. Following the master’s call, Danaos notified Resolve Marine, a company that was under contract to Danaos to assist in salvage and emergency situations,Resolve Marine is a U.S.-based company, with offices and resources around the world, that provides marine emergency response services, salvage and wreck removal, and maritime training. Resolve Marine was under contract to Danaos to provide 24-hour emergency firefighting and salvage assistance for Danaos vessels located anywhere in the United States. of the incident. Danaos then contacted a local salvage company for assistance with cleanup of any containers and associated debris that might wash up on shore.
At 2321, the master informed MCTS Prince Rupert that the vessel had also lost containers from bay 54. He indicated that there were collapsed containers on deck and that parts of the destroyed containers were hanging over the side of the vessel at about 5 m above the surface of the water. He also mentioned that the port-side accommodation ladder was damaged. The master indicated that, owing to the heavy weather, it was too dangerous to send crew outside to check the exact number of lost containers. He visually estimated that about 20 containers from bays 34 and 54 had been lost. MCTS asked the master to check the manifest and find out what was in the containers to see if there was any dangerous cargo.
At 2340, the master made a request to MCTS Prince Rupert for an anchorage. MCTS contacted the Pacific Pilotage Authority (PPA) dispatch, which asked MCTS to have the vessel proceed to the Constance Bank anchorage. On 22 October at 0018, after receiving confirmation from MCTS Prince Rupert, the vessel proceeded to Constance Bank anchorage.
At 0159, the master notified MCTS Prince Rupert that containers had also been lost from bay 14, and that these containers possibly held dangerous cargo. The master indicated that he and the crew would verify which containers had been lost from bay 14 when the vessel was at the anchorage. Once it was daylight, as the vessel was proceeding to the anchorage, the crew began assessing the severity of the damage and compiling a list of lost and damaged containers. At this point, the chief officer confirmed that some of the containers that had gone overboard from bay 14 held dangerous goods and that some of the damaged containers still on board in this bay held dangerous goods, specifically potassium amyl xanthate.
Around 0930, after the crew had assessed the lost and damaged containers, the chief officer reported to the master that some containers in bays 14, 34, and 54 were lost or damaged. The chief officer identified that there were still 17 containers in bay 14 and that 10 of them were damaged, including three 40-foot containers holding potassium amyl xanthate. In addition, of the containers that had gone overboard, 2 held dangerous goods, with 1 container holding potassium amyl xanthate and the other container holding thiourea dioxide.
From 1130 to 1300, several of the containers lost overboard were sighted during flyovers by fixed-wing aircraft from the Transport Canada (TC) National Aerial Surveillance Program. At 1200, the vessel anchored at Constance Bank, 4 nautical miles south of Victoria. The crew continued assessing the severity of the damage to the containers and the vessel, and the bridge officers began carrying out an anchor watch.
1.4.1 Subsequent fire in containers on board
On 23 October, at approximately 1046, the master noticed smoke coming from the forward deck while he was in his cabin. He proceeded to the bridge and asked the third officer, who was the officer on watch, about the smoke. The third officer had been completing paperwork and was not aware of the smoke. The third officer asked one of the crew members to investigate the source of the smoke. At this time, the vessel was still anchored at Constance Bank.
Shortly after, the crew member sent to investigate the smoke reported that there was a fire in a collapsed container in bay 14 that held dangerous goods. The third officer relayed this information to the master. At 1053, the fire alarm was activated and, shortly after, the master ordered the crew to start the fire pump. Around 1056, all of the crew members had mustered at the muster station. The master consulted the International Maritime Dangerous Goods Code (IMDG Code) fire schedule to determine the method for fighting a fire involving potassium amyl xanthate. The fire schedule recommended creating water spray from a protected position.International Maritime Dangerous Goods (IMDG) Code, adopted by IMO resolution A.716 (17) in 2002, entered into force on 01 January 2004.
At 1057, the second officer contacted MCTS Victoria and stated that there was a fire in a dangerous goods container, that firefighting was being initiated, and that the fire was not contained. The Canadian Coast Guard Ship (CCGS) Cape Calvert was deployed to the vessel. By 1058, 2 crew members who were on the fire team donned firefighting outfits and self-contained breathing apparatuses and initiated boundary cooling using fire hoses. Other team members also began boundary cooling using fire hoses.
Around 1108, the second officer provided an update to MCTS Victoria, indicating that there was a lot of smoke but no open fire. About 3 minutes later, the second officer provided another update indicating that the fire had spread to a 2nd dangerous goods container, that there were now visible flames, and that the team was trying to extinguish the fire.
At 1138, the CCGS Cape Calvert arrived on scene and stood by to evacuate personnel if required. The CCGS Captain Goddard M.S.M. also arrived on scene and stood by. At 1145, Danaos contacted the ZIM Kingston and the master confirmed that there was a fire on board.
At 1229, the CCGS Cape Calvert reported to the ZIM Kingston’s bridge that the fire was increasing. Around 1230, Danaos contacted Resolve Marine to request assistance with responding to the fire on the vessel. At 1236, the second officer contacted MCTS and requested assistance to extinguish the fire. At 1239, Joint Rescue Coordination Centre (JRCC) Victoria tasked Canadian Forces Auxiliary Vessel (CFAV) Firebrand, a fireboat based at Canadian Forces Base Esquimalt.The CFAV Firebrand’s main fire pump has a flow rate of 675 m³/h and a throw height of about 101 m.
At 1255, JRCC Victoria informed the master that smoke produced by burning xanthates is highly toxic and flammable. An emergency zone was established around the vessel, and all other vessels were cleared from Constance Bank. Around 1300, a senior salvage master from Resolve Marine contacted the master to do a remote assessment of the situation, then continued to provide remote assistance to the master while a firefighting response team mobilized to Seattle, Washington, U.S., with its firefighting equipment. At around 1322, the master notified the CCG that the intensity of the fire was increasing.
Because of the toxic flammable gas created by the fire, there were discussions between JRCC and other authorities about the crew stopping the firefighting and abandoning the vessel. The master was notified of these discussions and, at around 1400, he asked the crew to prepare for the possibility of abandoning ship. Around 1430, the crew rigged some of the fire hoses to the vessel railing so that the hoses would continue to spray water in the direction of the fire while unattended. At 1449, the second officer reported to CCG that fire had spread and there were then about 6 containers on fire.
At 1500, the CCG regional operations centre held a coordination call with federal, First Nations, provincial, and municipal representatives, as well as the ship owner’s agent and legal representatives. At this time, an incident command post (ICP) was established.An incident command system (ICS) is a standardized site incident management system for emergencies, disasters, or non-emergency events. The ICS allows response organizations to have a formalized structure for command, control, and coordination of the response through an incident command post (ICP). An ICS is recognized worldwide as a scalable system that provides a common response framework for an event of any size.
Meanwhile, the ZIM Kingston’s crew members rigged up emergency towing pennant wires at the forward and aft ends of the vessel to enable emergency towing without the assistance of on-board personnel should it become necessary to move the vessel after abandoning it. Around 1530, the crew finished rigging the fire hoses so that they could be left unattended, and the master ordered the crew to return to the accommodation and stand by. At 1535, the CFAV Firebrand arrived on scene and stood by.
At around 1618, the master reported to the CCG that the fire had spread to the inner rows of containers, which the crew could not access. At 1658, the CCG recommended that the crew abandon ship because of the toxic smoke. Resolve Marine recommended that the vessel evacuate non-essential crew and retain a small volunteer crew to keep the vessel operating and maintain the response to the fire.
At some point after 1600, Health Emergency BC, given information from the ICP, reported that there was no current or significant risk to public health or safety because of the vessel’s distance from shore and the fact that any air- or water-based pollution would dissipate. To assist with air quality monitoring, Resolve Marine contracted and mobilized an environmental air quality monitoring company to Victoria.
At 1706, the CCGS Cape Calvert evacuated 10 crew members, transported them to Victoria, and returned to the ZIM Kingston. At 1834, the Cape Calvert evacuated another 6 crew members and transported them to Victoria. Five crew members—the master, chief officer, second officer, chief engineer, and third engineer—remained on board the ZIM Kingston to continue firefighting.
At 1955, the Vancouver-based tug Seaspan Raven, which had been contracted by Resolve Marine, arrived on site to stand by for emergency towing services. The crew on the Seaspan Raven began boundary cooling with the ZIM Kingston master’s and crew members’ coordination. The Seaspan Raven has a firefighting class 1 system.Firefighting class 1 systems have, at a minimum, a flow rate of 2400 m³/h, a throw length of 120 m, and height of 45 m.
Resolve Marine also contracted 2 privately owned vessels, the Maersk Trader and Maersk Tender, that happened to be berthed in Victoria at the time. Both are foreign-flagged offshore supply vessels with firefighting class 1 systems. They arrived at the occurrence site at around 0100 on 24 October and joined the Seaspan Raven in the boundary cooling operations (Figure 3).
Overnight, the wind speeds started increasing, and by 0540, they were 30 to 35 knots and were hampering firefighting efforts. At 0630, the Atlantic Raven, a CCG-contracted emergency towing vessel, arrived on scene and stood by. By 1132, the winds had increased to 48 knots.
Around 1205, the Maersk Tender proceeded to Port Angeles, Washington, to pick up Resolve Marine personnel and equipment. Around 2050, 4 of the Resolve Marine team members had been transported to Victoria, but because of bad weather, they were unable to board the ZIM Kingston.
On 25 October, at 1533, 5 Resolve Marine team members boarded the vessel to assess the fire. At 1735, 7 of the 16 crew members who had been evacuated from the ZIM Kingston returned to the vessel to assist with firefighting efforts.
On 26 October, at 0750, the Resolve Marine team commenced targeted firefighting on 3 containers that did not contain dangerous goods. This involved using a drill to cut a hole in the side of the containers, then inserting a lance with a hose attachment into the hole and flooding the containers with water.
The Resolve Marine team continued firefighting, boundary cooling, and monitoring the containers over the course of the next 2 days, with continued assistance from the 3 contracted tugs. A fire round conducted at 0040 on 27 October noted no fire or smoke. Cooling and monitoring continued up until 1545 on October 28, at which point the Resolve Marine team declared the fire extinguished.
1.5 Container loss monitoring and cleanup efforts
A total of 109 shipping containers were lost overboard when the ZIM Kingston rolled heavily. This represented approximately 11% of the vessel’s deck cargo. The majority of the containers that went overboard likely sank shortly after entering the water. Those that remained afloat began to drift northwest, parallel to the Vancouver Island coastline. High winds and seas prevented recovery efforts from being initiated immediately after the container loss.
TC, the CCG, and the U.S. Coast Guard used various resources to track the containers that remained afloat. Overhead flights were carried out when the weather permitted, and tracking buoys were deployed to mark the location and potential drifting patterns of the floating containers. On 27 October, overflights identified 4 containers that had gone aground on the beaches of Cape Scott Provincial Park and Raft Cove Provincial Park on northern Vancouver Island (figures 4, 5, 6, and 7).
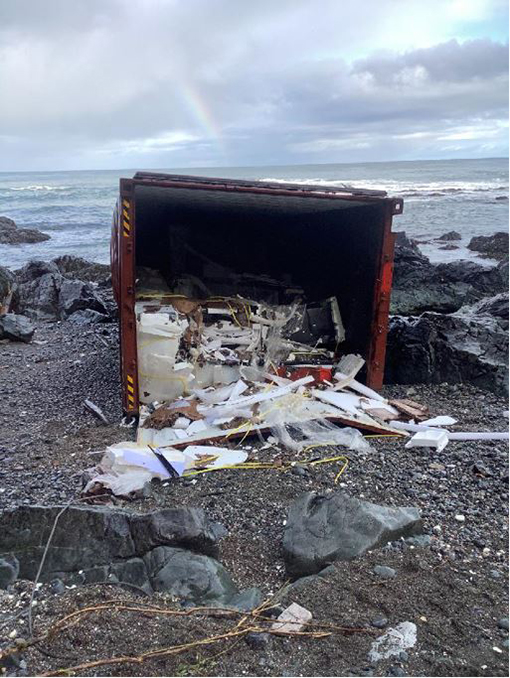
The ICP mobilized environmental personnel, who began to assess the toxicological risk posed by the container contents and to evaluate ecological sensitivities for any impacted shoreline habitats.
By 30 October, Danaos had hired a local contractor to recover the containers and remove the associated debris. At the request of the ICP’s environmental unit,The ICP environmental unit included Environment and Climate Change Canada (ECCC), the CCG, the Province of BC, the Department of Fisheries and Oceans Science Sector, First Nations representatives, and Danaos. a debris removal plan was developed to guide the cleanup operations of the grounded containers and their contents. The plan provided guidance for site assessments and initial cleanup efforts of existing containers and debris. It also set out guidance for short-term monitoring, which involved surveys to identify the presence of containers and debris, and long-term monitoring, which involved periodically checking sites that had been cleaned up over a 9-month period to determine if they remained free of containers and debris. The plan also provided guidance for containers and debris found and reported in the future.
By the end of November, cleanup efforts had removed the 4 containers. Because of the remoteness of the locations, the containers had to be cut up so that they could be airlifted off the beach in pieces. Associated debris was also removed, including refrigerators, polystyrene foam, Christmas decorations, sofas, industrial parts, and other household items.The total recorded weight recovered was 47.7 tonnes, which included the 4 containers as well as waterlogged debris. Following the initial cleanup efforts, debris continued to wash up on shore. The local contractor continued to work on removing the containers and debris.
On 07 February 2022 the CCG negotiated an agreement with Danaos to designate a representative for the vessel. This ensured that the CCG had a ZIM Kingston representative in Canada in the event the CCG identified new hazards relating to the containers and debris in the future.
On 13 April 2022, a Danaos-contracted company conducted a bathymetric survey of an approximate 2 square kilometre area around the location where the containers were lost overboard. The water depth in the area surveyed was approximately 100 m. The survey identified 17 objects of interest on the sea floor, but the sonar equipment being used could not conclusively identify the objects as containers. The original data from the survey to validate the conclusions were not provided to the participants of the ICP.
See section 1.26.1 for additional information about cleanup operations following this occurrence.
1.6 Injuries
Danaos sent all of the ZIM Kingston crew for preventative medical examinations after the occurrence. The chief officer was treated in hospital for smoke inhalation.
1.7 Damage
As a result of the occurrence, a total of 109 containers went overboard from 3 bays (bays 14, 34, and 54) and 53 containers on deck were damaged (figures 9 and 10). Post-occurrence examination of the containers showed that there had been fires inside 6 of the containers in bay 14: of these, 3 had held xanthates and 3 had held tires and general consumer goods. One of the hatch covers in bay 14 was bent, and the port-side accommodation ladder was also damaged.
Bay 14 held a combination of 40-foot containers and 20-foot containers on deck. The 20-foot containers were stowed in pairs end-to-end, forming the equivalent length of the 40-foot containers. Forty-nine containers were lost overboard from bay 14, and 17 were damaged (Figure 10).
Bay 34 held only 40-foot containers on deck. Thirty-one containers were lost overboard from bay 34, and 17 were damaged (Figure 11).
Bay 54 held only 40-foot containers on deck. Twenty-nine containers were lost overboard from bay 54, and 20 were damaged (Figure 12).
1.8 Pollution
Of the 109 containers lost overboard, 105 had not been recovered at January 2024. Two of the containers held dangerous goods, and the rest held a variety of consumer items. Of the 2 lost containers that held dangerous goods, 1 container held potassium amyl xanthate and the other held thiourea dioxide.
During the fire, the burning potassium amyl xanthate on the vessel generated toxic smoke. Air quality monitoring ashore from various locations in Victoria, was conducted to assess the risk to public health. Health Emergency BC determined that the level of contaminants in the air was low enough that there was no risk to public health.
1.9 Vessel ownership and management
The ZIM Kingston’s registered owner is Balticsea Marine Inc. (Balticsea). The owner had a bareboat charter“In a bareboat charter, an owner leases their commercial vessel to someone else. The charterer (the person leasing the vessel) is responsible for providing a crew and the provisions.” (Source: Transport Canada, “Request or extend a certificate of bareboat registry,” at https://tc.canada.ca/en/marine-transportation/vessel-licensing-registration/request-extend-certificate-bareboat-registry [last accessed on 10 July 2024]) agreement with Danaos, which then acted as a disponent owner for all regulatory and contractual purposes. Danaos was responsible for the general management of the vessel, including crewing, maintenance, and regulatory compliance.
The ZIM Kingston had been under a time charter to the container line ZIM since 2008. Under this arrangement, ZIM was responsible for the commercial operations of the vessel, including scheduling port calls, booking cargo and bunkers, and arranging berths. ZIM was also responsible for fuel costs, pilotage fees, and harbour dues.
ZIM’s time charter with the ZIM Kingston was formalized through a contract known as a charter party. A charter party is a standard contract between a vessel owner or disponent owner and a charterer that sets out the responsibilities of both in regard to chartering of the vessel. In this case, the charter party referred to ZIM as the charterer and Balticsea as the owner. In practice, however, Danaos, as disponent owner, was fulfilling the responsibilities assigned to Balticsea.
For time charters, the charter party normally sets out the agreed period of hiring, the terms and conditions of voyages, the type of cargo to be carried, etc. The charter party may also set out other standard contractual terms such as its service speed, fuel consumption, and carrying capacity. A charter party may also include various contractual clauses, such as an option to request the replacement of the vessel’s master or officers if the charterer is dissatisfied with their conduct. This option is a standard contractual clause that can be found in most charter parties and was included in ZIM’s time charter.Charter party between Balticsea Marine Inc. and ZIM Israel Integrated Shipping Services (08 June 2006), section 13(g).
ZIM had also developed sailing instructions for the masters on ZIM-chartered vessels. With respect to decisions regarding voyage planning and passage distances, the sailing instructions indicated that
Master’s on scene decisions with respect to ship’s safety is always respected. However, use of phrase “safety of the vessel” shall be based on common sense, good seamanship and with due regard to prevailing circumstances.
Lack of confidence and/or reluctance in executing duties as per Charterer’s requirements shall not be justified by aforementioned expression and will be challenged by Charterer with no delays.
If there are clear grounds to believe that regular route […] became unsafe for surface navigation or there are other reasons to deviate from planned passage, Master has to inform Charterer and provide relevant information that supports his decision […]
Any deviations from the most effective […] route for getting “GSM [Global System for Mobile communication], Wi-Fi, TV and/or similar signals” are not allowed.
By capitalizing more time when planning ship’s route, we have a good chance to save a significant amount of Bunker per round trip.ZIM Global Operations, General Sailing Instructions for ZIM/GSL Operated Vessels (June 2021), section 2.4.
With respect to fuel consumption, the charterer’s instructions indicated that
Global warming issues are relevant to both our planet and living environment. Fuel oil savings reduce CO2 emission to keep the earth breathing. In view of the great proportion of fuel costs, [the] [m]aster’s task is to economize on fuel consumption whenever possible. Masters of all ZIM/GSL [Global Ship Lease] operated vessels are required to constantly check their ship’s fuel consumption.Ibid., section 3.1.
1.9.1 Weather routing and voyage planning service
ZIM had a contract with Weathernews Inc. (WNI), a company that provides weather routing and voyage planning advice for vessels on cross-ocean passages. WNI collects weather data, creates forecasts using an artificial intelligence weather forecasting system, analyzes risks and develops and proposes solutions, and communicates about identified risks.
For the ZIM Kingston, WNI was under contract to provide the following:
- Voyage planning material that generally consisted of a recommended route, along with a rationale and advice for that route; a waypoint overview for the recommended route; alternative routes; pressure surface maps; graphs of vessel speed; forecast wind wave height; and a table of forecast sea conditions along the route
- A 24-hour communication service via email or phone for voyage-related inquiries (estimated time of arrival, vessel speed, meteorological phenomena, etc.)
WNI sent regular recommendations to ZIM vessels for voyage planning based on the vessels’ loaded condition, main engine capabilities, sea state, and forecast weather conditions.
With respect to routing, ZIM’s sailing instructions indicated that masters were requested to cooperate with WNI and follow its recommendations. The master had the ultimate authority over route selection and could elect to follow a different route or request an alternative route from WNI, and WNI would continue to provide support, guidance, and weather updates.
If masters decided not to follow WNI recommendations, the charterer’s instructions indicated that masters were required to provide to ZIM and WNI a detailed statement to explain the decision based on their expertise and good seamanship with reference to factors such as the weather, sea state, safety parameters, and the vessel’s condition.Ibid., section 2.5. This provision is a standard clause that is common throughout the global shipping industry.
1.10 Personnel certification and experience
The crew on the ZIM Kingston held certificates in accordance with the provisions of the International Convention on Standards of Training, Certification and Watchkeeping for Seafarers (the STCW Convention).
The master of the ZIM Kingston held a Class 1 certificate of competency issued by the Hellenic Republic Ministry of Shipping on 06 January 2015. The master had been employed with Danaos since 2004 and had worked as a master since 2019. The master joined the ZIM Kingston on 08 May 2021.
The chief officer held a chief mate on a seagoing vessel of 500 GT or more certificate of competency issued by the Government of the Russian Federation on 16 March 2019. He had worked at sea since 2004 and had served on several vessels owned or operated by Danaos since 2010. In 2019, he started serving as chief officer, and he joined the ZIM Kingston as chief officer on 08 May 2021.
The second officer held a chief mate on a seagoing vessel of 500 GT or more certificate of competency issued by the Government of Ukraine on 22 March 2016. He had completed 2 contracts with Danaos in the last 2 years and joined the ZIM Kingston as second officer on 08 May 2021.
The third officer held an officer in charge of a navigational watch certificate of competency issued by the Government of Ukraine on 04 September 2017. This was his first contract with Danaos, and he joined the ZIM Kingston as third officer on 08 May 2021.
1.11 Safety management system
Safety management involves individuals at all levels of an organization and requires that a systematic approach be taken in identifying and mitigating operational risks. A safety management system (SMS) is an internationally recognized framework that allows companies to identify hazards, manage risks, and make operations safer. The principal objective of an SMS on board a vessel is to ensure safety at sea, prevent human injury or loss of life, and avoid damage to property and the environment.
Some elements of an effective SMS are
- procedures for identifying hazards and managing risks;
- procedures and checklists for the vessel’s operations;
- maintenance procedures for the vessel and its associated equipment;
- documentation and record-keeping procedures;
- procedures to prepare for and respond to emergency situations; and
- drills, training, and familiarization for the vessel’s crew.
As required by the International Management Code for the Safe Operation of Ships and for Pollution Prevention (the ISM Code), Danaos had an SMS in place for its vessels, including the ZIM Kingston. To demonstrate its compliance with the ISM Code, the ZIM Kingston held a safety management certificate that had been issued by the classification society DNV on 16 April 2019. The SMS documentation consisted of 4 manuals: a policy manual, a procedures manual, a fleet instructions manual, and an emergency procedures manual. Copies of each manual were available on board the ZIM Kingston at the time of the occurrence.
1.11.1 Safety culture
One way to encourage a good safety culture is through the implementation of formal safety management processes. Safety culture is the way that safety is perceived, valued, prioritized, and managed throughout all levels of a company. It encompasses the attitudes, beliefs, perceptions, and values of all employees in an organization in relation to safety. One of the most important factors affecting safety culture is management’s degree of commitment to safety. It is vital that owners and operators actively demonstrate their commitment by providing leadership and resources to manage safety. For example, management should support employees in ensuring safe operations and reporting safety-related issues and provide documented procedures.
1.12 Arranging anchorages for container vessels calling at Vancouver
There are 3 primary anchorage locations that can accommodate container vessels the length of the ZIM Kingston while awaiting a berth in Vancouver: English Bay, Vancouver Inner Harbour, and Constance Bank. For Constance Bank anchorages, vessels are assured of a place for only 48 hours, after which time they may need to vacate the anchorage for other vessels. There are also anchorages at Trincomali Channel, Plumper Sound, and Cowichan Bay, known as overflow anchorages,The overflow anchorages are typically used by container vessels when there is no space available at the primary anchorages. The primary anchorages are closer to key stops on the routes of most container vessels (the Port of Vancouver and the pilot station off Victoria) than the overflow anchorages. that can accommodate container vessels the length of the ZIM Kingston.
The Constance Bank anchorages are managed and allocated by the Pacific Pilotage Authority (PPA), which takes anchorage requests over the telephone. The English Bay anchorages, Vancouver Inner Harbour anchorages, and overflow anchorages are managed and allocated by the Vancouver Fraser Port Authority (VFPA). The VFPA has an online portal through which requests for anchorage must be submitted. A request through the portal prompts the VFPA to begin actioning the request; this may include assigning an anchorage or waitlisting a vessel and sending updates when an anchorage becomes available. Ships’ agents sometimes informally contact the VFPA by phone or email to get information about anchorage availability. These calls or emails do not constitute an anchorage request; the only way to initiate an anchorage request to the VFPA is through the VFPA portal.
ZIM has a local agent in Vancouver who is the point of contact for masters on ZIM vessels arriving at the Port of Vancouver. One of the jobs of the local agent is to arrange anchorages for ZIM vessels if requested by the masters. On 19 October 2021 at 1539, the local agent asked the master of the ZIM Kingston if he would like to have an anchorage secured for the vessel, and the master replied that he would.
After making telephone enquiries with the VFPA and the PPA, the local agent informed the master that all of the VFPA and PPA anchorages were full. He also noted that he had arranged a PPA anchorage for the vessel as of 22 October at 1700, which was the earliest available time. He also indicated that he would contact the master if anything came available sooner.
On 19 October at 1737, the master of the ZIM Kingston emailed the local agent to ask about stopping and drifting near the entrance of Juan de Fuca Strait. The master also repeated his request for an anchorage and added the operations superintendent in ZIM’s Pacific Operations office to the email. The master and the ZIM operations superintendent then discussed options for stopping and drifting; however, it was concluded that this was not feasible owing to bad weather.
At 2300, the operations superintendent emailed the master and indicated that WNI had been asked to provide a routing plan that allowed for the vessel to arrive at the Victoria pilot station at 0200 on 24 October. The operations superintendent also indicated that the MV ZOI, which was ahead of the ZIM Kingston in the berthing schedule, was in the same situation and was currently drifting outside the port limits in Juan de Fuca Strait. At 2347, the master emailed the operations superintendent and stated that at the position of the MV ZOI, the significant wave heightsSignificant wave height is an average measurement of the largest 33% of waves (Source: National Oceanic and Atmospheric Administration, National Weather Service, “Significant Wave Height,” at https://www.weather.gov/mfl/waves [last accessed 17 July 2024]). would be from 4.5 to 5.5 m with the maximum up to 9 m per WNI calculations. The master received no response to this email.
On 20 October at 0212, the master emailed the operations superintendent and stated that he would drift outside Juan de Fuca Strait. At 1115, WNI provided the vessel with a data sheet that indicated predicted weather information for the period during which the vessel would be drifting. The local agent contacted the PPA in the morning and afternoon of 20 October to see if any anchorages had come available, but there were none.
On 21 October at 0300, the vessel arrived at La Perouse Bank. At this time, there were still no PPA anchorages available for a vessel of the ZIM Kingston’s length. However, there were VFPA anchorages available for a vessel of the ZIM Kingston’s length. VFPA records indicate that no requests for anchorage were made through its portal on behalf of the ZIM Kingston for the occurrence voyage.
Rather than going to an anchorage, container vessels sometimes opt to hold offshore. The reasons for doing so vary. For example, container vessels may hold offshore if there are no anchorages available, if they encounter scheduling changes, or if doing so economizes on fuel costs or fees associated with pilotage and anchoring.
There are certain areas where container vessels typically maintain holding patterns while awaiting a berth at the Port of Vancouver, one being at La Perouse Bank and another being inside the Juan de Fuca Strait, in an area colloquially known as “the Racetrack.” At the time of the occurrence, there were 12 vessels maintaining a holding pattern in “the Racetrack” and there were a number of other vessels, along with the ZIM Kingston, maintaining a holding pattern at La Perouse Bank. The waters inside Juan de Fuca Strait are partially protected from ocean swell, while those at La Perouse Bank are not.
1.13 Parametric rolling
Parametric rolling results from the interaction of 2 elements—the wave characteristics in a seaway and the stability characteristics of a vessel—and leads to the sudden onset of extreme roll angles for a vessel. The problem of parametric rolling of vessels has been recognized for more than half a century.International Towing Tank Conference, Recommended Procedures and Guidelines, Predicting the Occurrence and Magnitude of Parametric Rolling (effective 2006), at https://ittc.info/media/1920/75-02-07-043.pdf (last accessed 17 July 2024).
This section describes
- parametric rolling in general,
- the simulations run by the National Research Council Canada (NRC) with a scale model of the ZIM Kingston,
- the guidance and tools available to assess the risks of parametric rolling, and
- the results of a desktop exercise in which the forecast data and actual occurrence data were used to determine whether the available guidance and tools identified a risk of parametric rolling for the circumstances of the occurrence.
1.13.1 General
The stability of a vessel with a given load is determined by its centre of gravity (G) and its underwater hull formUnderwater hull form refers to the shape of those parts of vessel’s hull that are submerged under water. with volume, centre of buoyancy (B), waterplane area,Waterplane area refers to the shape of the vessel’s hull on the waterline, as seen from directly above or below. and metacentre (M).When a vessel floating in still water is inclined by an external force to a small angle, the centre of buoyancy shifts to a new position. The point where the new line of buoyancy (a vertical line that passes by the centre of buoyancy) intersects with the original line of buoyancy marks the initial metacentre. For small angles of heel, stability can be measured by the metacentric height (GM) (Figure 13). The vessel also has a natural period of roll, which is a measure of the time it takes for the vessel to make a complete roll from one side to the other and back again (i.e., from starboard extreme to port extreme and back to starboard extreme). Vessels with a larger GM have a shorter roll period (a quicker return to upright) and are considered more stable than those with a lower GM.
Once a vessel is underway, its stability parameters will change as it encounters waves.The wave encounter period is the time that passes, usually measured in seconds, while a vessel encounters 2 adjacent wave crests or 2 adjacent wave troughs. When the vessel is in, or close to being in, head or following seas, and the length of the waves is similar to the length of the vessel, a situation arises where the vessel begins to fluctuate between minimum stability and maximum stability. Minimum stability occurs when the vessel is centred on a wave crest, where waterplane area is minimized. Maximum stability occurs when the vessel is centred in the trough, where waterplane area is maximized.
When the vessel is on a wave crest, stability is reduced and the vessel will roll over to one side, but when the wave trough reaches midship, the increased stability quickly pushes the vessel to an upright position. Once another wave crest reaches the midship position, stability is again reduced, which results in the vessel rolling in the opposite direction, but when the wave trough reaches midship, it will quickly push the vessel back upright again. This sequence is illustrated in Figure 14.
This fluctuation in stability is accentuated in vessels with a flared bow and flat transom stern, characteristics that are common for container vessels because they maximize deck cargo carrying capacity while minimizing water resistance through the use of fine hull lines. The fluctuation in stability is also accentuated when the vessel is travelling in waves high enough to cause a significant change in underwater hull form.
The timing of the waves is also an important factor in the development of parametric rolling. For a simplified analogy, consider pushing someone on a swing. For the swing to go higher, the push must be applied at just the right moment as the swing starts its forward motion after having reached its maximum. The effect is even greater if 2 well-timed pushes are applied, one at each end.
Although there are many more factors involved, a similar idea applies to a vessel that is rolling under the forcing action of the waves. If the force exerted by a wave acts at just the right moment in the vessel’s roll period, then the roll will be amplified. If the vessel encounters 2 waves during a single roll period that act at just the right moments, the roll angle of the vessel can be amplified to extreme levels. If there happens to be a sequence of several such waves, a parametric roll will develop and the roll angle of the vessel can increase dramatically.This analogy is from the DNV booklet entitled “Parametric rolling – a concern for container ships?” Paper Series 2005-P011 (April 2005).
Once parametric roll resonance develops, the vessel’s roll angle will increase until the vessel’s dampening forcesDampening forces can be created by structures on or in the vessel, such as fins, bilge keels, or anti-rolling tanks. The natural resistance a vessel encounters as it moves through the water is also a dampening force. are large enough to absorb the vessel’s rolling energy or there is a change in the vessel’s encounters with the waves, either due to a change in the waves themselves or a change in the vessel’s speed or heading. Parametric roll resonance may occur quickly, in only a few cycles, and last a relatively short time. Nevertheless, in even a short time, it can cause major damage to a vessel and its cargo.
1.13.2 ZIM Kingston model testing
In order to better understand the motions that the ZIM Kingston experienced in this occurrence, the TSB contracted the NRC to conduct model testing at its Ocean, Coastal and River Engineering Research facility in St. John’s, Newfoundland and Labrador. The test program involved the construction of a 1:50 scale model of the ZIM Kingston, loaded to represent the vessel’s displacement, centre of gravity, GM, and roll period at the time of the occurrence (Figure 15).
The model was built with steering capability and was self-propelled so that testing could be done in drifting, transiting, and manoeuvring operational modes. The model was also fitted with accelerometers. The testing took place in the Ocean Engineering Basin, which is 75 m long, 32 m wide, and 3.2 m deep, and had segmented wave generators along 2 of its sides to create waves (Figure 16). Wind was modelled using a fan bank stationed on one side of the basin.
The basin and model used an optical motion tracking system to record the model’s motions. The data recorded in the model testing were then scaled up to understand the motions experienced by the ZIM Kingston and the wave phenomena that can create these motions.
1.13.2.1 Environmental modelling
The weather buoy that was nearest to the location of the occurrence was the La Perouse Bank weather buoy, approximately 60 km away. On the day of the occurrence, the buoy measured significant wave heights (Hs) that ranged from 4.6 to 6.4 m and wave periods (Tp) from 10.5 to 13.5 seconds.
NRC analyzed the data from the La Perouse Bank weather buoy to determine how the bathymetry of the ocean floor would have affected waves at the location of the occurrence. As a result of this analysis, the following wave parameters were used for the testing:
- 5.6 m Hs and 13.5 s Tp
- 5.3 m Hs and 11.6 s Tp
- 4.6 m Hs and 9.0 s Tp
1.13.2.2 Testing
The testing was segmented based on the vessel’s 3 operational modes around the time of the occurrence: drifting, transiting, and manoeuvring. In each of these operational modes, the vessel was tested at relative headings to the waves of 0°, 45°, 90°, 135°, and 180°. This was done to facilitate understanding of the vessel’s motions in head through to following seas.
The following testing was undertaken for each operational mode:
- Drifting: 60 tests were undertaken. During these tests, the vessel was initially held steady and then released to drift freely in the wind and waves.
- Transiting: 64 tests were undertaken. During these tests, the model’s propulsion and steering were used to maintain a course in the waves generated by the basin.
- Manoeuvring: 39 tests were undertaken. During these tests, the model’s propulsion and steering were used to transit at an initial heading and then complete a U-turn before transiting again.
Of these tests, a total of 114 were successful. An unsuccessful test consisted of a test where the model came too close to the edge of the basin.
1.13.2.3 Results
Out of the 114 successful tests, 38 (37%) resulted in the model developing roll motions greater than 20°. The maximum roll motions recorded were 48°. In all of the operational modes, the largest roll motions were observed when the model was in head and following sea conditions (Figure 17). No significant roll motions were observed in beam sea conditions.
Analysis of the tests that resulted in roll motions greater than 20° showed that the model’s pitching periodPitching refers to the rotational motion of a vessel around its transversal axis, making the bow and stern alternatively rise and fall as the vessel moves through waves. The pitching period is the amount of time, usually measured in seconds, that it takes for one complete oscillation (e.g., for the bow to move from its highest point to its lowest and back to its highest again). was approximately equal to the wave encounter period and was nearly half the roll period. The ratio of roll period to wave encounter period is a key factor for the development of parametric roll resonance and indicates that parametric rolling was the cause of the extreme rolling events during the testing. Furthermore, the testing determined the range of values for this ratio, as well as for the ratio of wave length to ship length, that were found to coincide with parametric rolling of the vessel (Table 2).
Parameter | Typical | ZIM Kingston model testing |
---|---|---|
Roll period / wave encounter period (TN/TE) | TN/TE ≈ 2 | 1.95 < TN/TE < 2.9 |
Wave length / ship length (LE/LBP) | LE/LBP ≈ 1 | 0.95 < LE/LBP < 1.5 |
Finding: Other
Model testing by the NRC identified that parametric rolling can occur in significant wave heights as low as 2.6 m, far less than those encountered at the time of the occurrence.
The tests conducted with the model drifting in a near head seas scenario most closely resembled the condition of the ZIM Kingston at the time of the occurrence. Tests in these conditions were repeated multiple times and showed that extreme motions, such as those experienced on the ZIM Kingston, could be reproduced when the significant wave height was 5.6 m and the wave period was 13.5 s. These tests showed multiple roll angles up to 35°, with the motions taking different amounts of time to initiate, ranging from 2 minutes to 12.5 minutes.
The model testing also determined vertical and transversal accelerations acting on the bays where container losses occurred, as well as adjacent bays, for the highest and furthest outboard containers. The highest accelerations were transversal in bay 14 at near 0.95 g;The term g refers to the acceleration of a free-falling body due to gravity and is constant at 9.808 m/s2. The acceleration of an object in motion (such as a container on the deck of a vessel) is proportional to the force acting on it. however, the transversal accelerations in the other bays examined (bays 10, 30, 34, 54, and 58) were all near 0.9 g.
Typically, large vessels are structurally flexible, and hogging and saggingHogging and sagging refer to the tendency of a vessel’s hull to flex as it passes through a wave crest and trough, respectively. events contribute considerably to the accelerations encountered by locations far away from the centre of gravity due to resonant and transient vibrations, phenomena known as springing and whipping. The model testing did not account for such structural issues. Testing also indicated that, in cases where the model rolled by 25.5° or more, it would have been possible for sea water to impact the sides of the containers on deck, known as a “green water” event (Figure 18). These events can impose significant loads on the container structures.
Throughout the testing, it was also observed that both regular and irregular waves could cause parametric roll resonance. It was also observed that the time it took for parametric roll resonance to develop varied based on the model’s speed, with resonance taking longer to develop at lower speeds, such as while drifting. During the manoeuvring tests where parametric rolling occurred, it was also observed that roll amplitudes reduced once the model began to turn, confirming that changing a vessel’s heading can minimize rolling once it has started.
1.13.3 Guidance and tools for assessing the risk of parametric rolling
The following sections describe the guidance and tools that were provided to the crew on the ZIM Kingston, as well as that generally available to bridge teams on container vessels, to manage the risk of parametric rolling.
1.13.3.1 Guidance and tools available to the crew on the ZIM Kingston
Danaos’ fleet instructions manual, which was part of its SMS, contained some guidance on parametric rolling. The manual defined it as a phenomenon of large, unstable rolling that occurs suddenly in head or stern quartering seas. The manual indicated that this type of rolling is violent in nature and results in very large accelerations that compromise the safety of container vessels. Parametric rolling was further defined as a threshold phenomenon, meaning that it occurs when certain environmental, operational, and design parameters exist.
The manual went on to list parameters that contribute to parametric rolling, as follows:
- The ship would be traveling with a small heading angle to the predominant wave direction (head or stern quartering sea).
- Wavelength of the predominant swell would be comparable to ship’s length.
- Wave height would be fairly large.
- The ship’s roll-dampening characteristic would be low.Danaos Shipping Co. Ltd, Fleet Instructions Manual, Revision 55 (01 September 2021), Chapter 6, section 1.6.7.
The manual cautioned that if resonance occurred between the wave encounter period and the natural, or twice the natural, roll period of the vessel, then parametric rolling could be experienced.
The manual also referred to a booklet produced by DNV entitled “Parametric Rolling – A Concern for Container Ships?”. A copy of this booklet was available on the vessel’s bridge. It provided a description of the theory behind the development of parametric rolling. The conditions for its development were given as follows:
- The natural period of roll is equal to approximately twice the wave encounter period
- The wave length is on the order of the ship length (between 0.8 and 2 times LBP [the length between perpendiculars])
- The wave height exceeds a critical level
- The roll damping is lowDNV, “Parametric rolling – a concern for container ships?” Paper Series 2005-P011 (April 2005), section 3.1.
With respect to the wave heights required to instigate parametric rolling, the DNV booklet stated that, for big vessels, the waves would need to be rather large, which occurs seldomly, and gave an example from a DNV internal report of a 230 m long vessel that would require waves with a significant height of between 7 and 8 m to cause parametric rolling. The booklet advised that heading changes in the order of 30° would be required to reduce rolling motion.
The master on the ZIM Kingston had some general knowledge of the risk posed by parametric rolling, but had never experienced it, nor had he ever completed a quantitative assessment of risk specific to parametric rolling.
1.13.3.2 International Maritime Organization
The International Maritime Organization (IMO) has developed several documents that are relevant to the management of risk related to parametric rolling, as described below.
1.13.3.2.1 Guidance to the master for avoiding dangerous situations in following and quartering seas
In May 1995, the IMO Maritime Safety Committee (MSC) published a circular entitled, “Guidance to the Master for Avoiding Dangerous Situations in Following and Quartering Seas.” Parametric rolling motion was one of the issues addressed in the circular, among others.International Maritime Organization, MSC/Circ. 707, Guidance to the Master for Avoiding Dangerous Situations in Following and Quartering Seas (19 October 1995).
In January 2007, the MSC published a revised circular entitled, “Revised Guidance to the Master for Avoiding Dangerous Situations in Adverse Weather and Sea Conditions.” The introduction warned that “some combinations of wave length and wave height under certain operation conditions may lead to dangerous situations for ships….”International Maritime Organization, MSC.1/Circ. 1228, Revised Guidance to the Master for Avoiding Dangerous Situations in Adverse Weather and Sea Conditions (11 January 2007). and that “when sailing in adverse weather conditions, a ship is likely to encounter various kinds of dangerous phenomena, which may lead to capsizing or severe roll motions causing damage to cargo, equipment and persons on board.”Ibid.
The circular advised crew to regularly observe the wave conditions, particularly wave period and length, gave some explanations for how to do this, and also explained how to determine the wave encounter period, either by calculation or by using a chart provided. The circular cautioned that the guidance contained within it was designed to accommodate all types of merchant ships and, therefore, being of a general nature, might be too restrictive for some vessels and too generous for others.
The circular described parametric rolling as the result of stability variation between a vessel’s position on the wave crest and its position in the wave trough and described 2 situations where parametric rolling may occur, as well as how to recognize it:
- The wave encounter period is approximately equal to the roll period of the vessel, a situation characterized by asymmetric rolling, i.e., the roll amplitude to one side is much greater than the amplitude to the other.
- The wave encounter period is approximately equal to half the roll period of the vessel, a situation characterized by symmetric rolling with large amplitudes. In this situation, parametric rolling may occur in following, quartering, head, and bow seas.
The circular pointed out that severe parametric roll motions could be induced by small waves in head or bow seas because heavy heaving or pitching motions may contribute to the stability variations, especially in vessels with a bow flare and flared stern frame.
The circular also provided some guidance for avoiding dangerous situations, including 2 different approaches for parametric rolling. Firstly, section 4.2.2.1 of the circular, which concerned successive high-wave attack, advised that when transiting in following or quartering seas with an average wave length that is larger than 0.8 times the vessel length and a significant wave height that is larger than 0.04 times the vessel length, the vessel speed should be reduced or the course changed if the vessel is operating in the danger zone indicated in Figure 19.
Secondly, section 4.2.3.2 advised that for avoiding parametric rolling in following, quartering, head, bow, or beam seas, the course and speed of the vessel should be selected so as to avoid situations where the wave encounter period is close to the vessel’s roll period or close to one half of the vessel’s roll period.
1.13.3.2.2 Interim Guidelines on the Second Generation Intact Stability Criteria
In December 2020, the MSC published a circular entitled, Interim Guidelines on the Second Generation Intact Stability Criteria.International Maritime Organization, MSC.1/Circ. 1627, Interim Guidelines on the Second Generation Intact Stability Criteria (10 December 2020). The preamble to these guidelines pointed out that some vessels are at greater risk of encountering critical stability in waves, and indicated that administrations may, for certain vessels or groups of vessels, apply dynamic stability criteria to assess the safety level of the vessel in waves. To this end, the guidelines provided performance-based criteria for assessing 5 dynamic stability failure modes in waves. One of the dynamic stability failure modes was parametric rolling.
The criteria provided a method to assess the likelihood of stability failure, defined as “an event that includes the occurrence of very large roll (heel, list) angles or excessive rigid body accelerations, which may result in capsizing or impairs normal operation of the ship and could be dangerous to crew, passengers, cargo, or ship equipment.”Ibid.
Compliance with the criteria was to be assessed in stages. First, the vessel design (for a given loaded condition, operational profile, and wave environment) would be assessed for vulnerability to each of the dynamic stability failure modes. If the vessel was found to not be vulnerable to any of the 5 failure modes, the assessment for the vessel would be concluded and the vessel would be exempted from further requirements in this regard. On the other hand, if the vessel was found to be vulnerable to 1 or more of the failure modes, there were 3 options:
- Changes could be made to the vessel’s design, loaded condition, or operational profile. The vessel’s vulnerability would then be reassessed until it was found to be not vulnerable, with any pertinent operational limitations in place.
- The vessel could be advanced to a direct stability assessment, involving numerical and/or physical modelling of the vessel and its behaviour in a sea state. Similar to option 1, the stability assessment would be repeated until a combination of design, loaded condition, and operational profile was found that resulted in the vessel not being vulnerable, with any pertinent operational limitations in place.
- Operational guidance could be developed and implemented, adherence to which would result in the vessel being not vulnerable.
The desired level of safety could be achieved by virtue of the vessel’s design alone, by the implementation of operational measures alone, or by some combination of the two. The guidelines described the procedures to be followed when developing operational measures, which could include:
- limitations related to areas of operation, or routes and season
- limitations related to maximum significant wave height
- guidance on the combinations of vessel speed and relative heading that should be avoided for each relevant sea state
The IMO envisions incorporating the second generation intact stability criteria into the International Code on Intact Stability, 2008 and making them mandatory; however, the criteria must be tested beforehand. For this reason, the guidelines are currently available on a trial basis and the IMO has invited stakeholders to provide feedback on them. The IMO has not established a timeline for implementing the guidelines as mandatory, and it is not clear whether the guidelines are intended to apply only to new builds, or whether they will also apply to existing vessels.
1.13.3.2.3 Proposal for a new output on prevention of loss of containers at sea
At its 107th session in June 2023, the MSC considered a proposal for “a new output addressing the continued loss of containers at sea by means of joint and coordinated measures to prevent these losses throughout the work of the involved Committees and Subcommittees”.International Maritime Organization, MSC 107/17/12, Proposal for a new output on prevention of loss of containers at sea (28 February 2023). The proposal noted that member states and non-governmental organizations are currently working on several related initiatives, including ones aimed at assessing
- the true strength limits for lashing and container gear,
- possible gaps in planning and loading procedures,
- extreme motion and acceleration values due to the vessel size, and
- stability issues during parametric roll in following seas.
The proposal asserted that work on preventing container loss at sea needs a coordinated approach that allows for individual initiatives to benefit from and build on one another.
As a result of deliberations on the proposal, a new output, “Development of measures to prevent the loss of containers at sea,” was added to the agenda for the Subcommittee on Carriage of Cargoes and Containers. This subcommittee will coordinate work on the new output with other applicable IMO subcommittees, with a target completion year of 2025.
1.13.3.2.4 Seafarers’ Training, Certification and Watchkeeping Code
The Seafarers’ Training, Certification and Watchkeeping (STCW) Code sets out basic requirements for training and certification of seafarers at an international level. The STCW curriculum for certification of officers on container vessels does not include training on parametric rolling.
1.13.3.3 Classification societies
Some classification societies, including the American Bureau of Shipping (ABS), Bureau Veritas (BV), and DNV, have introduced optional class notationsClass notations are marked on a vessel’s classification certificate to signify that the vessel meets specific classification society standards. This includes hull construction and class survey during construction (A1 notation, often accompanied by a Maltese Cross) or for special features beyond those typically covered by general construction standards, including noise levels, cybersecurity, and energy efficiency. to indicate that a vessel’s performance with respect to parametric rolling has been evaluated and that information has been provided for the crew to identify and mitigate the risk of parametric rolling.
ABS and BV both have similar requirements for assigning a notation.American Bureau of Shipping, “Guide for the Assessment of Parametric Roll Resonance in the Design of Container Carriers,” (Aug 2024), at https://ww2.eagle.org/content/dam/eagle/rules-and-guides/current/design_and_analysis/133-guide-for-the-assessment-of-parametric-roll-resonance-in-the-design-of-container-carriers-2024/133-parametric-roll-guide-aug24.pdf (last accessed 18 July 2024).,Bureau Veritas, “Parametric Roll Assessment Rule Note NR 667” (July 2019), at https://erules.veristar.com/dy/data/bv/pdf/667-NR_2019-07.pdf (last accessed 16 July 2024). They require numerical simulations to be performed for the vessel’s motions in a range of sea states and relative headings for representative vessel loading conditions and service speeds in order to determine the vessel’s maximum roll angle for each scenario. Input required for the simulations includes the details of the vessel hull form, results from model tests (relevant to the hull’s dampening characteristics) and details of the vessel loading conditions and operating speeds, among other things. The process must take into account the dampening benefits of roll stabilization devices such as anti-roll tanks. The results of the simulations are then used to develop operational guidance for the master, in the form of polar diagrams (wave heading angle vs. speed for each sea state and loading condition), indicating the risk level(s) associated with parametric rolling. An example from ABS is shown in Figure 20.
There are 2 options for achieving the class notation with DNV: vessels can either install anti-rolling tanks or implement software that meets functional, technical, and performance requirements for calculating risk.Det Norske Veritas, “New DNV anti-roll app helps avoid container loss” (31 May 2022), at https://www.dnv.com/expert-story/maritime-impact/New-DNV-anti-roll-app-helps-avoid-container-loss.html (last accessed 17 July 2024). DNV has also developed an app called Anti-Roll Assist, which can be used on board a vessel or from a shore-based control centre and which provides information to masters to help them recognize and avoid the risks of parametric and synchronous rolling.
The app uses data from hydrodynamic simulations of the individual vessel’s hull form (conducted in advance) as well as data such as the vessel’s draft, trim, metacentric height, heading, and speed; water depth; and online wave data. The app generates a polar diagram that depicts the heading and speed of the vessel and the strain on its container securing system (Figure 21). An integrated reporting feature documents the reasons for decisions made regarding deviations from the predetermined route.
At the time of the app’s release in 2022, DNV reported that work was underway to create interfaces that would enable the app to be integrated with other bridge software systems.
1.13.3.4 Other industry guidance and tools
In May 2021, a project known as the TopTier Joint Industry Project was initiated by Maritime Research Institute Netherlands. It brought together various container transport industry experts to identify and recommend improvements for transporting, stowing, and securing containers and related matters, and to provide the technical understanding needed for safe designs and innovations in the future.Maritime Research Institute Netherlands, “TopTier Securing Container Safety,” at https://www.marin.nl/en/jips/toptier (last accessed 16 July 2024). A review of current practice and incidents was conducted in Phase 1 of the project, which showed that parametric rolling in following seas was especially hazardous. In early 2022, several tools were produced to alert mariners to the issue:
- A notice that includes a flow chart with steps to follow and quantitative criteria to apply to identify if a risk of parametric rolling exists, and describes what actions to take if it does (Appendix B)
- A suite of videos that visually presents the information contained in the Notice to Mariners
- A roll risk estimator that consisted of a spreadsheet for calculating the risk of parametric rolling and a polar diagram to visually display the results (Appendix C)
These toolsThese tools are available at https://www.marin.nl/en/jips/toptier (last accessed 16 July 2024). assume that data on the wave characteristics will be gathered by visual observation, and instructive notes are provided for this.
In September 2022, the Danish company Kjærulf Pedersen developed a sensor system that can recognize the tendencies that lead to parametric rolling and send a message to the vessel’s control system so the system and crew have time to change course.The Maritime Executive, “Sensor company builds system to warn of parametric rolling danger” (05 September 2022), at https://maritime-executive.com/article/sensor-company-builds-system-to-warn-of-parametric-rolling-danger (last accessed 16 July 2024). The company’s system is based on 3 sensors, placed at the bow, midship, and stern, that monitor the vessel’s movements in real time. The system compares the input from the sensors with data on the vessel’s speed, acceleration, and direction to detect if the vessel’s movements are approaching a state that can become uncontrollable. If so, a warning is sent to the vessel’s control system so that mitigating action can be taken. The system had been successfully installed and tested on 4 Maersk container vessels.
Global technology company ABB has developed the OCTOPUS Advisory Suite,ABB, “Octopus – On-board, Part of ABB’s Advisory Systems,” at https://library.e.abb.com/public/3298fbfa811896fbc1257b4e00449f1e/OCTOPUS%20product%20sheet%20v.3.pdf (last accessed 16 July 2024) which provides continuous monitoring, simulation, and forecasting of a vessel’s responses and performance. The system gathers information about the vessel, the route, the loading conditions, vessel-specific limitations, and the weather to offer a user interface that advises on safe speeds, headings, and operating windows, as well as avoidance of the dangers of rolling, slamming, and parametric rolling.
DTN, a company that operates in several sectors, including the marine and offshore sectors, has developed a Ship Performance Optimization System (SPOS). This system offers a seakeeping moduleDTN, “SPOS,” at https://www.dtn.com/weather/shipping/spos/ (last accessed 16 July 2024). that can define motion threshold values in relation to IMO parameters for parametric roll, synchronous roll, broaching, and high wave resonances. SPOS Seakeeping calculates motions to ensure that the vessel’s intended route will avoid areas exceeding limits. SPOS Seakeeping shows the forecast motion values in chart form, and shows motions that will likely exceed limits in both chart and polar diagrams (Figure 22).
In 2020, the Swedish Club, a multinational mutual marine insurance company, published a report entitled “Container focus: Preventing the loss of containers at sea.”The Swedish Club, “Container losses: The Swedish Club identifies the catalysts” (29 September 2020), at https://www.swedishclub.com/news/press-releases/container-losses-the-swedish-club-identifies-the-catalysts (last accessed 16 July 2024). The report explores planning, loading, stability, and lashings. It also provides advice on dealing with heavy weather and includes some explanation and guidance about parametric rolling. Although the report emphasizes the importance of using judgement to make course and speed adjustments when heavy weather is encountered, it does advise that the best defences against parametric rolling are equipment that can help detect it and training to help crew to recognize and avoid it.
In the aftermath of a major occurrence in 1998 involving the parametric rolling of the container vessel APL China in head seas and the IMO activities that followed, ship design and engineering company Herbert Engineering Corp. produced a training video to help crew to understand and avoid all forms of large rolling motion, including parametric rolling in head seas. The video explores the reasons why large rolling can occur in particular conditions and suggests what can be done to limit it.The training video is available at https://youtu.be/QEw6fKZTpzc (last accessed 16 July 2024).
The Nautical InstituteThe Nautical Institute is a non-governmental organization that aims to promote professionalism, best practices, and safety throughout the maritime industry and to represent the interests of its members. (Source: The Nautical Institute, “About us,” at https://www.nautinst.org/about-us.html (last accessed 16 July 2024) has an online technical library that includes a slide presentation entitled “Introduction to Parametric Rolling Motion.”The Nautical Institute, “Introduction to Parametric Rolling Motion (PRM),” at https://www.nautinst.org/uploads/assets/e05c5a46-9efd-49d3-839fddc8a7f85941/Introduction-to-Parametric-Rolling-Motion-ver-A4-presentation.pdf (last accessed 16 July 2024). The presentation provides some theory and description of parametric rolling, and introduces the case study of an occurrence in 2014 involving the loss of containers from the Svendborg Maersk. For detecting the factors that induce parametric rolling, the presentation points to the guidance provided in the IMO’s 2007 circular. The presentation also offers several recommendations for addressing the general risk of parametric rolling on board vessels, as follows:
- include parametric rolling on the list of recommended STCW simulation training
- create vessel-specific guidelines using direct stability assessments
- integrate sea state monitoring into on-board systems to assist mariners with identifying sea states that induce parametric rolling
- include sea state monitoring systems in SOLAS’s mandatory equipment
Finally, weather routing service providers are in a good position to provide guidance and advisory services to assist vessels in forecasting the risk of parametric rolling, given that they have access to vessel particulars, route, and sea state forecasts. Following an occurrence in January 2021 involving the loss of containers from the Maersk Essen, the Danish Maritime Accident Investigation Board identified that the vessel’s weather service company, WNI—the same company that was under contract to ZIM—had a software solution capable of motion risk forecasting that could assess the risk of parametric rolling. WNI’s software is based entirely on IMO’s 2007 circular and assessed the risk of parametric rolling during the Maersk Essen’s voyage as being high.Danish Maritime Accident Investigation Board, “Maersk Essen: Marine Accident Report on Loss of Cargo, 16 January 2021,” at https://dmaib.com/media/8489/maersk-essen-loss-of-cargo-on-16-january-2021.pdf (last accessed 16 July 2024).
1.13.4 Post-occurrence assessments of risk for parametric rolling
To enhance its understanding of the numerous factors involved and to evaluate the effectiveness of various guidance materials relating to the identification of risk for parametric rolling, the TSB conducted a risk assessment exercise using the circumstances of the ZIM Kingston’s occurrence voyage as the basis.
Three sources were suitable for use in the desktop exercise:
- the materials available on board the vessel (the fleet instructions manual and the DNV booklet);
- the IMO circular (MSC.1/Cir.1228); and
- the TopTier Joint Industry Project outputs (Notice to Mariners and Risk Estimator)
A variety of scenarios were established—combinations of different vessel speeds, headings, and wave conditions—reflecting the circumstances as they were planned or forecast in the days leading up to the occurrence, as well as the actual conditions at the time of the occurrence. These scenarios were then run through the methodologies described in each set of guidance materials to determine whether the risk of parametric rolling could be identified.
1.13.4.1 Parameters of scenarios used to assess the risk of parametric rolling
At 1115 on 20 October, WNI issued a voyage data sheet to the vessel for a route entitled “Drifting Plan” (Appendix D). The data sheet provided a summary of weather and sea state conditions (strong or near gales, gusting to gale force, and up to around 6 m waves) forecast for a position outside Juan de Fuca Strait from approximately 0330 on 21 October until 1830 on 23 October. During this time period, the vessel was assumed to be stationary, i.e., with no change in position and a speed over ground of 0. More detailed weather and sea state forecasts, including significant wave height and wave period, were also provided for 12‑hour intervals, starting from 1700 on 20 October.
Accordingly, for the risk assessments using the forecast data in the drifting plan (scenarios 1 through 4 in Table 3), the vessel was assumed to have a speed over ground of 0 and to be headed into the wind. Wave conditions were taken from the WNI forecast.
For the 2nd set of risk assessments, actual conditions from the time of the occurrence were assumed (scenarios 5 through 7 in Table 3) as follows: the vessel was headed approximately into the waves (which were coming from the west-southwest) and was drifting astern, in the same direction as the waves were travelling. The vessel’s speed over ground was 2.7 knots and its heading was 244°.The speed over ground and heading used for the actual occurrence data scenarios are representative values from the range of data provided by the vessel’s automatic identification system (AIS). The range of wave conditions determined for the vessel model tests were also used (see section 1.13.2.1).
Data source | Scenario number | Date and time | Vessel speed (knots) | Vessel heading (degrees) | Wave conditions | ||
---|---|---|---|---|---|---|---|
Direction (degrees) | Significant height (metres) | Period (seconds) | |||||
Forecast data provided in the drifting plan | 1 | 21 October at 0500 | 0 | 112.5 | 202.5 | 3.1 | 9 |
2 | 21 October at 1700 | 0 | 157.5 | 202.5 | 4.8 | 11 | |
3 | 22 October at 0500 | 0 | 180 | 225 | 5.3 | 11 | |
4 | 22 October at 1700 | 0 | 180 | 247.5 | 5.5 | 13 | |
Occurrence data | 5 | 21 October at 2230 | 2.7 | 244 | 225 | 5.6 | 13.5 |
6 | 21 October at 2230 | 2.7 | 244 | 225 | 5.3 | 11.6 | |
7 | 21 October at 2230 | 2.7 | 244 | 225 | 4.6 | 9.0 |
1.13.4.2 Results of risk assessments
The above parameters were evaluated and results applied to the criteria in accordance with the various source materials, with the TSB’s results shown in Table 4 below.
Scenario | Date/ time | Guidance on board | MSC.1/Circ.1228 | TopTier | |||
---|---|---|---|---|---|---|---|
Fleet instructions manual | DNV booklet | Sec. 4.2.2.1 | Sec. 4.2.3.2 | Notice to Mariners | Risk estimator | ||
1 – Drifting plan | 21 Oct at 0500 | No | No | No | No | No | No |
2 – Drifting plan | 21 Oct at 1700 | No | No | No | No | No | Yes |
3 – Drifting plan | 22 Oct at 0500 | No | No | No | No | No | Yes |
4 – Drifting plan | 22 Oct at 1700 | No | No | No | No | No | No |
5 – Occurrence | 21 Oct at 2230 | No | No | No | No | Yes | No |
6 – Occurrence | 21 Oct at 2230 | No | No | No | Yes | Yes | Yes |
7 – Occurrence | 21 Oct at 2230 | No | No | No | No | No | Yes |
1.13.4.2.1 Documentation available on board during the occurrence voyage
When only the guidance material available on board during the occurrence voyage was considered, the risk of the vessel developing parametric rolling was not identifiable for any of the scenarios. The main reason for this was that the fleet instructions manual did not identify the wave encounter period being approximately half the vessel roll period as a precursor for parametric rolling.
As well, some of the other criteria were ambiguous and therefore made the assessment dependent on an individual’s interpretation; for example, the criteria in the fleet instructions manual that wave height should be “fairly large.” The DNV booklet specified that waves with a significant wave height of greater than about 4% of the vessel length (or, in this case, 10.4 m) were necessary for the development of parametric rolling. However, waves of this height were not observed in this occurrence.
1.13.4.2.2 International Maritime Organization circular
With respect to the 2007 IMO circular, if section 4.2.2.1 (concerning risk of successive high-wave attack) was considered alone, a risk was not identifiable mainly because the wave heights at the time of the occurrence were not predicted to be in excess of the criteria defining large waves (that is, wave heights greater than 4% of vessel length). If section 4.2.3.2 (concerning avoiding parametric rolling in following, quartering, head, bow or beam seas) was considered, the risk was identifiable for the vessel in one scenario likely experienced around the time of the occurrence. There are very few criteria specified in section 4.2.3.2 to help identify risk, with the guidance only that the vessel will have a wave encounter period of close to or approximately half the vessel roll period. Determining whether these conditions are present depends significantly on the judgement of the user. Specifically, one must decide the tolerance that is acceptable: is the risk present if the wave encounter period is half the roll period plus or minus 1 second, or more? The circular offers no guidance on this question.
1.13.4.2.3 TopTier Notice to Mariners and risk estimator
When using the TopTier Notice to Mariners, a risk of parametric rolling was apparent for 2 of the 3 scenarios likely experienced by the vessel around the time of the occurrence (scenarios 5 and 6 in Table 4). The tolerance allowed when evaluating the wave encounter period is plus or minus 3 seconds. However, the Notice to Mariners was not effective when applied to the forecast scenarios from the drifting plan, since the method described in the Notice to Mariners applies only to vessels operating in following seas.
When using the TopTier risk estimator spreadsheet, a risk of parametric rolling was identified for 2 of the forecast scenarios in the drifting plan as well as 2 of the scenarios likely around the time of the occurrence (scenarios 2, 3, 6, and 7 in Table 4). One reason that the results from the Notice to Mariners differ from the results from the risk estimator is that the risk estimator accounts for the risk of parametric rolling in near head seas as well as in following seas, whereas the Notice to Mariners only accounts for the risk in following seas.
1.14 Design, construction, and maintenance of containers
The design, construction, and maintenance of containers used to transport goods are regulated by the International Convention for Safe Containers, 1972. The Convention requires container design to be approved and certified by a government party to the Convention; in practice, this approval process is often delegated to recognized organizations.A recognized organization is a classification society that has been delegated authority through formal legal agreements with the federal Minister of Transport to perform inspections or issue certificates on behalf of the Minister. The Convention also places the responsibility for maintenance on the owner of the container and requires owners to examine containers at intervals appropriate to operational conditions. Containers are also required to be inspected and re-certified 5 years after construction, and at intervals not exceeding 30 months afterwards. The Convention’s annexes set the standards of design and inspection that containers must meet to ensure they are safe for handling, stacking, and transporting.
The container shipping industry relies on inspections arranged by container owners or lessors to maintain certifications. Container lines will generally not accept a container for shipment if it does not have certification.
Because of the large number of containers on the ZIM Kingston and the wide variety of owners and lessors of these containers, the investigation was not able to determine the age and maintenance history of every container on board. One of the 40-foot containers stowed in bay 14 had been manufactured 15 years prior to the occurrence; this was the oldest of the containers for which the TSB was able to obtain data. This container went overboard during the occurrence, and the investigation was unable to assess its pre- or post-occurrence condition.
1.15 Vessel certification
The ZIM Kingston is certified under the SOLAS Convention and in class with DNV. Prior to the occurrence, the vessel had last undergone an annual survey on 15 November 2020.
1.16 Container securing system
On the ZIM Kingston, similar to most container vessels, the 40-foot containers were secured on deck using components that included lashing bars, turnbuckles, twistlocks, and deck-mounted foundations (Figure 23). Twenty-foot containers were secured using similar components, as well as midlocks that secured the 20-foot containers end-to-end. The foundations were fixed to the deck or deck hatch covers and served as blocks on which the container stacks rested. The lashing bars were used in combination with turnbuckles and twistlocks to secure the containers on the lower 2 to 3 tiers.Lashing bars are secured manually, so it is normal to secure only the lower tiers because it is difficult to access containers any higher in the stack. The containers in higher tiers were secured one on top of the other using twistlocks. Containers beside each other were not secured together, meaning that each container stack was independent of its neighbouring stacks.
Container securing components have safe working loads that are typically 50% of the components’ minimum breaking strength. The minimum breaking strength is defined as the force at which the component will fail and is determined by the weakest point of the component. Most manufacturers will design components so that there is some unknown degree of strength beyond the minimum breaking strength; however, this is not guaranteed. The ratings for the container securing components in use on the ZIM Kingston are shown in Table 5.
Component | Safe working load (kN) | Minimum breaking strength (tension) (kN) | Minimum breaking strength (shear) (kN) |
---|---|---|---|
Foundations | 250 | 500 | 420 |
Lashing bars | 245 | 490 | n/a |
Turnbuckles | 245 | 490 | n/a |
Twistlocks | 250 | 500 | 420 |
Container vessels typically carry thousands of container securing components. Following the occurrence, the TSB Engineering Laboratory in Ottawa, Ontario, obtained a sampling of the ZIM Kingston’s container securing components for examination and testing.
The TSB visually examined samples of turnbuckles, twistlocks, lashing bars, and foundations from bay 14. The lashing bars exhibited mild signs of bending that would have been consistent with damage that occurred as the stacks toppled. None of the sample lashing bars or turnbuckles showed other signs of significant damage. There were scrapes, small surface marks, and corrosion that would be expected for these components. None of the damage observed would likely have led to failure.
A visual examination of sample foundations from bay 14 exhibited signs of damage and corrosion. The damage appears to have occurred once the centre of gravity for each stack fell outside the footprint of the container stack as a result of large roll angles that would have imposed significantly higher compressive forces than expected. While corrosion was present on the foundations, it did not substantially reduce the material thickness, so it was unlikely that the breaking strength was reduced.
Six twistlock samples from a variety of locations on deck, including bay 14, were inspected and subjected to hardness testing to determine their ultimate strength. The inspection showed no signs of a progressive failure (fatigue), and the failure surfaces showed signs of simple overload failures. The hardness testing identified that the twistlock samples met their safe working load specifications, with one exception. One sample, from bay 34, row 08, tier 82, had an estimated shear failure point of 389 kN, slightly below the required 420 kN minimum breaking strength in shear. It should be noted, however, that the predicted loads in bay 34 would have led the component to likely fail in tension before it failed in shear.
1.17 Cargo securing manual
A cargo securing manual provides guidance for proper use of the container securing system and for evaluating forces acting on containers. Cargo securing manuals are developed individually for each vessel by specialist companies and then inspected and approved by classification societies. Cargo securing manuals are required on all types of vessels engaged in the carriage of cargoes other than solid and liquid bulk cargoes.International Maritime Organization, MSC.1/Circ. 1353, Revised Guidelines For the Preparation of the Cargo Securing Manual, Rev. 2 (07 December 2020), paragraph 3.
The ZIM Kingston had a cargo securing manual that had been approved by DNV on 01 August 2008. The cargo securing manual included specifications for components in the cargo securing system, guidance for stowing and securing containers and non-standard cargo, and information about inspection and maintenance. Under SOLAS Chapter VI, Regulation 5, cargoes must be loaded, stowed, and secured so as to prevent damage or hazard to the vessel and the persons on board, and loss of cargo overboard.
IMO has developed the Code of safe practice for cargo stowage and securing (CSS Code), which provides an international standard for the safe stowage and securing of cargoes. It provides guidance to ensure that vessels are suitable for their intended purposes, that vessels are equipped with proper means for securing cargoes, and that cargoes are secured in a way that minimizes risk to the vessel and personnel. The CSS Code also provides advice on cargoes known to create difficulties and hazards with regard to stowage and securing, as well as actions to be taken in heavy sea conditions and actions that can be taken to remedy the effects of cargo shifting. The CSS Code refers to an IMO circular which states that cargoes “shall be loaded, stowed, and secured throughout the voyage in accordance with the Cargo Securing Manual approved by the Administration.”Ibid., paragraph 1.
1.18 Load planning
The tasks related to load planning on the ZIM Kingston were divided between ZIM shore-based ship planners, who were responsible for developing preliminary loading plans for the vessel, and crew on board, who were responsible for approving the loading plan and overseeing stowage and securing of containers in accordance with the plan.
1.18.1 Charterer’s load planning
Under the charter party, ZIM had an obligation to provide the master with a preliminary loading plan for the stowage of containers and dangerous goods to be loaded. The plan was to be provided as early as possible, and no later than upon arrival at the port of loading. Regular updates were to be provided to the vessel when any changes were made. The responsibility for developing the preliminary loading plan rested with ZIM’s shore-side ship planners. The charterer’s role in loading and stowage was explained as follows in the charter party:
The Charterers shall ensure that stowage is effected in accordance with the requirements of this Charter Party and of the vessel’s stability including, inter alia, that stack and tier weights are not exceeded. Loading to be done in accordance with the Cargo Securing Manual and all other relevant certificates and requirements of the Vessel. The stowage is always subject to the Master’s prior approval.Charter party between Balticsea Marine Inc. and ZIM Israel Integrated Shipping Services (08 June 2006), section 10(c).
Ship planners have a number of considerations to take into account when developing loading plans, including the number of ports that the vessel will be calling at; the order in which the vessel will call at these ports; and the number, size, weight, and type of containers that are planned to be loaded and unloaded at each port. Avoiding heavier containers from being loaded on top of lighter ones and minimizing the number of containers that have to be restowed are also considerations. Ship planners are required to ensure the loading plan meets the requirements of the IMDG Code, which sets out specific requirements for carriage of dangerous goods.
ZIM ship planners used load planning software that allowed for monitoring of various aspects of a loading plan, including the container stack height and weight, the number and position of reefer containers, dangerous goods containers, non-standard cargo, and restow containers. The load planning software also allowed ship planners to monitor the vessel’s bending moment, shearing forces, torsional moment, and estimated lashing forces (racking force, lifting force, compressive force,Racking force refers to transverse forces acting on a container stack; that is, forces that may cause it to topple to one side or the other. Lifting force refers to forces acting in an upward direction to “lift” the stack, and compressive forces refer to those acting in a downward direction to compress the stack. etc.) in relation to the safe working load of the components used to secure the containers on board.
To calculate the forces and moments, the load planning software used a nominal roll angle as the basis for estimating the accelerations and forces that would act on the containers during a voyage. The nominal roll angle was determined according to classification society rules and varied according to the stability (represented by GM) and roll period of the vessel when loaded for a given voyage, among other parameters.
The load planning software used by ZIM ship planners differed from that used on the vessel. An analysis of the differences between the 2 types of software was outside the scope of the investigation. Neither the ZIM ship planners nor the vessel’s crew had access to each other’s load planning software.
1.18.2 Shipboard load planning
Once the ZIM Kingston received a preliminary loading plan from the ZIM ship planners, the SMS indicated that the chief officer was responsible for checking the plan using the vessel’s loading computer to “ensure that the proposed stowage is acceptable in all respects.”Danaos Shipping Co. Ltd, Fleet Instructions Manual, Chapter 6, section 1.2.2. A copy of the plan was then to be submitted to the master for approval. The SMS also indicated that the chief officer was to use the final stowage plan to update the loading computer before departure to ensure that stability and stresses were still acceptable. The chief officer was then to provide the master with the vessel’s condition for departure.
The vessel’s load planning software provided a graphical display of the vessel’s loading plan with interactive capabilities on the bays and tiers. It allowed crew members to verify that the loading plan met the class-approved parameters for stability, stress on the hull, stowage, and segregation of dangerous goods. The software could also calculate the lashing forces that would be exerted on the containers if the vessel encountered its nominal roll angle. For the occurrence voyage, the nominal roll angle was 19.91°. The software could then compare these lashing forces against the safe working load of the container securing components and identify any containers calculated to exceed the safe working load of one or more of their securing components at the nominal roll angle. These containers were then flagged as having excessive lashing forces as shown in Figure 24.
If a loading plan proposed by a ZIM ship planner included containers with excessive lashing forces for the nominal roll angle, the master was to notify the ship planner, and they were to work together to rectify the issue. The SMS stated generally that the “vessel must not proceed to sea unless all lashing has been completed to the [m]aster’s satisfaction.”Danaos Shipping Co. Ltd, Fleet Instructions Manual, Chapter 6, section 1.2.3.
The SMS also provided for the eventuality that changes to the loading plan during loading could result in the vessel’s final pre‑departure condition having containers with excessive lashing forces for the nominal roll angle. In this situation, the master was required to notify Danaos’s operation department and issue a letter of protest to the terminal and the charterer. A letter of protest advises them that the vessel is operating outside the bounds of the charter party, and requests that they either correct the situation or assume liabilities and cost should damage arise from their action.
1.18.3 Load planning for the occurrence voyage
For the occurrence voyage, the chief officer received a preliminary loading plan from a ZIM ship planner on 30 September. The plan proposed loading 1855 containers (3460 TEU) and a cargo weight of 29 048 t. The chief officer uploaded the plan into the ZIM Kingston’s load planning software, which calculated that the vessel would have a GM of 0.83 m and a nominal roll angle of 19.91°. The software flagged containers in 14 of 16 bays on the deck as having excessive lashing forces for the nominal roll angle. In these 14 bays, the number of flagged containers per bay ranged from 5 to 76 (all of the containers in the bay).
On 03 October, the ZIM ship planner sent a revised preliminary loading plan to the vessel. The ship planner asked for the condition of all vessel tanks upon departure and the estimated condition of them at arrival at the next port. The revised loading plan proposed loading 1967 containers (3659 TEU) and a cargo weight of 30 591 t.
The chief officer uploaded the revised plan into the vessel’s load planning software, which calculated that the vessel would have a GM of 0.75 m and a nominal roll angle of 19.91°. The software flagged containers in 15 of 16 bays as having excessive lashing forces for the nominal roll angle. The chief officer informed the master of this. With this revised plan, the number of flagged containers in each bay ranged from 10 to 76.
The master notified the ZIM ship planner that the plan had been checked and provided the vessel’s departure tank conditions. The master’s response to the ship planner did not indicate that the lashing forces were excessive. The ship planner acknowledged the master’s response; they continued to correspond about changes to the plans required to accommodate gear boxes.Gear boxes are container-sized open-top boxes used to stow container securing equipment (e.g., twistlocks, lashing bars) and transfer it between the dock and the vessel.
On 05 October, the ship planner provided the vessel with a final loading plan that had 2 fewer 20-foot containers and a cargo weight of 30 552 t, making for 3657 TEU. The chief officer uploaded the plan into the vessel’s load planning software, which calculated that the vessel would have a GM of 0.74 m and a nominal roll angle of 19.91°.
The vessel’s load planning software allowed crew members to simulate changes to the vessel to see the effect on the vessel’s loaded condition. There were records in the vessel’s load planning software for 03, 04, and 05 October showing that the crew had considered some alternative ballast configurations. These alternative configurations did not reduce the number of containers that were flagged as having excessive lashing forces for the nominal roll angle. The master accepted the final loading plan and the vessel sailed in this loaded condition. A letter of protest was not filed. Post-occurrence, it was reported that the load planning software being used by the ship planner had not identified any lashing force exceedances.
1.18.4 Loaded condition upon departure
The ZIM Kingston departed on 06 October with 1965 containers (3657 TEUs) and 30 552 tonnes of cargo. Of the 1965 containers, 1273 were loaded on deck and 692 were loaded in the holds. The vessel also carried 9733 tonnes of ballast water and 3547 tonnes of fuel. The vessel’s GM was about 0.77 m.
Upon departure, the shipboard load planning software had flagged containers in 15 bays as having excessive lashing forces for the nominal roll angle. The number of containers flagged ranged from 10 to 76. Bay 62 was loaded to 141% of the racking force limits and had all of its 76 containers flagged, although no containers were lost from this bay.
For bays 14, 34, and 54 (the bays from which containers were lost), the number of flagged containers were as follows:
- In bay 14, 15 of 63 containers were flagged. Maximum exceedance was 28% over the lifting force limit.
- In bay 34, 70 of 76 containers were flagged. Maximum exceedance was 51% over the lifting force limit.
- In bay 54, 70 of 75 containers were flagged. Maximum exceedance was 70% over the lifting force limit.
Although 15 bays were determined to have containers with excessive lashing forces, none were predicted to exceed the breaking strength limits of the container securing system for the nominal roll of 19.91°. TSB calculations determined that the lashings in bays 14, 34, and 54 were likely to have exceeded the breaking strength limit if the vessel rolled to an angle of 27° or above.
1.18.5 Load planning on previous voyages
The TSB collected data regarding the ZIM Kingston’s load planning for voyages made in August and September 2021. The data indicated that the ZIM Kingston’s final loading plans for the 2 months prior to the occurrence routinely had containers in multiple bays that exceeded the lashing forces for the nominal roll angle, as calculated by the vessel’s load planning software (Table 6).
Date | Port | Number of bays where 1 or more container exceeded the lashing forces for the nominal roll angle (of 16 bays in total) |
---|---|---|
01 August | Shanghai, China | 9 |
03 August | Ningbo, China | 12 |
03 September | Los Angeles, U.S. | 14 |
13 September | Kaohsiung, Taiwan | 14 |
15 September | Xiamen, China | 15 |
17 September | Yantian, China | 12 |
21 September | Ningbo, China | 13 |
30 September | Yangshan, China | 14 |
06 October (occurrence voyage) | Busan, South Korea | 15 |
Post-occurrence, it was reported that, on the 3 previous voyages leading up to the occurrence voyage, the ZIM load planning software outputs showed the lashing forces as being within the limits for the nominal roll angle.
It is not uncommon for vessels to sail with some lashing forces beyond the safe working load of container securing components at the nominal roll angle, though still below the components’ minimum breaking strength.Container vessels sailing with lashing forces that exceeded safe limits have been identified in the following accident investigation reports: UK Marine Accident Investigation Report 14/2020 (Ever Smart), UK Marine Accident Investigation Report 2/2020 (CMA CGA Washington), Australian Transport Safety Bureau Report No. 344-MO-2018-008 (YM Efficiency), and a joint investigation by the Dutch Safety Board and Panama involving the container vessel MSC ZOE in January 2019.
1.19 Carriage of dangerous goods on vessels
The carriage of dangerous goods on vessels is largely governed by the IMDG Code, which sets out requirements for packing, documentation, container stowage, and segregation of incompatible substances, among other things. The Code also sets out requirements for vessels to undergo periodic audits to verify compliance with the Code. The SOLAS Convention requires vessels carrying dangerous goods to hold a certificate to show compliance with the construction and equipment requirements set out in the Convention.International Maritime Organization, Safety of Life at Sea (SOLAS) Convention, Chapter II-2, Regulation 19.
The ZIM Kingston carried the documentation required by the IMDG Code for the transportation of dangerous goods on the occurrence voyage. The vessel had a dangerous cargo manifest in accordance with IMDG Code regulations. The vessel also had a list of dangerous goods on board that was posted on a notice board outside the ship’s office. The list contained information about the dangerous goods on board, including the identification numbers for the containers in which they were stowed, their stowage position on deck, flashpoint, and fire schedule. The list also included emergency contact numbers for specialists for each dangerous good. The crew could access safety data sheets (SDS) for dangerous goods online. The SDS for xanthates states that when xanthates come into contact with moisture, they produce toxic and highly flammable vapours that can cause an explosion.
A number of the crew members had received company-specific training on hazardous materials from Danaos in May 2021. DNV had issued the vessel a document of compliance for carriage of dangerous goods on 02 October 2018.
The dangerous goods on board were stowed on deck or below deck in accordance with IMDG Code requirements for stowage. Xanthates and thiourea dioxide, for instance, are required to be stowed on deck only and clear of the accommodations. On the ZIM Kingston these products were stowed in bays 13 and 14 on deck and clear of the accommodations. The xanthates were packed in plastic and the thiourea dioxide was packed in drums.
Aside from the xanthates and thiourea dioxide, the ZIM Kingston also carried other containers with dangerous goods, including various gasses, flammable liquids, and corrosive substances.
1.19.1 Responding to dangerous good fires and spills
Container vessels typically do not carry specialized media for fighting fires involving dangerous goods. Crew may be limited in their ability to apply available fire suppression agents to containers because of the difficulty of accessing the containers, especially if they are stowed at height. Owing to the wide variety of dangerous goods carried on board at any given time, crew are not typically trained in specialized firefighting techniques for specific dangerous goods.
For guidance on fires and spills involving dangerous goods, the IMDG Code refers to the Emergency Response Procedures for Ships Carrying Dangerous Cargo (the EmS Guide). This guide provides general guidelines for responding to a fire involving dangerous goods, as well as a fire schedule that provides specific information about how to respond to fires involving different types of dangerous goods.
Potassium amyl xanthate is classed under the IMDG Code as a substance susceptible to spontaneous combustion. For a fire involving potassium amyl xanthate, the EmS Guide directs the use of fire schedule F-A, which is a general fire schedule for dangerous goods that recommends fighting the fire from a protected position from as far away as possible. For cargoes on deck, this fire schedule recommends creating water spray from as many hoses as possible. The schedule also cautions that exposed cargoes may explode or their containment may rupture.
The SDS for xanthates states that if only water is available for firefighting, it should be used in the form of a spray to cool structures or containers.
1.20 Firefighting equipment
The ZIM Kingston was equipped with all of the required firefighting and lifesaving equipment required under SOLAS Regulation 13, Chapter II-2. The vessel had 3 firefighter outfits and 2 additional self-contained breathing apparatuses. An air compressor for refilling breathing devices was located on the upper deck of the accommodation.
The vessel also carried a lance that could be used to puncture containers in fire situations.
1.21 Fire response procedures
The ZIM Kingston had a muster list and fire plan, as well as an emergency response procedures manual that included a checklist for a fire in containers on deck. The vessel also had a list of emergency contact numbers posted on the bridge, including that for Resolve Marine.
The emergency response procedures checklist for fire in containers on deck required the crew to identify the locations and ID number of the burning containers to determine the extent of the fire and check if dangerous goods were involved. If dangerous goods were involved, the master was to consult the IMDG Code and provide guidance to the emergency team leader for firefighting.
1.22 Fire drills
The ZIM Kingston was required to carry out fire drills every 2 weeks, according to the vessel SMS. The last fire drill had taken place on 19 October 2021, 4 days before the fire. It involved a scenario where there was a fire in a container on deck. During this drill, the crew mustered and checked various equipment involved in responding to a fire, including the firefighter outfits, fire pumps, self-contained breathing apparatuses, and communications equipment. The actions to be taken in the event of a fire in a container on deck were discussed. Some of the equipment was also demonstrated, and there was discussion about how to fight a fire involving dangerous goods.
1.23 Contract with marine emergency response company
The ZIM Kingston regularly called at U.S. ports on its trans-Pacific voyages. For vessels such as the ZIM Kingston, since 2013 the U.S. Oil Pollution Act of 1990 requires the operator to plan for salvage and marine firefighting and have contracts in place with salvage and marine firefighting resource providers that can respond in a timely manner.U.S. Code of Federal Regulations, Title 33, Chapter I, Subchapter O, Part 155, Subpart I – Salvage and Marine Firefighting. To comply with this requirement, Danaos had a contract in place with Resolve Marine that covered the ZIM Kingston. Although there is no such requirement in Canada, in this occurrence, Danaos was able to contact Resolve Marine and extend their contract to Canada.
Because Danaos had an existing contract for the ZIM Kingston, Resolve Marine had access to key information about the vessel, such as the general arrangement plan, the fire control plans, and the capacity plans. This information is integral to coordinating a fire response. Resolve Marine, being experienced with emergency response protocols, also understood the role of the ICP and became part of it.
If a vessel is not covered by a pre-existing contract with a marine emergency response company, there are mechanisms, such as the use of a Lloyd’s Open Form agreement, that allow the owner of a vessel in difficulty to quickly engage a salvor. Because salvage organizations are paid either on the basis of time plus a bonus or through a salvage award, they are incentivized to respond promptly to an emergency.
1.24 Canadian approach to marine emergencies involving hazardous and noxious substances
The term “hazardous and noxious substances” (HNS) is defined by TC as dangerous goods and other substances, aside from petroleum products, that are potentially harmful to human health and marine life when released into the environmentTransport Canada, Canada's preparedness and response for hazardous and noxious substances released from ships: discussion paper, at https://tc.canada.ca/en/marine/canada-s-preparedness-response-hazardous-noxious-substances-released-ships-discussion-paper#definition (last accessed 25 July 2024). They can be substances that are toxic, corrosive, reactive, flammable, or explosive.
Canada’s national approach to marine emergencies involving HNS is largely in the early stages. The current approach is for an ICP to be established, with the response typically led by the CCG and involving other relevant players. For a marine emergency involving HNS, key players might include representatives from the company or organization involved, federal and provincial government departments, representatives of Indigenous communities in or near affected areas, and other specialists (e.g., dangerous goods specialists, air and water quality monitoring specialists).
Once the ICP is established, a response is improvised based on the HNS situation being faced and the resources that can be obtained to assist. There is no overarching plan for how to respond to marine emergencies involving HNS, nor is there an inventory of resources and their capabilities. There are also no certified marine response organizations for HNS based in Canada, nor is there any requirement for contracts with emergency response companies, as there is in the U.S.
By contrast, the federal government does have a national regime in place to respond to oil spills. In 1995, TC established the Marine Oil Spill Preparedness and Response Regime. The guiding principles of the regime highlight the need for effective and responsive legislation and comprehensive contingency plans. They also identify the need for potential polluters to pay for preparedness and polluters to pay for reasonable response costs. Finally, the guiding principles address partnership with industry and mutual agreements with neighbours.Transport Canada, “National Oil Spill Preparedness and Response Regime – Overview,” at https://tc.canada.ca/en/marine-transportation/marine-safety/national-oil-spill-preparedness-response-regime-0 (last accessed 17 July 2024).
Under the regime, TC ensures that the appropriate level of preparedness is available to respond to marine oil pollution incidents in Canada of up to 10 000 tonnes within prescribed time standards and operating environments. The regime sets out a national preparedness planTransport Canada, “Environmental Prevention and Response National Preparedness Plan,” at https://tc.canada.ca/en/marine-transportation/marine-safety/environmental-prevention-response-national-preparedness-plan (last accessed 17 July 2024). to provide an understanding of the preparedness capacity of the marine spill response regime and to ensure mechanisms are in place to provide an adequate preparedness capacity. The plan sets out the roles of key players (e.g., TC, CCG, the vessel, marine response organizations,Marine response organizations are specialized companies that respond to a spill on a polluter’s behalf. There are 4 marine response organizations certified by Transport Canada. Environment and Climate Change Canada [ECCC]) in terms of both preparedness and response for oil spills.
The federal government has recognized that although Canada has a regime in place for oil spills from vessels, there is room for improvement around measures in place for incidents involving HNS.Transport Canada, “Marine Pollution Preparedness, Response and Recovery – Discussion Paper,” at https://tc.canada.ca/sites/default/files/2023-01/MPPRR%20Paper_EN1.pdf (last accessed 17 July 2024). TC indicates that a dedicated HNS plan has not yet been developed in part because the number of HNS releases internationally is low compared to the number of oil spills. Nevertheless, TC recognizes that an effective HNS preparedness and response program would reduce the harmful impacts of future incidences.
To this end, through funding provided under the Oceans Protection Plan,Transport Canada, “Oceans Protection Plan,” at https://tc.canada.ca/en/campaigns/oceans-protection-plan (last accessed 17 July 2024). TC and the CCG have started actioning a proposal to create a single national system to respond to all marine pollution incidents, regardless of their source. The proposal is documented in a discussion paper on Marine Pollution, Preparedness, Response, and Recovery (MPPRR).Transport Canada, “Marine Pollution Preparedness, Response and Recovery – Discussion Paper,” at https://tc.canada.ca/sites/default/files/2023-01/MPPRR%20Paper_EN1.pdf (last accessed 17 July 2024). The discussion paper indicates that the roles and responsibilities for all partners in the system would be clearly defined to make sure that the response to marine pollution incidents is timely and minimizes impact on human health and the environment.
Under the MPPRR system, TC is proposing to be the policy and legislative lead, “continuing its role in ensuring that the transportation industry is prepared to respond to marine pollution incidents.”Transport Canada, “Marine Pollution Preparedness, Response and Recovery – Discussion Paper,” p. 4, at https://tc.canada.ca/sites/default/files/2023-01/MPPRR%20Paper_EN1.pdf (last accessed 17 July 2024). The CCG would “lead the federal response to all marine pollution incidents, regardless of source” and coordinate how to prepare for and respond to marine pollution incidents with an increased network of responders, including Indigenous communities and marine response organizations. ECCC, the Department of Fisheries and Oceans (DFO), and Natural Resources Canada would continue to advise on environmental issues.
The proposal was in a feedback phase through the summer of 2023. In December 2023, TC shared that, during the feedback phase, it had received 46 formal written submissions. It had also conducted 20 meetings across the country with provincial environmental and emergency ministries, Indigenous communities and groups, marine industry stakeholders, and other interested groups. The feedback will be incorporated in TC’s policy framework for this initiative. The implementation of the national system is planned for 2027.
In the discussion paper on the MPPRR, TC also noted that it would be proposing some changes to the Canada Shipping Act, 2001 to strengthen preparedness requirements. One of the proposed changes would be to require vessels to have “arrangements for firefighting and salvage services, and a response specialist to work with the Government of Canada and other partners to manage the incident.”Transport Canada, “Marine Pollution Preparedness, Response and Recovery – Discussion Paper,” at https://tc.canada.ca/sites/default/files/2023-01/MPPRR%20Paper_EN1.pdf (last accessed 17 July 2024). In June 2023, the Canada Shipping Act, 2001 was amended to give the Governor in Council the authority to make regulations, on the recommendation of the Minister, “respecting arrangements for emergency services, including requiring vessels or classes of vessels to enter into such arrangements.”Government of Canada, Canada Shipping Act, 2001 (as amended 22 June 2023), subsection 120(1), para s.1. At June 2024, TC indicated that work to develop regulations under this provision of the Canada Shipping Act, 2001 was underway. The work is planned to continue over the next 4 years, subject to the government’s regulatory priorities. As part of this work, TC will be undertaking additional policy and risk analysis, and extensive engagement with Indigenous peoples and stakeholders.
1.24.1 Response to this occurrence
In response to this occurrence involving HNS, the CCG used the ICS to set up an ICP. Participants included the following parties:
- legal representatives for Danaos
- Resolve Marine
- various federal government departments, including TC, DFO, ECCC, and Public Safety Canada
- various BC government ministries and agencies, including the Ministry of Environment and Climate Change Strategy, Emergency Management BC, and Health Emergency Management BC
- the Pauquachin First Nation and W̱SÁNEĆ Leadership Council
The ICP established control over the firefighting response and recovery operation to locate and collect the lost cargo. On 19 November, the ICP was stood down.
Following the occurrence, the CCG produced an after-action report that reviewed the incident response.Canadian Coast Guard, “MV ZIM Kingston Incident Response National After-Action Report,” (12 October 2023). The review found that the response was generally successful because of planning, coordination, the vessel owner’s active participation, extensive responder experience, and some good fortune. The review also identified the following areas for continuous improvement:
- readiness
- communication and information sharing between response groups and agencies with differing mandates and authorities
- the definitions of the roles and responsibilities of cross-jurisdictional response partners
- plans, procedures, and training on HNS and availability of subject matter expertise, particularly for vessel cargoes
- mechanisms to mobilize marine emergency response organizations and activate local resources
- local coastal firefighting capacities
The review identified that there are certain types of maritime incidents to which the CCG does not have the capability to respond. For instance, presently, the CCG does not directly participate in marine fire suppression activities as part of incident response, nor does it have fire suppression capabilities, policies, or procedures in place to directly respond to a marine vessel fire. The review recommended that the CCG undertake an environmental scan to compile regional and national marine firefighting suppression capabilities.
1.25 Approach by other countries to marine emergency response
Maritime administrations around the world vary in their approaches to responding to marine incidents. New Zealand has developed an Integrated Maritime Incident Readiness and Response Strategy,Maritime New Zealand, “Integrated Maritime Incident Readiness and Response Strategy” (Issue 5, March 2022), at https://www.maritimenz.govt.nz/media/yxenkoeq/integrated-maritime-incident-readiness-and-response-strategy-issue5.pdf (last accessed 17 July 2024). which sets out direction for how Maritime New Zealand maintains its preparedness and response for maritime incidents and promotes a standardized and coordinated national readiness and response system. The UK and Australia have systems whereby an individual is empowered to make decisions on behalf of the maritime administration during a marine emergency. In the UK, this individual is known as a Secretary of State’s Representative (SOSRep),UK Maritime and Coastguard Agency, ”The national contingency plan. A strategic overview for responses to marine pollution from shipping and offshore installations” (17 August 2017), at https://assets.publishing.service.gov.uk/government/uploads/system/uploads/attachment_data/file/638623/170817_NCP.pdf (last accessed 19 July 2023). and in Australia, a Maritime Emergency Response Commander (MERCOM).Australian Maritime Safety Authority, “Maritime casualty management,” at https://www.amsa.gov.au/marine-environment/maritime-casualty-response/maritime-casualty-management (last accessed 17 July 2024). The European Union has several cooperative areas, such as for the Netherlands, Baltic, and North Adriatic, that are covered by Maritime Incident Response GroupsMIRG EX, “Maritime Incident Response Groups” at http://www.mirg.eu/ (last accessed 17 July 2024). in response to its Place of Refuge requirements. These groups provide fire and rescue services with the capability to carry out a rapid emergency response to vessels at sea.
Other maritime administrations, such as China, Japan, and Singapore, have requirements for vessels to have pre-arranged plans for emergency response involving HNS cargoes, and some have developed their respective coast guard organizations to have a high capability for responding to fires, search and rescue, salvage, etc.
Many maritime administrations rely on the deployment of personnel from commercial marine emergency response organizations for incidents where firefighting, salvage, or emergency towage is needed. As noted earlier, the U.S. government requires operators of vessels over a certain size to plan for emergency towing, salvage, and marine firefighting as part of their vessel response planning. Response timeframes and minimum capability for emergency towing, salvage, and marine firefighting that are tied to the vessel’s size, oil carrying capacity, and area of operation are set out by the U.S. government.
1.26 Cleaning up after container loss occurrences
According to the World Shipping Council, which undertakes surveys of its member companies to estimate the number of containers lost at sea each year, in the 14-year period from 2008 to 2021, there were on average a total of 1629 containers lost at sea each year.World Shipping Council, “Containers Lost at Sea – 2022 Update,” at https://static1.squarespace.com/static/5ff6c5336c885a268148bdcc/t/62b2d93516eba2026ec97cee/1655888181926/Containers_Lost_at_Sea_2022.pdf (last accessed 17 July 2024).
Cleaning up containers and container contents lost overboard is a complex operation that can span years, or even decades. Cleanup operations are affected by a variety of factors, such as whether the containers and contents can be located, how far the containers and contents have spread, and whether the containers and contents have sunk or remain floating. The depth of the water in which the containers have sunk may also affect recovery operations.The depth at which containers can be recovered varies depending on various factors. Following a container loss from the YM Efficiency off the coast of Australia, containers were recovered from depths ranging from 100 to 130 m (Source: Australia Maritime Safety Authority, “MV YM Efficiency – final survey results as at 30 July 2018 12:00 (AEST),” at https://www.amsa.gov.au/sites/default/files/2023-11/sd1004544197_mv_ym_efficiency_containers_30072018_1100_survey_results_fi.pdf [last accessed 23 July 2024]).
In Canada, the Wrecked, Abandoned or Hazardous Vessels Act, which came into force on 30 July 2019, provides the federal government with the power to make vessel owners clean up containers and container contents that have been lost overboard, once a hazard has been determined.The ZIM Kingston occurrence is the first occurrence to which the CCG has applied the Wrecked, Abandoned and Hazardous Vessel Act. The Act is an incorporation of the Nairobi International Convention on the Removal of WrecksTransport Canada, “Overview of the Nairobi Convention on the Removal of Wrecks, 2007,” at https://tc.canada.ca/en/corporate-services/policies/overview-nairobi-international-convention-removal-wrecks-2007 (last accessed 17 July 2024). into Canadian law. Both the Act and the Convention consider wrecks to include “equipment, stores, cargo, or any other thing that is or was on board a vessel and that is sunk, adrift, stranded, or grounded, including on the shore.”Transport Canada, S.C. 2019, c. 1, Wrecked, Abandoned and Hazardous Vessels Act (as amended 28 August 2019), Part 2, section 27.
Within Canada’s Exclusive Economic Zone,Canada’s Exclusive Economic Zone generally extends 200 nautical miles beyond Canada's territorial sea. vessel owners are liable for the costs of removing wrecks that pose a hazard to the environment; infrastructure; the health; safety, or well-being of the public; and safe navigation. Vessel owners must also handle any costs of remedial action taken by federal officers. The liability period extends to 3 years from the date that the wreck is determined to be a hazard up to a maximum of 6 years from the maritime casualty that caused the wreck.The Nairobi International Convention on the Removal of Wrecks is incorporated into the Wrecked, Abandoned and Hazardous Vessels Act under Schedule 1. With respect to liability period, section 23 of the Wrecked, Abandoned and Hazardous Vessels Act references the limits set out in the Marine Liability Act, Part 6, Division 2, Section 77, subparagraphs 6(a)(i) and (ii). Vessel owners also have certain duties related to reporting, locating, and marking of wrecks.Transport Canada, S.C. 2019, c. 1, Wrecked, Abandoned and Hazardous Vessels Act (as amended 28 August 2019), Part 1, sections 19, 20, and 21.
Vessels of 300 gross tons or more that are in Canadian waters must have a Wreck Removal Convention Certificate on board.Transport Canada, S.C. 2019, c. 1, Wrecked, Abandoned and Hazardous Vessels Act (as amended 28 August 2019), Part 1, section 24. The certificate is proof that the vessel is insured, or has financial security in place, for wreck removal costs. In Canada, TC is responsible for issuing these certificates to Canadian vessels and foreign ships that are registered in countries where the Convention is not in force. Vessels without a valid certificate are not allowed to enter or leave ports in Canadian waters and may be subject to enforcement action, including vessel detention or fines. The ZIM Kingston held a valid Wreck Removal Convention Certificate.
1.26.1 Long-term cleanup operations following the occurrence
Since the container loss involving the ZIM Kingston, members of the BC Marine Debris Working GroupThe BC Marine Debris Working Group is made up of non-profit and for-profit organizations working together to reduce plastic pollution in BC. have been helping with efforts to collect and photo-document debris from the vessel. As of 31 January 2024, these ongoing beach cleanups have found new debris that is likely from the ZIM Kingston along large stretches of the BC coastline. The freshness of the debris suggests that damaged containers are continuously releasing contents under certain deep-water conditions.
One of the working group’s members, the Rugged Coast Research Society, was contracted by the World Wildlife Fund Canada to conduct aerial and shoreline surveys to document areas where debris accumulation was known to be highest and to help determine the spread of the debris. The DFO Science Sector became aware of these efforts and supported the Rugged Coast Research Society by providing access to relevant data and records. This helped increase awareness and use of the marine debris reporting hotline that DFO had set up. It also helped to expand the number of organizations and individuals involved in debris monitoring. The aerial and shoreline debris surveys and ongoing debris monitoring efforts determined that significant quantities of debris were located around Cape Scott Provincial Park and as far southeast as Florencia Bay.
As part of DFO’s annual stock assessment trawl surveysA stock assessment trawl survey is a trawl conducted to assess the status of fisheries resources. that took place in the spring of 2022 and 2023, various bottom trawl tows were conducted in the La Perouse Bank and Swiftsure Bank areas, approximately 18 to 38 cm off the ocean floor. Both years, several items that were likely linked to the ZIM Kingston container loss were found inside the trawl, including clothing, games, and household items. The debris was found up to 180 km from the occurrence location.
In February 2023, a total of 807 different debris locations have been recorded throughout the BC coastline. Furthermore, debris linked to the ZIM Kingston and ONE ApusThe ONE Apus lost 1816 containers during a storm in the Pacific Ocean. (Source: Mike Schuler, gCaptain, “It’s Been One Year Since ONE Apus’ Epic Cargo Loss” [01 December 2021], at https://gcaptain.com/its-been-one-year-since-one-apus-epic-cargo-loss/ [last accessed 17 July 2024]). was also reported washing up on the shores of Vancouver Island, Haida Gwaii, and in Alaska, U.S.At the time of the occurrence, there were 2 unrelated federally funded shoreline clean-ups being undertaken on Haida Gwaii and in Clayoquot Sound on Vancouver Island. Several tonnes of garbage were removed from both areas as part of these clean-ups, some of which may have been attributable to the occurrence.,Some of the debris was found in national and provincial parks, including in Gwaii Haanas National Park Reserve and Naikoon Provincial Park on Haida Gwaii and in Cape Scott Provincial Park on Vancouver Island.
In July 2023, a DFO science team conducted a 2-week long science expedition on board the CCG vessel John P. Tully. The expedition used a remotely operated vehicle (ROV) and other equipment to survey the ocean floor on the continental shelf off southern Vancouver Island including the La Perouse Bank area. One of the expedition’s objectives was to map the lost containers from the ZIM Kingston occurrence and conduct visual surveys to characterize and record impacts from the containers and container debris.
The team found 29 containers on the ocean floor in a band that was 16 km long and 1 km wide extending north-northwest from the occurrence site. The majority of the 29 containers had significant damage. Fifteen of the containers could be positively identified as originating from the ZIM Kingston by matching identifying features on the containers with the vessel and its manifest. A significant amount of debris and crushed container pieces were also found in the immediate area of the container loss (figures 25, 26, and 27). Debris located included plastic wrap and packaging, couches, wicker chairs, tables and loungers, hot water heaters, and an estimated 6700 pairs of boots. Analysis of the survey of the ocean floor is ongoing.
At January 2024, only 4 of the missing containers had been found on land. Monitoring and cleanup efforts are ongoing by volunteers, non-profit organizations, and research societies.
1.26.2 Environmental risks
The risks posed by container loss are complex given the variety of cargo carried in containers. HNS can pose various risks to marine habitats, and can bioaccumulate through the food chain, eventually posing a threat to human health. Marine wildlife such as seabirds, mammals, fish, and turtles can become entangled in plastics, and they can mistake plastics for prey and die of starvation as their stomachs become filled with indigestible material. Ingestion of plastics can also cause lacerations, infections, and reduced ability to swim. Many of the marine species potentially impacted by plastics are currently listed under the Species at Risk Act.Government of Canada, Species at Risk Act (S.C. 2002, c. 29) (as amended 08 December 2023), Schedules 1-3. Other types of cargoes pose less risk and can, in some cases, create new habitat for marine life.
Subsequent to the ZIM Kingston container loss, DFO and ECCC attempted to gain an understanding of the risks posed to the environment from the lost containers by reviewing the data that was available to them: the vessel’s cargo manifest, the types of dangerous goods released into the environment, the known effects of plastic pollution, details about the environment around the occurrence location, and information on the integrity of lost containers at sea in general.
DFO and ECCC concluded that there was not enough existing research data to establish how long the containers would maintain their integrity at sea before structural failure, and so took a precautionary approach when looking at environmental risks, assuming that the containers would fail over time and release their contents. DFO and ECCC found that the vessel’s cargo manifest was not specific enough to allow for identification of all contents that may be harmful to the environment. As well, a significant amount of debris released during a container loss is likely to include packaging, plastic bags or wraps, polystyrene, and packing straps, which are known to have environmental impacts but cannot be linked back to a particular release event.
At the request of the ICP’s environmental unit, Danaos contracted the services of an environmental consulting company to assess the physical and ecological sensitivities around the occurrence location and determine the impacts the lost containers and associated debris might have on the marine environment. The report concluded that if sunken containers were to be located, recovering them would likely be a difficult process, particularly when water depth, site exposure, and risk of breaching the container were factored into a recovery operation. Breaching a container during the recovery process may cause more pollution on the sea floor or throughout the water column. The report indicated that the risks associated with recovery of sunken containers may outweigh the benefits.
The report also indicated that the occurrence site exhibited little structural diversity and low biological productivity, and that any sunken containers in the area were not anticipated to have any impacts on the environment or the nearby protected areas, provided they remained intact. The report indicated that the sunken containers might have the potential to increase the overall productivity of the site over a longer time span given the possibility for colonization of marine life on the containers.
The report concluded by indicating that minimal research has been conducted on the potential environmental implications of sunken cargo containers and, given the broad spectrum of materials and substances reported to be in the containers, it was difficult to speculate on the specific impacts of all of the contents.Pacificus Biological Services Ltd, ZIM Kingston Incident: Sunken Containers Site Characterization and Risk Profile (12 January 2022).
DFO sent the report to internal departmental subject matter experts for review. The review identified that, with respect to the environmental risks posed to the occurrence location, the grounds off Barkley Canyon, near the occurrence location, are productive fishing grounds for numerous groundfish and mid-water species that are commercially and ecologically important. High catches are related to rich euphausiid production on La Perouse bank and in the Barkley Canyon. The review also identified that the area around the occurrence location is habitat for species such as pink shrimp, spotted prawns, Dungeness and Tanner crabs, and invertebrates like sea cucumbers, sea stars, tubeworms, sponges, and coral.
The review identified that the lost containers and release of container contents presented potential risks to the productivity of Barkley Canyon. It also identified the following risks:
- research and commercial fishing gear becoming entangled with sunken containers, given that not all of the locations of the sunken containers are known; the abandoned gear can continue to catch and kill fish and other species for many years
- damage to the Ocean Networks Canada cableOcean Networks Canada is an organization that has placed underwater cameras on the sea floor across much of Canada’s coastline on the Pacific, Atlantic, and Arctic coasts to gather ocean research observation data. These cameras use cables to transmit the data that they record. that passes through the area in which the containers were lost
- marine wildlife becoming entangled in container contents or ingesting them, should the contents of the containers be released; marine wildlife identified as being present in the area in which the containers were lost includes sea birds, harbour seals, elephant seals, California sea lions, grey whales, and dolphins
- an increased number of predators being attracted into existing juvenile habitat should the sunken containers become colonized by marine species
There have been studies done on the general impacts of marine debris and container loss. For example, in the U.S., in 2004, scientists at the Monterey Bay Aquarium in California discovered a lost container at a depth of 1200 m within the Monterey Bay National Marine Sanctuary. Seven years later, researchers used a remotely operated vehicle to make visits to the container and study the impacts that the container was having on the marine environment. The study found that the marine life colonizing the container’s exterior and the seabed within 10 m of the container differed significantly from the surrounding area. The container provided a hard surface for colonization by marine life typically found in rocky habitats; however, some of the key marine life that dominate rocky habitats was absent or rare on the container, which was possibly because of potential toxicity or limited time for colonization.J. R. Taylor, A. P. DeVogalere, E. J. Burton et. al., “Deep-sea faunal communities associated with a lost intermodal shipping container in the Monterey Bay National Marine Sanctuary, CA,” Marine Pollution Bulletin, Vol. 83, Issue 1 (15 June 2014) pp. 92–106, at https://www.sciencedirect.com/science/article/pii/S0025326X14002264?via%3Dihub (last accessed 17 July 2024). The containers lost from the ZIM Kingston are at a depth of about 100 m in areas subject to active fishing and bottom currents, making a direct comparison of the impacts from the 2 container loss events unreliable.
As well, in 2006, also in the U.S., the National Oceanic and Atmospheric Administration implemented a Marine Debris Program to investigate and prevent the adverse impacts of marine debris. As part of the program, selected survey sites are routinely monitored and quantities and types of marine debris are recorded. The resulting data are used to compare quantities, locations, movement, sources, and impacts of marine debris.U.S. National Oceanic and Atmospheric Administration, “Marine Debris Program – Our Work,” at https://marinedebris.noaa.gov/our-work (last accessed 17 July 2024).
1.26.3 Marine Cargo Container Spills report
Following the ZIM Kingston occurrence, the House of Commons Standing Committee on Fisheries and Oceans undertook a study of the effects of cargo container spills on Canada’s marine environment. The study looked at environmental impacts, the speed and efficacy of responses to cargo spills, jurisdictional gaps, and polluter responsibility and financial accountability. The resulting reportHouse of Commons of Canada Standing Committee on Fisheries and Oceans, “Marine Cargo Container Spills” (October 2022), at https://www.ourcommons.ca/Content/Committee/441/FOPO/Reports/RP11818796/foporp06/foporp06-e.pdf (last accessed 17 July 2024). made a number of recommendations, including the following related to container pollution:
- That DFO implement a marine debris monitoring and management plan that adequately addresses all forms of marine debris impacting coastlines.
- That the Government of Canada invest in research and monitoring to understand the impacts of polystyrene and other plastics entering our oceans and improve how these products are removed to prevent ecological harms.
- That the Government of Canada work with the IMO to develop standards and requirements for locating devices to be incorporated in shipping containers, and that the CCG and TC consider the feasibility of installing location and tracking devices on shipping containers to assist in locating lost and sunken containers.
The committee recognized that the current response process does not provide sufficient funding for long-term cleanup operations and recommended that the federal government examine alternative mechanisms that would go beyond the current statutory limitation of liability of 3 or 6 years and would ensure that sufficient funds are available for immediate and long-term environmental damage caused by marine cargo container spills.
In February 2023, the Minister of Transport responded on behalf of the Government of Canada to the committee’s recommendations.The Honorable Omar Alghabra, Minister of Transport, “Government Response to the Sixth Report of the Standing Committee on Fisheries and Oceans,” at https://www.ourcommons.ca/DocumentViewer/en/44-1/FOPO/report-6/response-8512-441-131 (last accessed 17 July 2024). The Minister’s response indicated that, since 2019, the federal departments have been working to reduce plastic pollution and transition to circular and sustainable systems where plastics stay in the economy and out of the environment. The response stated that over 10 million dollars of funding has been provided for 39 projects to conduct research into the ecotoxicological and human health effects of plastics.
The Minister’s response also stated that, through the Oceans Protection Plan, the Government of Canada plans to invest in scientific research and operational solutions to enhance Canada’s response to marine incidents. With respect to the need for a container debris monitoring and management plan, the Minister’s response indicated that this is being addressed through existing programs, such as the Zero Plastic Waste Strategy,Environment and Climate Change Canada, “Canada’s Zero Plastic Waste Agenda,” at https://www.canada.ca/en/environment-climate-change/services/managing-reducing-waste/reduce-plastic-waste/canada-action.html (last accessed 17 July 2024).,Canadian Council of Ministers of the Environment, “Strategy on Zero Plastic Waste,” at https://ccme.ca/en/res/strategyonzeroplasticwaste.pdf (last accessed 17 July 2024). which is focused on preventing, reducing, reusing, recovering, and cleaning up plastic waste. The Zero Plastic Waste Strategy sets out the responsibilities of the various federal departments with respect to plastics and identifies TC as the department responsible for marine debris originating from shipping and ships.
1.27 The International Convention on Liability and Compensation for Damage in Connection with the Carriage of Hazardous and Noxious Substances by Sea, 2010
The international framework for the “polluter pays” concept in relation to HNS is set out in the International Convention on Liability and Compensation for Damage in Connection with the Carriage of Hazardous and Noxious Substances by Sea, 2010 (the HNS Convention). The HNS Convention was adopted in 2010, but it has not entered into force. Twelve states must ratify it before it can enter into force, with at least 4 of the ratifying states having not less than 2 million units of gross tonnage. At January 2024, 8 states had ratified the HNS Convention, including Canada. Five of the ratifying states have more than 2 million units of gross tonnage.
1.28 Previous occurrences
1.28.1 Container loss related to parametric rolling
| Maersk Essen, 2021A | ONE Apus, 2020B | CMA CGM G. Washington, 2018C | Svendborg Maersk, 2014D | P&O Nedlloyd Genoa, 2006E | APL China, 1998F |
---|---|---|---|---|---|---|
Inadequate information and tools |
Yes | Yes | No | Yes | Yes | No |
Inadequate procedures | Yes | No | Yes | Yes | Yes | Yes |
Inadequate training and awareness |
No | Yes | Yes | Yes | Yes | Yes |
A Danish Maritime Accident Investigation Board, “Maersk Essen: Marine Accident Report on Loss of Cargo, 16 January 2021,” at https://dmaib.com/media/8489/maersk-essen-loss-of-cargo-on-16-january-2021.pdf (last accessed 17 July 2024). |
- There are significant benefits to predicting parametric rolling based on real-time conditions rather than on forecasts (Maersk Essen).
- The commercial objectives of container vessels do not promote caution around voyage planning and influence masters’ decision making. However, commercial considerations were of little relevance when the conditions for the forthcoming voyage did not present themselves as hazardous to the ship (Svendborg Maersk).
- Vessels that have flat transom sterns and significant bow flares are the most vulnerable to parametric rolling because of the significant changes in stability these vessels undergo in head and near head seas (APL China).
- Parametric rolling applies loads to on-deck container stacks and securing systems that are well beyond those derived from classification society guidelines or predicted through linear seakeeping analysis (APL China).
1.28.2 Container loss and related pollution
Between 2014 and 2024, there has been 1 other reported occurrence of a container vessel losing containers off the west coast of Canada in Canadian waters. On 03 November 2016, the container vessel Hanjin Seattle lost 35 containers at the entrance to Juan de Fuca Strait.TSB Marine Transportation Safety Occurrence M16P0408. Several days later, pieces of the containers, including a refrigeration unit, washed ashore in the area around Tofino, including in Vargas Island Provincial Park and Pacific Rim National Park Reserve. The owners of the Hanjin Seattle had filed for bankruptcy a few months before the occurrence and, as a result, only a small amount of the cleanup costs could be recovered from them.
Between 2019 and 2024, there have also been 2 occurrences of container vessels losing containers in the northeast Pacific Ocean outside of Canadian waters. The Japanese-flagged container vessel ONE Apus lost 1816 containers on 01 December 2020, and the Danish-flagged container vessel Maersk Essen lost 689 containers on 16 January 2021.
It is not unusual for pollution from lost shipping containers to continue to wash up on shore long after the occurrence. Reports from around the world show that the contents of lost and sunk containers continue to pollute decades later. For example, following the loss of a container overboard in the early 1980s near the English Channel and France’s Finisterre region’s marine park, locals have been collecting debris from the container for 35 years: bright orange plastic pieces of landline novelty phones shaped like the cartoon cat Garfield.British Broadcasting Corporation, “Garfield phones beach mystery finally solved after 35 years” (28 March 2019), at https://www.bbc.com/news/world-europe-47732553 (last accessed 17 July 2024). And in February 1997, the container ship Tokio Express lost 62 containers overboard off the southwest coast of the United Kingdom. LEGO pieces from one of the containers continue to be found 26 years later.M. Weisberger, “5 million shipwrecked Legos still washing up 25 years after falling overboard, LiveScience (published 12 February 2022), at https://www.livescience.com/great-lego-spill-25th-anniversary (last accessed 17 July 2024).
1.28.3 Shipboard fires
Between 01 January 2009 and14 March 2024, at least 571 occurrences reported to the TSB involved fires on vessels. The TSB is currently investigating 3 occurrences involving shipboard fires.TSB marine transportation safety occurrences M24C0017, M23C0104, and M22A0258. The TSB has also previously completed a number of investigations involving shipboard fires:
- On 23 January 2020, a fire occurred in the sauna area on board the Newfoundland Lynx while off the coast of Newfoundland. Crew were able to extinguish the fire successfully. When the vessel returned to shore, the local fire department boarded the vessel to ensure that the fire had been successfully extinguished. The TSB investigation determined that the vessel had inadequate firefighting gear, procedures, and fire drills.TSB Marine Transportation Safety Investigation Report M20A0003.
- On 15 December 2019, the bulk carrier Tecumseh had a fire in the engine room while transiting the Detroit River off Windsor, Ontario. There were 16 crew members on board at the time. The vessel dropped both anchors, and the fixed fire suppression system was used to extinguish the fire. The fire later re-ignited, and the vessel was towed to the Port of Windsor, where the fire was extinguished on 16 December with the assistance of shore-based resources. Following the TSB investigation, the Board issued a safety concern stating that some Canadian ports and harbour authorities may lack the proper equipment, training, and resources to respond effectively to shipboard fires occurring within their jurisdiction, which could result in fires that endanger crews, the general public, property, and the environment.TSB Marine Transportation Safety Investigation Report M19C0403.
- On 31 January 2018, a fire broke out in the engine room of the container vessel MOL Prestige while the vessel was off Haida Gwaii, BC. There were 22 crew and 1 supernumerary on board at the time. The fire was eventually extinguished. Five of the crew members were seriously injured. The CCG ship Sir Wilfrid Laurier assisted until a salvage tug arrived and towed the disabled vessel to Seattle, Washington, U.S. The TSB investigation determined that the fire was caused by maintenance issues in the engine room of the MOL Prestige.TSB Marine Transportation Safety Investigation Report M18P0014.
- On 11 August 2001, the bulk carrier Windoc was struck by a lowering vertical-lift bridge while proceeding downbound in the Welland Canal at Allanburg, Ontario. The vessel’s wheelhouse and funnel were destroyed. The vessel drifted downstream, caught fire, grounded, and was subsequently declared a constructive total loss. The bridge had structural damage, and the Welland Canal was closed to vessel traffic for 2 days. There were no serious injuries or pollution. The TSB investigation determined that the responding fire brigade’s lack of training and experience in fighting shipboard fires, the lack of equipment to access the vessel, and the non-accessibility of fire control plans hindered an effective firefighting response.TSB Marine Investigation Report M01C0054.
1.29 TSB Watchlist
The TSB Watchlist identifies the key safety issues that need to be addressed to make Canada’s transportation system even safer.
Safety management is a Watchlist 2022 issue. Although the ZIM Kingston had an SMS, it did not contain procedures to guide the master in identifying and avoiding conditions that are conducive to parametric rolling. Additionally, the guidance in the SMS around loading was vague and was not consistently applied to ensure that the container load remained within safe limits.
ACTIONS REQUIRED Safety management will remain on the Watchlist for the marine transportation sector until
|
1.30 Laboratory reports
The TSB completed the following laboratory reports in support of this investigation:
- LP006/2022 – Analysis of Cargo Securing Mechanisms
- LP177/2021 – VDR Analysis
The National Research Council Canada completed the following report in support of this investigation:
- NRC-OCRE-2022-TR-056 – Physical Modelling to Investigate the Motion Characteristics of “Zim Kingston” Containership in Harsh Environments
2.0 Analysis
A total of 109 containers were lost overboard from the ZIM Kingston, and a number of other containers that remained on board were damaged when the vessel rolled 36° to both port and starboard. Around 36 hours later, fire broke out in one of the damaged containers on board that contained dangerous goods. The fire subsequently spread to adjacent containers.
The analysis will look at the factors involved in the container loss and subsequent fire; the policies, procedures, and tools that were available to the crew to monitor for and manage risk associated with parametric rolling; and guidance to industry on this topic. The analysis will also look at the loading of the vessel; the environmental impacts of container loss; and Canada’s preparedness for marine emergencies.
2.1 Container loss
As the ZIM Kingston was nearing Vancouver, British Columbia (BC), the master made a request for an anchorage for the vessel’s estimated time of arrival of 0300 on 21 October 2021. This was because he had concerns about the vessel’s navigational safety given the forecast weather conditions. Subsequent to this request, the master was informed that there were no anchorages available. He then held the vessel offshore at La Perouse Bank while awaiting a berth at the Port of Vancouver.
While offshore, the vessel’s bow was oriented into the oncoming waves. The wave periods were about half of the vessel’s roll period, and the wave lengths were similar to the vessel’s length. When these conditions converge with other vessel-specific factors in a precise way, dangerous rolling motions can develop, such as were experienced in this occurrence. Model testing conducted during the investigation demonstrated that the ZIM Kingston experienced parametric rolling.
There are numerous factors that affect the ability of a container securing system to withstand the conditions that may be experienced during a voyage. For this reason, it is often very difficult to pinpoint a single factor that fully explains a container loss event. Furthermore, even if a given factor is determined to have played a role, the degree to which it contributed to the container loss event may not be quantifiable.
For the occurrence voyage, the investigation identified various factors, in addition to the 36° roll, that may have played a role in the container loss event:
- One or more of the container securing components in the affected bays could have been weak, causing the associated container stacks to collapse. Although the TSB was able to test some samples of the vessel’s container securing components and their condition was found to be generally consistent with industry standards, it was not possible to test all the securing components after the occurrence.
- One or more containers in the affected bays may have been in a weakened condition and may have failed, causing the associated container stacks to collapse. As there are no certifications that attest to the condition of shipping containers, there were no records with which to determine their condition.
- The vessel was loaded such that safe working loads were exceeded in many locations, as determined by the load planning software for the nominal roll angle of 19.91°. However, it was not clear if or how this contributed to the container loss.
- There may have been various mechanisms that exacerbated the forces acting on the containers and securing components, such as structural vibrations (springing and whipping), shifting of container contents, and sea water impacting the side of the container stacks. It was also not clear if or how these mechanisms contributed to the container loss.
- When a vessel is in motion in a seaway, forces due to acceleration are generated. Model testing of the ZIM Kingston determined that, at the time of the occurrence, these accelerations may have reached 0.95 g. However, the extent to which the forces affected each container’s individual securing components is not known.
TSB calculations determined that the lashing forces, when estimated on a static basis and without taking into account any of the above factors, would have exceeded the breaking strength of the vessel’s container securing components at vessel incline angles of 27° or greater. The vessel roll angles at the time of the occurrence were above 27°, leading to the conclusion that the significant roll angles experienced by the vessel were the key factor that precipitated the failure of the vessel’s container securing system and the loss of the containers.
It must be noted that containers were lost only from bays 14, 34, and 54, and that the bays that had containers with the most excessive lashing forces did not lose containers. These anomalies are likely explained by the container securing system having some unknown degree of strength beyond the nominal breaking strength and/or the involvement of one or more of the factors listed above.
2.2 Monitoring for and managing the risk of parametric rolling
In the hours that the ZIM Kingston had been drifting and motoring in a holding pattern offshore, the master had positioned the vessel so that the bow was oriented into the oncoming waves, which is standard practice in adverse conditions. The master also knew that other container vessels were holding in the same area as they awaited berths in Vancouver. The master was observing the wind and waves and was satisfied with the vessel’s speed and pitching and rolling behaviour. Post-occurrence analysis of the pertinent vessel and environmental parameters in the time leading up to the occurrence shows that the vessel was at risk of developing parametric roll resonance and that this risk was identifiable using some of the guidance material generally available to the industry. However the risk was not identifiable with the guidance on board the vessel at the time of the occurrence.
A vessel’s vulnerability to parametric rolling will vary based on vessel-specific characteristics, such as stability, hull geometry, size, and speed. For this reason, 2 container vessels drifting in the same sea conditions may react quite differently because of their different characteristics, with 1 of the vessels encountering parametric rolling while the other does not. This variation underscores a need for risk assessments around parametric rolling to be vessel-specific.International Maritime Organization, MSC.1/Circ. 1228, Revised Guidance to the Master for Avoiding Dangerous Situations in Adverse Weather and Sea Conditions (11 January 2007).
Previous investigations by other agencies have shown that assessing the risk of parametric rolling is complex and it is difficult to predict exactly when a parametric rolling event will occur. Furthermore, once parametric rolling starts, it may not be possible to stop it before negative consequences, such as container loss, occur. This means that there must be a focus on monitoring for the conditions that give rise to parametric roll resonance so that mitigating measures can be taken to prevent the onset of dangerous motions when these conditions are present. Doing so requires bridge crew to have access to
- formal policies and comprehensive procedures for managing the risk of parametric rolling; and
- effective tools to help them monitor the numerous conditions affecting the vessel motions, analyze the risk of parametric rolling, and implement mitigating measures when necessary.
2.2.1 Policy and procedures
The fleet instructions manual for the ZIM Kingston, issued by the vessel’s ship manager, Danaos Shipping Co. Ltd. (Danaos), described parametric rolling as being violent in nature and a widespread concern for container vessels with significant negative consequences. The manual included a list of qualitative general conditions that need to exist for parametric roll resonance to occur, such as “a resonance” between the wave encounter period and the natural roll period, a “fairly large” wave height, and “low” roll damping. The manual also referred to a booklet on the subject published by DNV in 2005 that was available on the vessel’s bridge. However, neither source identified when a parametric rolling risk assessment for the ZIM Kingston should be done, how it should be done, what results would represent unacceptable risk, or what mitigating measures should be taken and when.
In the absence of formal policies and comprehensive procedures to support an assessment of risk related to parametric rolling, the master had to rely on his knowledge and experience to evaluate the safety of the vessel as it maintained a holding pattern in the open ocean. The master had a general understanding of the conditions that can lead to parametric rolling and the actions to take if it happened (changing course and speed), but he had never experienced parametric rolling firsthand and had never completed a quantitative assessment of risk specific to parametric rolling.
2.2.2 Tools
A quantitative assessment of risk for parametric rolling requires a variety of data related to vessel stability, environmental conditions, and vessel performance. Specifically, it requires both predicting a vessel’s stability and performance in forecast environmental conditions and monitoring actual stability and performance in real-time environmental conditions. The quality of the risk assessment will naturally be significantly influenced by the accuracy and reliability of that data. Data requirements include
- vessel stability (metacentric height [GM] and natural roll period);
- vessel performance (speed over ground and heading); and
- environmental conditions (significant wave height, direction, and period).
These data must then be used to calculate relevant parameters, such as the wave encounter direction and period, and compare them against criteria that establish level of risk. Considering that all of these data are constantly changing, forecasts need to be updated frequently and continuous real-time monitoring of environmental conditions and vessel performance is required.
Depending on the tools available to the bridge crew, the process of assessing risk may vary along the following parameters: resource intensity, time consumption, and level of certainty. On the low end of the scale (more human resources and time, less certain), bridge crew would use periodic, manual collection of vessel stability and performance data, observations of sea conditions, and paper-based calculations or graphs. On the high end of the scale (less human resources and time, more certain), bridge crew would use automated and integrated equipment that is capable of sensing and collecting vessel-specific data in real time, analyzing the data with an algorithm that can detect an onset of parametric roll resonance, and continuously displaying the vessel’s prevailing level of risk.
The tools available to the bridge crew of the ZIM Kingston for assessing the risk of parametric rolling were low on the scales of sophistication, ease of use, and certainty. With respect to the data required related to vessel stability, vessel performance, and environmental conditions, the bridge crew had access to the following:
- For vessel stability, the vessel was equipped with load planning software that could calculate static stability and roll period information based on vessel loading conditions, but this data was only as current and as certain as the most recent input.
- For vessel performance, on-board navigation equipment provided vessel speed and heading, but these data vary significantly with time and so procedures for determining useful data points as input to risk calculations would be needed.
- For environmental conditions, forecast data was readily available; however, it is inherently uncertain, and is not suitable for combining with other real-time data for ongoing risk monitoring. Real-time sea condition data could be collected on board by observation; however, this method of data collection is also prone to uncertainty due to the subjectivity of the observer and is not practical for continuous monitoring. It can also be challenging to observe real-time sea conditions if visibility is limited by weather or darkness.
These various data sources were independent, so before doing any calculations, one or more individuals would need to consult each source to extract relevant data, then consult the owner-supplied on-board guidance material to perform the necessary calculations and assessment. Guidance material did not offer any detailed instructions or formulae (for calculating wave encounter period, for example) for their application to the ZIM Kingston, and the limits for acceptable risk were vague and inconsistent. For example, according to the owner’s fleet instructions manual, there is a risk of parametric roll resonance if there is resonance between the wave encounter period and “the natural roll period or twice the natural roll period.” However, the DNV booklet put the limit at half the natural roll period. In any case, when these guidance materials were used after the occurrence to assess the risk of parametric rolling around the time of the occurrence, neither of them indicated that the vessel was at risk.
2.3 Guidance to industry for managing the risk of parametric rolling
Effectively managing the risk of parametric rolling on container vessels is challenging. It is essential for bridge crew serving on container vessels to be aware of the factors that lead to parametric rolling and to be familiar with measures to prevent it and respond to it. Bridge crew must have access to vessel-specific data and tools to predict risk in advance, on the basis of weather and sea state forecasts. This is especially important for voyage planning and comparing the safety of alternative routes. Bridge crew must also have data and tools that allow for ongoing monitoring of risk during the voyage, based on actual operating conditions. And finally, there must be shared understanding of risk among owners, charterers, and other shore-based personnel so that bridge crew are supported in making decisions necessary for the safety of the vessel on its voyage.
Decision making by masters is influenced by many factors, including training, experience, and guidance provided by written procedures and instructions. The potential for commercial pressure to influence a master’s decision making is also an important factor. In this occurrence, ZIM Integrated Shipping Services Ltd.’s (ZIM) sailing instructions put a high priority on minimizing fuel consumption and required the master to explain routing decisions that differed from Weathernews Inc.’s (WNI) recommendations. The instructions also included a clause specifying that “[l]ack of confidence and/or reluctance in executing duties as per Charterer’s requirements shall not be justified by [safety of the vessel] and will be challenged by Charterer with no delays.”ZIM Global Operations, General Sailing Instructions for ZIM/GSL Operated Vessels (June 2021), section 2.4. The charter party gave ZIM the contractual right to request replacement of masters if dissatisfied with their performance. These provisions are standard contractual terms used throughout the global shipping industry. While the investigation could not determine whether these provisions directly played a role in this occurrence, their use in the container vessel industry may subtly influence decision making towards commercial gains.
Investigations by other investigation agencies into previous occurrences involving parametric rolling point to inconsistencies and inadequacies with respect to the training of bridge crew and the adoption of procedures and tools to support them in managing the risk of parametric rolling. A substantial number of resources are available, including articles, videos, circulars, presentations, research papers, and class society publications, that target a variety of audiences and present different guidance for assessing the risk of parametric rolling (from visual sea state observations used in combination with paper charts to sophisticated vessel motion sensors and computer-based algorithms). However, none of these resources provide comprehensive guidance to help vessel owners, charterers, and bridge crew manage the risk of parametric rolling effectively, taking into account the need for
- information about parametric rolling to be presented in an accessible and understandable way;
- clear guidance to help bridge crew practically apply this information, i.e. specific directions about when risk assessments should be done, how they should be done, what results represent unacceptable risk, and what mitigating measures should be considered;
- company policies and procedures that foster a shared understanding of the risk around parametric rolling among all parties involved (owners, charterers, bridge crew) and ensure that bridge crew receive support in making safety-related decisions;
- effective tools to support bridge crew in managing the risk of parametric rolling;
- crew to have an understanding of the merits and limitations of these tools; and
- training, as well as guidance on its development and implementation, so that policies, procedures, and tools can be used to full effect.
A look at the guidance materials and tools that are currently available to industry for assessing the risk of parametric rolling highlights the challenge of finding a balance between materials and tools that are trusted, effective, practical, and affordable. The International Maritime Organization (IMO) is generally recognized as the international body best-positioned to develop and disseminate guidelines to the marine industry; however, its circular addressing the risk of parametric rolling has not been updated in over 17 years and the investigation identified several shortcomings with it, as follows:
- The circular is intended for all types and sizes of vessels and addresses several different dangerous motion mechanisms; as a result, it may be too restrictive for some vessels and too generous for others. As well, the circular’s operational guidance with respect to parametric rolling is minimal and contained in a single paragraph.
- The circular characterizes parametric rolling as a heavy weather phenomenon, but model testing for the ZIM Kingston found that parametric rolling could develop in significant wave heights as low as 2.6 m.
- The circular addresses the risk of parametric rolling using 2 different approaches: one intended to address a variety of dangerous motions that can result from a successive high-wave attack in following seas and the other intended to avoid parametric rolling in waves from a variety of encounter directions; the use of different approaches could be confusing to users.
- The circular does not offer any guidance with respect to policies, procedures, training, tools, or services related to the management of risk associated with parametric rolling.
Once made mandatory, the criteria in the IMO Interim Guidelines on the Second Generation Intact Stability Criteria should minimize the risk of parametric rolling, in addition to other dynamic stability failure modes. The guidelines will provide a consistent approach to address the risk across the international shipping industry, either by virtue of improved vessel designs or operational limitations and guidance. However, the timeline for the incorporation of these guidelines into the International Code on Intact Stability, 2008 is unknown, and it is not clear whether they will apply to existing vessels. The guidelines also do not address the training of crew with respect to this issue. Similarly, it is unclear, at this time, whether the work of the IMO Subcommittee on Carriage of Cargoes and Containers will address the issues identified in this investigation.
2.4 Cargo fire and on-board response
When containers from bays 14, 34, and 54 fell overboard, several of the remaining containers in those bays were damaged, as were their contents. Three of the damaged containers in bay 14 contained potassium amyl xanthate packed in plastic liners. The damage to the containers caused damage to the liners, allowing water to come in contact with the xanthates, which started a fire. The fire subsequently spread to 5 other nearby containers, 2 of which also held xanthates and 3 of which held tires and other consumer items.
Once the fire was detected, the crew responded efficiently and followed industry and company guidelines for firefighting. There is no practical way to extinguish burning xanthates on a vessel at sea; the recommended response is to contain the fire by establishing boundary cooling and wait for the fire to burn out. The Maersk Trader and Maersk Tender were fortuitously docked nearby in Victoria, BC, and were promptly contracted to respond by the shipowner’s salvage contractor. The use of these vessels, with their more powerful pumps, to aid in the boundary cooling was instrumental to limiting the extent of damage from the fire.
The decision to retain a skeleton crew on board to continue boundary cooling, while making preparations such as the installation of emergency towing pennant wires for complete abandonment of the vessel, was done on the recommendation of specialized shore-based personnel and assisted with the emergency response.
Finding: Other
Danaos’s contract with an emergency response company meant that the ZIM Kingston had access to specialists who provided guidance throughout the emergency response and a team of trained personnel who were able to board the vessel to help fight the fire.
2.5 Safe loading of container vessels
Under regulations set out by the International Convention for the Safety of Life at Sea (SOLAS), containers need to be loaded, stowed, and secured in accordance with a cargo securing manual approved by the vessel’s administration.International Convention for the Safety of Life at Sea (SOLAS) (1974, last amended 2020), Chapter 6, Regulation 5; and Chapter 7, Regulation 6. Among other things, the cargo securing manual sets out the safe working load for the container securing components. The safe working load is used in combination with the vessel’s nominal roll angle to establish safe lashing force limits for the containers. If the loaded condition of the vessel exceeds the safe lashing force limits (racking force, lifting force, compressive force), the vessel is operating with a reduced margin of safety.
The fact the ZIM Kingston sailed on the occurrence voyage with containers that exceeded the safe lashing force limits was not causal to the container loss. Even if all of the containers had been within the lashing force limits, calculations by the TSB indicate that the container loss would likely still have happened because the rolling the vessel encountered was so extreme. As well, bay 14 was within the racking force limits and had only 15 containers that were flagged by the vessel’s load planning software as having excessive lashing forces, yet it was the bay where the most containers were lost. In contrast, bay 62 was loaded 41% over the racking force limit and had all of its 76 containers flagged, yet it did not lose containers. This demonstrates that there was no direct correlation between the containers that exceeded the lashing force limits and the container loss in this occurrence. However, sailing with lashing forces that exceed safe limits erodes the margin of safety that is in place to protect against container loss.
The investigation determined that, during the 2 months prior to the occurrence, the ZIM Kingston routinely sailed with bays in excess of the lashing force limits. There could be a number of factors that led to the acceptance of loading plans with lashing forces that exceeded the limits, including the following:
- The safe working load of the container securing components was half that of their breaking strength and was exceeded only if the vessel rolled beyond the nominal roll angle of 19.91°, which is a significant roll.
- The voyage could be planned to reduce the chances of encountering situations where the vessel might reach its nominal roll angle.
- There had been a number of previous voyages where containers exceeded the lashing force limits with no negative consequences.
- The vessel’s relevant safety management system guidance on remaining within lashing force limits was vague and did not explicitly prohibit the vessel from departing if it exceeded lashing force limits; in fact, it included a procedure for notifying the charterer in the event it did.
- In the container shipping industry, there are commercial and scheduling pressures to expedite and prioritize cargo operations.
For the ZIM Kingston, the tasks associated with load planning were divided between ZIM ship planners and the master. The ship planners were tasked with preparing a load plan that was within lashing force limits, and the master was responsible for ensuring that the vessel was loaded in a manner that kept it within lashing force limits. The investigation obtained the load plans sent by ZIM ship planners to the vessel for the occurrence voyage and the 8 preceding it, and found that all of these load plans exceeded the lashing force limits in the vessel’s load planning software. Post-occurrence it was reported that the ZIM load planning software outputs had showed the load plans for the occurrence voyage and the 3 voyages that preceded it as being within lashing force limits. The investigation was unable to determine why there may have been a discrepancy in ZIM’s outputs and the vessel’s outputs for these particular voyages.
The ZIM Kingston is not a unique example of a container vessel sailing with lashing forces that exceeded safe limits. Other international occurrences have identified the same issue.Maritime Accident Investigation Board, “Loss of cargo containers overboard from container ship Ever Smart,” at https://www.gov.uk/maib-reports/loss-of-cargo-containers-overboard-from-container-ship-ever-smart (last accessed 17 July 2024). Although masters are responsible for adhering to standards and limits for the safe loading of their vessel, in practice, various factors that are out of their control can limit their ability to do this. These include commercial and scheduling pressures to expedite cargo operations, as well as the complexity of load planning considerations when loading and discharging cargo in multiple ports (e.g. ensuring dangerous goods are appropriately segregated, avoiding restowing containers).
Although masters have ultimate authority when it comes to their vessel’s safety, they must also be supported in their decision making by a strong safety culture. Without this support, it can be difficult for masters to be the sole champions of safety. Charterers typically have a vested commercial interest in maximizing the cargo carrying capacity of the vessel and expediting the vessel’s movements. It is up to the owners to ensure that the commercial interests of the charterer do not interfere with the safety of the vessel. In this occurrence, the charterer’s sailing instructions specifically stated that the master’s use of safety as the rationale for a decision could be questioned by the charterer. The charterer also had a standard clause in the charter party stating that it could request that the master or officers be replaced if dissatisfied with their conduct.
2.6 Environmental impacts of container loss
In general, lost containers at sea pose a hazard to navigation while floating and, once they drift ashore or sink and break apart, can pose a significant risk to coastal environments and marine habitats depending on their contents.
In this occurrence, an estimated 1490 tonnes of containers and container contents were lost overboard, around 48 tonnes of which were recovered during short-term cleanup efforts. This means that an estimated 97% of what went overboard remains on the ocean floor, suspended in the water column, or washed up on remote areas of coastline off Canada and Alaska, United States (U.S.).
The volume and variety of contents lost overboard in this occurrence, as well as the general lack of studies on container spills, make it difficult to establish the environmental effects that this occurrence will have on Canadian waters and coastlines. As well, the cargo manifest was not specific enough to identify all of the constituent components of container contents that have the potential to affect the marine environment.
Recognizing that there is a gap in understanding the impacts of containers lost at sea, the Department of Fisheries and Oceans (DFO) undertook a survey to map the lost containers from the ZIM Kingston to better understand the impact on the marine environment. DFO indicated that, given the volume and area of the container loss, there will be clear impacts on the marine environment; these impacts can be documented with further surveys and analysis.
In Canada, polluters are required by law to cover the costs associated with cleaning up the pollution they have generated. The requirement for cleanup of containers and container contents lost overboard falls under the Wrecked, Abandoned or Hazardous Vessels Act. If the loss qualifies as a pollutant, there may also be obligations for the polluter under the Marine Liability Act. Although regulations can require a polluter to pay for cleanup costs, it does not mean that environmental impacts from container loss can be completely avoided. This is because a number of factors can hinder cleanup after container loss occurrences. For example:
- It is not always possible to locate or access containers and debris, especially if they have sunk in deep water.
- Containers may break apart and release debris for years, or even decades, after the original container loss.
- It may not be possible to establish ownership of container debris and therefore establish who is responsible for the cleanup.
- Debris from containers, such as polystyrene and plastic wrap used for packaging, may spread out over several locations in quantities that are not considered significant enough to contact the owner.
- Cargo documentation may not be specific enough to allow for debris to be linked to a vessel.
- Debris may become suspended in the water column or remain on the ocean floor, as shown by the debris found in the DFO trawl surveys, and never wash ashore.
- It may be impossible to identify the polluter, or they may be uncooperative or incapable of taking on the financial responsibility for their pollution.
In this occurrence, a debris removal plan was developed to address existing stranded containers and debris, and Danaos Shipping Co. Ltd. took on the responsibility for the initial cleanup efforts, which concluded in December 2022.
As of January 2024, DFO reported that fresh debris was continuing to wash up on BC’s coastline, indicating that the containers from the ZIM Kingston were continuing to release debris. DFO reported that the majority of the 29 containers found on the ocean floor from the ZIM Kingston had significant damage. Based on the state of these 29 containers, DFO estimated that the remaining containers have some or significant damage and either have released debris or are at continuous risk of releasing it. Members of the BC Marine Debris Working Group continue to help with efforts to collect debris from the coastline.
As many reports have shown around the world, contents from containers lost at sea continue to pollute decades after an occurrence. In Canada, there are statutory limitations on liability for the owners under the Wrecked, Abandoned or Hazardous Vessels Act. Specifically, the limitations are 3 years from the date that the wreck is determined to be a hazard up to a maximum of 6 years from the maritime casualty that caused the wreck. These limitations can pose challenges for getting owners to remove containers and debris that continue to pollute for many years after a container loss occurrence. As well, any new debris found has to be proven as coming from the container loss, which is another challenge for getting owners to remove containers and container debris.
Finding: Other
Canada does not have a program to monitor and assess the long-term impacts of lost containers or the debris from lost containers, and the impacts on marine ecosystems are relatively unknown.
2.7 Canadian preparedness for marine emergencies
This occurrence demonstrated some of the challenges involved in dealing with emergencies in the marine environment. It was largely due to the fortuitous presence of 2 vessels with firefighting class 1 capacity berthed in Victoria, and a pre-existing marine salvage contract, that a rapid response to the fire was launched. Specialists from Resolve Marine were able to be contracted and mobilized to the occurrence location from a nearby base in the U.S., which reduced the delay in having expert knowledge available for the response. As a result, the fire involving dangerous goods was contained with minimal consequences. Although specialists in marine salvage and response can be hired on an emergency basis, a pre‑established contract can improve the timeliness of the response through availability of vessel information and pre-planning.
Canada does not require pre-arranged plans for fire response or marine salvage, unlike the U.S. Previous TSB investigations have shown that Canadian ports are not always prepared to fight shipboard fires. Following an investigation into a shipboard fire on the bulk carrier Tecumseh,TSB Marine Transportation Safety Investigation Report M19C0403. the Board issued a safety concern about the adequacy of resources for responding to shipboard fires. Outside of ports and harbours, the options for responding to a shipboard fire are even more limited should the on-board fire response be unsuccessful in suppressing a fire.
For pollution-related occurrences, Canada does not have a plan for how to respond to spills involving hazardous and noxious substances (HNS), although it does have a plan for occurrences involving oil. The federal government recognizes that there is a need for improved preparedness for HNS occurrences and has announced that it intends to develop a response program to reduce the harmful impacts of future incidences. To this end, Transport Canada (TC) and the Canadian Coast Guard have started actioning a proposal through the Oceans Protection Plan to create a single national system to respond to all marine pollution incidents, regardless of their source, in a timely manner that minimizes impact on human health and the environment. This will help improve the preparedness of the marine industry for future HNS occurrences; however, it will not be in place until at least 2027.
In June 2023, the Canada Shipping Act, 2001 was amended to give the Governor in Council the authority to make regulations, on the recommendation of the Minister, “respecting arrangements for emergency services, including requiring vessels or classes of vessels to enter into such arrangements.”Government of Canada, Canada Shipping Act, 2001 (as amended 22 June 2023), subsection 120, paragraph s.1. At June 2024, TC indicated that work to develop regulations under this provision of the Canada Shipping Act, 2001 was underway. The work is planned to continue over the next 4 years, subject to the government’s regulatory priorities. As part of this work, TC will be undertaking additional policy and risk analysis, and extensive engagement with Indigenous peoples and stakeholders. While the timespan of 4 years is not outside the norm for new regulatory initiatives, the current gaps in preparedness to respond to marine emergencies will remain during this time.
2.8 Electronic inclinometer
Data from electronic inclinometers can provide important information on the motions experienced by a vessel. This data can support navigational decision making and assist with accident investigations. Electronic inclinometers provide a continuous recording of roll angles, along with the date and time they were experienced, making it possible to establish when particular roll angles occurred and the roll period.
At the time of the occurrence, the ZIM Kingston was required by regulation to carry an analog inclinometer. Analog inclinometers record only the maximum roll angle that a vessel experiences, and they do not record the date and time of this event. They also do not provide data on the vessel’s roll period. In June 2023, the IMO amended SOLAS Chapter V, Regulation 19 to make the carriage of electronic inclinometers mandatory on container vessels and bulk carriers of 3000 GT and up that are built on or after 01 January 2026.
Without an electronic inclinometer on the ZIM Kingston, the bridge team did not have easy access to data about the vessel’s roll period, and the subsequent investigation did not have access to data to establish the precise timing of the vessel’s roll angles.
3.0 Findings
3.1 Findings as to causes and contributing factors
These are conditions, acts or safety deficiencies that were found to have caused or contributed to this occurrence.
- While the ZIM Kingston was holding offshore at La Perouse Bank awaiting a berth at the Port of Vancouver, British Columbia, it encountered environmental conditions that, in conjunction with the specific characteristics of the vessel itself, resulted in the onset of parametric rolling.
- The parametric rolling caused the vessel to roll 36° to both port and starboard. The forces that resulted from these extreme motions were the precipitating factor causing the loss of 109 containers overboard and damage to other containers that remained on board.
- The vessel owner had not developed procedures or provided specific tools to support the bridge crew on the ZIM Kingston in making assessments and managing the risk of parametric rolling; as a result, this risk was not being effectively monitored and no mitigation measures were put in place as the vessel held offshore.
- Water ingress inside a damaged container holding potassium amyl xanthate in bay 14 generated a reaction that caused a fire to ignite inside the container and then spread to 5 other nearby containers.
3.2 Findings as to risk
These are conditions, unsafe acts or safety deficiencies that were found not to be a factor in this occurrence but could have adverse consequences in future occurrences.
- If there is no comprehensive, up-to-date guidance to industry in the management of parametric rolling, there is a risk that company policies, procedures, tools, and training in this regard will be inconsistent, ineffective, or absent altogether, leading to continued container loss occurrences and their associated negative outcomes for safety and the environment.
- If masters are provided with loading plans that do not respect the limits set out in a vessel’s cargo securing manual and masters accept the risk of sailing with lashing forces that exceed safe limits, container vessels will sail with a reduced margin of safety to protect against container loss.
- If Canada is not prepared to respond to marine emergencies in Canadian waters, there is a risk that these emergencies will not be managed in a timely and effective manner, endangering vessels, their crews, the environment, and the health and safety of Canadians.
3.3 Other findings
These items could enhance safety, resolve an issue of controversy, or provide a data point for future safety studies.
- Model testing by the National Research Council Canada identified that parametric rolling can occur in significant wave heights as low as 2.6 m, far less than those encountered at the time of the occurrence.
- The on-board response to the container fire followed industry and company guidelines and was conducted in an efficient manner. The use of shore-based specialized personnel and vessels of opportunity contributed to limiting the extent of the fire.
- Danaos’s contract with an emergency response company meant that the ZIM Kingston had access to specialists who provided guidance throughout the emergency response and a team of trained personnel who were able to board the vessel to help fight the fire.
- Canada does not have a program to monitor and assess the long-term impacts of lost containers or the debris from lost containers, and the impacts on marine ecosystems are relatively unknown.
- Electronic inclinometers provide more data about a vessel’s roll angles than analog inclinometers and also provide data about a vessel’s roll period, making them more useful for safe navigation and accident investigations.
4.0 Safety action
4.1 Safety action taken
4.1.1 Danaos Shipping Co. Ltd.
Following the ZIM Kingston occurrence, Danaos Shipping Co. Ltd. (Danaos) took the following safety actions:
- On 01 November 2021, a Yes/No line item was added to the departure report to ensure that Danaos is informed when a vessel is sailing with excessive lashing forces.
- On 19 November 2021, Danaos issued a safety bulletin to all fleet masters. The bulletin described loading guidelines and some common lashing problems. As well, the bulletin reminded masters to ensure that they had a good understanding of vessel-specific lashing requirements, as documented in each vessel’s cargo securing manual. Finally, masters were encouraged to challenge ship planners if plans did not conform with the loading program or documented requirements.
4.1.2 The Canadian Coast Guard, Transport Canada, and the Vancouver Fraser Port Authority
In the fall of 2022, the Canadian Coast Guard (CCG), Transport Canada, and the Vancouver Fraser Port Authority formed a working group to examine and respond to the risks resulting from the increase in the number of vessels holding offshore, especially when weather is poor, few berths are available, or there are limited anchorages that can accommodate the vessels holding offshore.
This working group has developed a weekly memo, issued to the members of the working group and other partners, summarizing weather conditions, the number of vessels requiring berths, anchorage availability, and forecast risks. The CCG is leading an initiative to evolve this memo into a dynamic model to support decision making. The working group has also developed guidelines for communicating these risks to the masters of the vessels holding offshore.
As well, when forecast risks are high, the members of the working group collaborate to have CCG assets both available and on standby, make anchorages available to vessels holding offshore, or direct vessels to enter sheltered waters.
4.1.3 Fisheries and Oceans Canada
Fisheries and Oceans Canada issued a Fishery Notice to multiple fisheries listing the known location of 25 containers on the ocean floor. The containers were also marked as navigational seabed hazards on the Canadian Hydrographic Service chart for the area.
4.2 Safety concerns
On 21 October 2021, the container vessel ZIM Kingston, with 21 crew members on board experienced parametric rolling, rolled 36°, and lost 109 containers overboard while drifting at La Perouse Bank, about 27 nautical miles south of Ucluelet, British Columbia (BC). A number of containers on deck were also damaged. Around 36 hours later, while the vessel was anchored off Victoria, BC, a fire broke out in a damaged container that held dangerous goods. The fire then spread to 5 nearby containers and burned for 5 days before it was declared extinguished. One of the crew members was subsequently treated for smoke inhalation.
In November 2021, 4 of the containers lost overboard were recovered from the shores of northern Vancouver Island, along with various debris from the containers. In July 2023, an underwater survey located another 29 containers on the ocean floor in proximity to the occurrence site. Ongoing beach cleanups have found debris that is likely from the ZIM Kingston washing up along large stretches of the BC coastline; debris was also found as far north as Alaska, U.S.
The investigation identified safety deficiencies that led the Board to issue the following 2 safety concerns.
4.2.1 Comprehensive guidance for managing the risk of parametric rolling
Parametric rolling results from the interaction of 2 elements—the wave characteristics in a seaway and the stability characteristics of a vessel—and leads to the sudden onset of extreme roll angles for a vessel. Managing the risk of parametric rolling is complex. Not only is it difficult to predict exactly when a parametric rolling event will occur, but once extreme rolling starts, it may not be possible to stop the dangerous motions before negative consequences occur, such as container loss. For this reason, there must be a focus on monitoring for the conditions that give rise to parametric rolling so that preventive measures can be taken when the conditions are present. Doing so requires bridge crew to have access to formal policies and comprehensive procedures for managing the risk of parametric rolling. They must also have effective tools to monitor the numerous conditions affecting their vessel’s motions, analyze the risk of parametric rolling, and implement mitigating measures when necessary.
A post-occurrence analysis of the pertinent vessel and environmental parameters in the time leading up to the occurrence showed that the ZIM Kingston was at risk of developing parametric rolling and that this risk was identifiable using some of the guidance material generally available to the industry. However, the risk was not identifiable with the guidance on board the vessel at the time of the occurrence. Without formal policies and comprehensive procedures to support an assessment of risk related to parametric rolling, the master had to rely on his knowledge and experience to evaluate the safety of the vessel as it maintained a holding pattern in the open ocean. The master had a general understanding of the conditions that can lead to parametric rolling and the actions to take if it happened, but he had never experienced parametric rolling firsthand and had never completed a quantitative assessment of risk specific to parametric rolling.
Investigations by other agencies into previous occurrences involving parametric rolling point to similar inconsistencies and inadequacies with respect to the training of bridge crew and the adoption of procedures and tools to support them in managing the risk of parametric rolling. Although there are a substantial number of resources available that target a variety of audiences and present different guidance for assessing the risk of parametric rolling, none of these resources provide comprehensive guidance to help vessel owners, charterers, and bridge crew manage the risk of parametric rolling effectively.
Comprehensive guidance about parametric rolling should be presented in an accessible and understandable way. It should help bridge crew practically apply this information, by providing specific directions about when risk assessments should be done, how they should be done, what results represent unacceptable risk, and what mitigating measures should be considered. It should address the need for bridge crew to have effective tools to manage the risk of parametric rolling and an understanding of the merits and limitations of these tools. It should also address the need for training so that policies, procedures, and tools can be used to full effect by vessel crew. Finally, comprehensive guidance should address the need for company policies and procedures to foster a shared understanding of the risk around parametric rolling among all parties involved (owners, charterers, bridge crew) and to ensure that bridge crew receive support in making safety-related decisions.
The International Maritime Organization (IMO) is generally recognized as the international body best positioned to develop and disseminate comprehensive guidance to the marine industry; however, its circularInternational Maritime Organization, MSC/Circ. 1228, Revised Guidance to the Master for Avoiding Dangerous Situations in Adverse Weather and Sea Conditions (11 January 2007). addressing the risk of parametric rolling has not been updated in over 17 years and the investigation identified several shortcomings with it. For example, the circular has only minimal operational guidance on parametric rolling and does not offer any guidance with respect to policies, procedures, training, tools, or services related to the management of risk associated with parametric rolling. The circular also characterizes parametric rolling as a heavy weather phenomenon, whereas model testing of the ZIM Kingston found that parametric rolling could develop in significant wave heightsSignificant wave height is an average measurement of the largest 33% of waves (Source: National Oceanic and Atmospheric Administration, National Weather Service, “Significant Wave Height,” at https://www.weather.gov/mfl/waves [last accessed 17 July 2024]). as low as 2.6 m.
The recently published IMO Interim Guidelines on the Second Generation Intact Stability Criteria will minimize the risk of parametric rolling and will provide a consistent approach to address risk across the international shipping industry. However, the timeline for incorporation of these guidelines into the International Code on Intact Stability, 2008 is uncertain, and it is not clear whether the guidelines will apply to existing vessels. The guidelines also do not address the training of crew with respect to this issue. Similarly, it is unclear, at the time of report writing, whether the work of the IMO Subcommittee on Carriage of Cargoes and Containers will address the issues identified in this investigation.
The Board is concerned that the absence of up-to-date comprehensive industry guidance for the management of parametric rolling may cause company policies, procedures, tools, and training to be inconsistent, ineffective, or absent altogether, which could lead to more container loss occurrences, along with their associated negative outcomes for safety and the environment.
4.2.2 Canada’s preparedness for marine emergencies
On commercial vessels, crew are trained and equipped to handle many marine emergencies with on-board resources. However, an emergency can quickly shift to one where outside resources are needed. The occurrence involving the ZIM Kingston demonstrated some of the challenges involved in responding to a marine emergency in Canadian waters. It also raised questions about the availability and capability of Canadian resources to do so.
The vessel operator’s pre-existing emergency response contract was instrumental in the success of the fire response. Although emergency response specialists can be hired on an emergency basis, a pre-existing contract can improve the timeliness of the response because vessel information can be shared with the response specialists in advance, allowing a response plan to be prepared in advance.
While this occurrence took place at an anchorage outside the Port of Vancouver, previous TSB investigations have also shown that there are issues around preparedness when vessel fires occur in Canadian ports. Following an investigation into a shipboard fire on the bulk carrier Tecumseh in the Port of Windsor,TSB Marine Transportation Safety Investigation Report M19C0403. the Board issued a safety concern about the adequacy of resources in Canadian ports for responding to shipboard fires. Outside of ports and harbours, the options for responding to a shipboard fire are even more limited should an on-board fire response be unsuccessful in suppressing a fire.
Canada’s preparedness for other types of marine emergencies, such as occurrences involving hazardous and noxious substances (HNS), is also a concern. For pollution-related occurrences, Canada does not have a plan for how to respond to occurrences involving HNS, although it does have a plan for occurrences involving oil. The federal government has recognized the need to improve preparedness for HNS occurrences and has announced that it intends to develop a single national system to respond to all marine pollution incidents, regardless of their source, in a timely manner that minimizes impact on human health and the environment. In addition, Transport Canada (TC) has proposed to make regulations to strengthen preparedness requirements for industry, for example, by requiring vessels to have arrangements for firefighting and salvage services, and by having a response specialist who could work with the federal departments and other partners to manage any incident.
This occurrence, and many others, have shown that while the Canadian Coast Guard has the capacity to evacuate crew members that are injured or at risk, there are systemic gaps in other aspects of responding to emergencies on vessels. While TC is proposing the above-noted changes to address these gaps, in practice the only concrete action that has been taken so far is the 2023 amendment to the Canada Shipping Act, 2001 that gives the Governor in Council the ability to make regulations regarding emergency arrangements. At June 2024, TC indicated that work to develop these regulations is expected to continue over the next 4 years, subject to the government’s regulatory priorities.
In the interim, the Board is concerned that there are gaps in Canada’s preparedness for marine emergencies that exceed the response capacity of a vessel’s crew, posing a risk to vessels, the environment, and the health and safety of the general public.
This report concludes the Transportation Safety Board of Canada’s investigation into this occurrence. The Board authorized the release of this report on 26 June 2024. It was first released on 31 July 2024.
Correction
The details about the availability of anchorage for a vessel the size of the ZIM Kingston have been removed from the report on the basis of additional data obtained after the report’s release. The section entitled “Arranging anchorages for container vessels calling at Vancouver” has been updated accordingly.
This correction was approved by the Board on 20 August 2024; the corrected version of the report was released on 05 September 2024.
Appendices
Appendix A – List of dangerous goods on board the ZIM Kingston
Dangerous goods(listed by proper shipping name) | Stowage position (bay, row, tier) | Weight (kg) |
---|---|---|
nitrous oxide, refrigerated liquid | bay 01, row, 09, tier 84 | 8200.000 |
nitrous oxide, refrigerated liquid | 010986 | 550.000 |
nitrous oxide, refrigerated liquid | 010988 | 630.000 |
lithium-ion batteries (including lithium-ion polymer batteries) | 050782 | 9513.000 |
battery-powered vehicle or battery-powered equipment | 060112 | 8981.500 |
battery-powered vehicle or battery-powered equipment | 060314 | 9200.000 |
nitrous oxide | 060314 | 25076.800 |
lithium-ion batteries (including lithium-ion polymer batteries) | 060582 | 18000.000 |
battery-powered vehicle or battery-powered equipment | 060784 | 7390.800 |
lithium-ion batteries (including lithium-ion polymer batteries) | 060784 | 1173.000 |
lighters or lighter refills containing flammable gas | 061084 | 13694.100 |
lighters or lighter refills containing flammable gas | 061086 | 9235.800 |
environmentally hazardous substance, solid, not otherwise specified | 130710 | 24000.000 |
thiourea dioxide | 130782 | 18000.000 |
environmentally hazardous substance, solid, not otherwise specified | 130810 | 24494.400 |
sodium hydroxide, solid | 130912 | 20000.000 |
Xanthates | 140382 | 23800.000 |
Xanthates | 140384 | 23800.000 |
Xanthates | 140582 | 23800.000 |
Xanthates | 140584 | 23800.000 |
perfumery products with flammable liquid | 150682 | 365.400 |
lithium-ion batteries (including lithium-ion polymer batteries) | 150682 | 527.250 |
lithium-ion batteries (including lithium-ion polymer batteries) | 150682 | 528.000 |
lithium-ion batteries contained in equipment or lithium-ion batteries packed with equipment (including lithium-ion polymer batteries) | 150682 | 4000.000 |
environmentally hazardous substance, solid, not otherwise specified | 150708 | 24494.400 |
environmentally hazardous substance, solid, not otherwise specified | 150710 | 24000.000 |
environmentally hazardous substance, solid, not otherwise specified | 150808 | 24494.400 |
environmentally hazardous substance, solid, not otherwise specified | 150810 | 24494.400 |
environmentally hazardous substance, solid, not otherwise specified | 150912 | 24000.000 |
environmentally hazardous substance, solid, not otherwise specified | 151012 | 24494.400 |
resin solution, flammable | 170810 | 16000.000 |
Cyclohexylamine | 170908 | 14000.000 |
resin solution, flammable | 171010 | 16000.000 |
lithium-ion batteries (including lithium-ion polymer batteries) | 180382 | 11760.000 |
lithium-ion batteries contained in equipment or lithium-ion batteries packed with equipment (including lithium-ion polymer batteries) | 180386 | 5145.600 |
lithium-ion batteries contained in equipment or lithium-ion batteries packed with equipment (including lithium-ion polymer batteries) | 180486 | 5145.600 |
sulphuric acid with not more than 51% acid or battery fluid, acid | 180584 | 13.150 |
sulphuric acid with not more than 51% acid or battery fluid, acid | 180586 | 13.150 |
sulphuric acid with not more than 51% acid or battery fluid, acid | 180588 | 13.150 |
lithium-ion batteries contained in equipment or lithium-ion batteries packed with equipment (including lithium-ion polymer batteries) | 180686 | 5145.600 |
battery-powered vehicle or battery-powered equipment | 180884 | 609.840 |
battery-powered vehicle or battery-powered equipment | 180886 | 609.840 |
battery-powered vehicle or battery-powered equipment | 180888 | 609.840 |
polymeric beads, expandable evolving flammable vapour | 180982 | 25500.000 |
polymeric beads, expandable evolving flammable vapour | 180984 | 25500.000 |
polymeric beads, expandable evolving flammable vapour | 181082 | 25500.000 |
polymeric beads, expandable evolving flammable vapour | 181084 | 25500.000 |
Cyclohexylamine | 190708 | 14000.000 |
sulphamic acid | 190806 | 25000.000 |
resin solution, flammable | 191010 | 16000.000 |
corrosive liquid, acidic inorganic, not otherwise specified | 251006 | 22500.000 |
corrosive liquid, acidic inorganic, not otherwise specified | 251008 | 22500.000 |
sodium hydroxide, solid | 471006 | 20000.000 |
- | - | 741803.420 |
Source: ZIM Integrated Shipping Services
Appendix B – Flow chart from TopTier Notice to Mariners for identifying the risk of parametric rolling in following seas
Source: Maritime Research Institute Netherlands, “Notice to Mariners: Beware of parametric rolling in following seas”.
Appendix C – Sample output from TopTier roll risk estimator
Source: Maritime Research Institute Netherlands, “Roll Risk Estimator V1.3.”
Appendix D – Drifting plan issued to the ZIM Kingston by Weathernews Inc.
Source: Weathernews Inc.
Appendix E – Container loss occurrences involving parametric rolling
Internationally, there have been several other investigations into container loss occurrences that involved parametric rolling, including investigations by the Danish Maritime Accident Investigation Board (DMAIB), the UK Marine Accident Investigation Branch (MAIB), and the Japan Transport Safety Board (JTSB).
Maersk Essen
On 16 January 2021, the Danish-flagged container vessel Maersk Essen lost 689 containers overboard while en route from Xiamen, China, to Los Angeles, United States (U.S.). The containers were lost as a consequence of heavy rolling that occurred approximately 450 nautical miles north of Hawaii, U.S. The investigation by DMAIB concluded that the Maersk Essen most likely experienced parametric resonance in the port quartering seas, possibly in combination with a pure loss of stability on a wave crest.
Although the vessel’s crew had some knowledge of how to stop the heavy rolling caused by parametric resonance and had received some on-board training about parametric rolling, DMAIB found that the vessel did not have reliable information or tools readily available on board to calculate and monitor the risk of parametric rolling.Danish Maritime Accident Investigation Board, “Maersk Essen: Marine Accident Report on Loss of Cargo, 16 January 2021,” at https://dmaib.com/media/8489/maersk-essen-loss-of-cargo-on-16-january-2021.pdf (last accessed 17 July 2024), p. 41.
DMAIB also found that the only mention of parametric rolling in the vessel’s safety management system was in a procedure for navigation in adverse weather. In that procedure, parametric rolling was described as a “well-known phenomenon, which happens when the meeting frequency matches the double of vessel’s own roll frequency and wavelength exceeds 0.8 vessel’s length.”Maersk A/S, “P825 – Navigation in adverse weather,” quoted in Danish Maritime Accident Investigation Board, “Maersk Essen: Marine Accident Report on Loss of Cargo, 16 January 2021,” at https://dmaib.com/media/8489/maersk-essen-loss-of-cargo-on-16-january-2021.pdf (last accessed 17 July 2024), p. 36. The crew was advised to mitigate parametric rolling by changing heading or speed, which meant that the procedure guided the crew on how to react only after the phenomenon had already started.Danish Maritime Accident Investigation Board, “Maersk Essen: Marine Accident Report on Loss of Cargo, 16 January 2021,” at https://dmaib.com/media/8489/maersk-essen-loss-of-cargo-on-16-january-2021.pdf (last accessed 17 July 2024), p. 36. The procedure referred to an on-board training module for more guidance, but neither the training module nor the procedure referenced methods or tools for predicting the risk of parametric rolling, or specified how to determine the relationship between the vessel’s roll period and the wave encounter period. Therefore, the procedure could not be used by the crew to monitor the risk of parametric rolling.Ibid., p. 36.
Following the accident, Weathernews Inc. (WNI), which had been providing weather routing services for the vessel, prepared a report on the occurrence. The report identified that WNI had a software solution capable of motion risk forecasting that could be used for parametric rolling. WNI’s software is based entirely on the 2007 International Maritime Organization (IMO) circular (MSC.1/Circ. 1228). The WNI report concluded that the risk of parametric rolling was identified by its software to be high during the vessel’s ocean voyage.Ibid., p. 40. It is unclear as to whether the risk analysis contained in the report was carried out during the voyage or in response to the occurrence. However, WNI’s communications to the Maersk Essen during the voyage did not include any information specifically about the risk of parametric rolling.Ibid., p. 40.
The DMAIB report includes a comparison of a variety of tools that can be used for detecting the risk of parametric rolling:
- an Excel spreadsheet provided by Maersk A/S after the occurrence
- IMO MSC.1/Circ. 1228
- the Ship Performance Optimization System (SPOS) Seakeeping module that was used on some Maersk A/S vessels, but not the Maersk Essen
- the WNI motion risk forecast
The DMAIB found that all of these tools detect the risk of parametric rolling by examining the sea conditions in relation to the vessel’s stability:
They differ in the degree and accuracy of ship specific information and definitions of risk threshold, but share the uncertainty embedded in forecasts and observed data. While some of the tools have more detailed ship specific data and are better integrated into the ship’s operational procedures and software, they are still prone to uncertainty of accuracy in wave data and local variations.Ibid., p. 36.
The report also noted that although IMO MSC.1/Circ. 1228 “conveys knowledge to be used when developing operational procedures, it is not an operational tool in itself.”Ibid., p. 38.
Finally, the DMAIB encouraged companies and authorities to explore and test options for predicting parametric rolling that are based on real-time conditions rather than on forecasts.Ibid., p. 66.
ONE Apus
At around midnight on 30 November 2020 and again in the early hours of 01 December 2020, the Japanese-flagged container vessel ONE Apus experienced heavy rolling while proceeding in heavy weather off the northwest coast of Niihau Island, Hawaii, U.S. The instances of heavy rolling were approximately 90 minutes apart: the first instance involved rolling of around 20° and the second involved roll angles of 25° or more. A total of 1841 containers were lost overboard, and an additional 983 containers were damaged.
The investigation by the JTSB concluded that the roll motions experienced by the vessel were most likely different from normal hull motions and that the vessel was operating in conditions that made it vulnerable to parametric rolling.Japan Transport Safety Board, “Marine Accident Investigation Report, Container Ship ONE APUS, 2020” at https://www.mlit.go.jp/jtsb/eng-mar_report/2024/2022tk0001e.pdf (last accessed 17 July 2024), p. 39. The JTSB also concluded that the rolling caused the damage to the containers and their securing devices and the resulting loss of containers overboard.
The vessel had been provided with a reference chart entitled “Guidelines To Master For Avoiding Heavy Weather Damage.” The chart indicated wave encounter directions and other conditions that would pose risk to a sample container vessel of 289 m in length (the ONE Apus was approximately 364 m in length). The chart noted that the information was a guideline only since actual vessel reactions to waves would vary depending on the vessel’s displacement, stability, and loading. The chart also referred to the guidance in IMO MSC.1/Circ. 1228. The chart indicated that parametric rolling was a risk when waves approached the vessel between 30° and 60° from the stern, port, or starboard. It also included a stipulation that if the vessel’s roll angle exceeded 20°, the vessel’s course should be altered. Although the chart had been in use on company vessels for some time, no special training for dealing with parametric rolling had been conducted.
During the period of heavy rolling, the master made some alterations to the vessel’s course and speed so that the swell would be approaching the vessel closer to the port stern, out of the danger zone indicated by the reference chart. However, he was unable to properly assess the direction of the swell in the darkness so these changes were ineffective, and the vessel proceeded under conditions that were conducive to parametric rolling.
The JTSB concluded that the preparation of operational guidance and training for crews in the use of this guidance would help avoid similar occurrences in the future. Furthermore, the JTSB noted that the container vessel industry would benefit from the development of a system that could detect signs of parametric roll and alert crews so that mitigating measures may be taken promptly.
CMA CGM G. Washington
On 20 January 2018, the UK-flagged container vessel CMA CGM G. Washington lost 137 containers, and 85 others were damaged when it unexpectedly rolled 20° to both port and starboard in heavy seas in the North Pacific Ocean while en route from Xiamen, China to Los Angeles, U.S. The investigation by MAIB concluded that the container loss was almost certainly the consequence of parametric rolling.
The vessel was fitted with an electronic motion monitoring, forecasting, and decision support tool known as Octopus-Onboard that was developed by the ABB Group. The software combined vessel navigation and stability data with weather forecast information and ship motion measurements from on-board sensors. The data were used to provide a range of outputs designed to support the crew’s seakeeping and routing decisions.United Kingdom (UK) Marine Accident Investigation Branch, “Report on the investigation into the loss of 137 containers from the container ship CMA CGM G. Washington in the North Pacific Ocean on 20 January 2018,” at https://assets.publishing.service.gov.uk/media/5e1dc891ed915d7c7c397896/2020-2-CMACGMGWashington.pdf (last accessed 17 July 2024), section 1.3.7, paragraph 1. For example, a polar diagram “displayed weather forecast information in a format that allowed the master and bridge team to select the best course and speed to avoid excessive vessel motion.”Ibid., section 1.3.7, paragraph 2. In particular, it highlighted zones where the vessel could encounter dangerous phenomena (as described in IMO MSC.1/Circ. 1228), such as high wave groups, surfing or broaching, parametric rolling, and synchronous rolling.Ibid., section 1.3.7, paragraph 2. Another output was time traces that provided “graphical representations of real-time information from on-board sensors for pitch and roll and, based on this data, calculated the historical probability of parametric rolling.”Ibid., section 1.3.7, paragraph 6.
The Octopus-Onboard system also allowed users to set response limits for a variety of criteria, including pitch and roll, slamming, resonance zones, propeller racing, water on deck, and bending moment. However, response limits had not been set in CMA CGM G. Washington’s Octopus-Onboard system.Ibid., section 1.3.7, paragraph 3.
The Octopus-Onboard system’s time trace data on the CMA CGM G. Washington showed that there had been a 100% risk of parametric rolling on the evening before the occurrence and at the time of the two 20° rolls.Ibid., section 1.8.2, paragraph 4. However, the master and the bridge watchkeepers had focused their attention on the Octopus-Onboard system’s polar diagram, and did not refer to the time trace data.Ibid., section 2.5, paragraph 2. The investigation found that
the master and the bridge team did not use the Octopus-Onboard system effectively because they did not fully understand all of its functionality. Had the Octopus-Onboard system’s time trace data been monitored, it is highly likely that the master would have taken further action to reduce the risk of parametric roll.Ibid., section 2.5, paragraph 4.
Svendborg Maersk
On 13 February 2014, the Danish-flagged container vessel Svendborg Maersk encountered heavy weather and experienced 2 instances of sudden, extreme roll angles (up to 41°), each with an associated loss of containers. At the time, the vessel had been transiting from Rotterdam, the Netherlands, through the northern part of the Bay of Biscay.
The investigation by DMAIB could not establish whether the extreme roll motions were the result of parametric rolling, nor did the crew establish whether parametric rolling had occurred.Danish Maritime Accident Investigation Board, “Svendborg Maersk: Heavy Weather Damage on 14 February 2014,” at https://dmaib.com/media/8621/svendborg-maersk-heavy-weather-damage-on-14-february-2014.pdf (last accessed 17 July 2024), pp. 26 and 28. Although the vessel had been provided with a SPOS that had a seakeeping module capable of forecasting the roll motions of the vessel during a voyage and providing warnings for risks such as parametric rolling based on vessel-specific data, the seakeeping module had not been implemented on board at the time of the occurrence.Ibid., p. 22.
Nonetheless, the subsequent investigation report raised concerns about the company procedures that were in place to support decision making in heavy weather conditions. Specifically, the safety management system (SMS) instructed masters to order weather routing services from an additional source (the Danish Meteorological Institute) as a second opinion when the typical methods were found insufficient.Ibid., p. 23. However, when planning the voyage, the master used information that was readily available and did not have reason to seek additional weather routing support. At the time of the occurrence, wave conditions were significantly worse than forecast, but the SMS procedure offered little operational support when preparing for the voyage, as it relied on the master’s individual experience and had minimal specifications about when to do what.
The procedure for navigation in adverse weather did state that parametric and/or synchronous rolling should be taken into account; however, the investigation report pointed out that the procedure was primarily focused on describing these types of rolling and offered little support in how to practically avoid them.
From 2001 to 2003, company masters had attended a course on heavy weather damage avoidance that covered the principles of parametric rolling, precautions against it, and responses to it. The course contents were available on CD in the ship’s training library so that the crew could familiarize themselves with it, but there had not been much focus on it, because “parametric rolling had not been identified as a cause of incidents or accidents for several years.” Therefore, the crew’s awareness of the CD and its contents was limited.Ibid., p. 23.
Finally, in its investigation report, DMAIB warned that
the commercial objectives related to ships’ activities will not promote a cautious approach to voyage planning and to any decision to proceed with the voyage in adverse weather, which later would be questioned if other ships passed the area of adverse weather safely. These objectives will have an influence on the master’s decision-making.Ibid., p. 27.
P&O Nedlloyd Genoa
In January 2006, the UK-flagged container vessel P&O Nedlloyd Genoa encountered heavy weather and experienced the collapse of a container stack, with the loss of 27 forty-foot containers, while transiting west in the North Atlantic. The investigation by MAIB found it probable that the accelerations caused by excessive heavy rolling, combined with discrepancies with weight distribution, resulted in the progressive collapse of the container stack.Marine Accident Investigation Branch, “Report on the investigation of the loss of cargo containers overboard from P&O Nedlloyd Genoa, North Atlantic Ocean, 27 January 2006” at https://assets.publishing.service.gov.uk/media/547c7073ed915d4c10000091/Nedlloyd_Genoa.pdf (last accessed 17 July 2024), sections 2.4 and 2.6.2.
Prior to the collapse, the vessel was rolling and pitching heavily in 5 to 6 m swells. The master was aware of the hazards of parametric and synchronous rolling; however, his primary concern was avoiding heading into large swell waves, which could lead to slamming.Ibid., section 2.7.1, paragraph 1. When the roll amplitude increased in the deteriorating weather (roll angles of 25° to 30° were reported), the vessel adopted a course that placed the bow more into the swell and reduced speed to prevent slamming. Water ballast was also loaded into the vessel’s double bottom, which increased the vessel’s metacentric height.Ibid., section 2.7.1, paragraph 2.
The investigation found that with swell waves similar in length to the vessel’s length, these actions resulted in the wave encounter period becoming closer to half the vessel’s natural roll period.Ibid., section 2.7.1, paragraphs 2, 3, and 4. Although the sea conditions did not appear to have been steady enough to induce parametric rolling, the actions taken to counteract slamming generated the pre-conditions for parametric rolling – something that could be avoided through the provision of vessel-specific advice on the issue.
The investigation also identified that
an awareness of the circumstances and conditions that lead to parametric rolling and familiarity with preventative actions is a necessary prerequisite for deck officers serving on container vessels sensitive to parametric rolling.Ibid., section 3.1, item 13.
As a result of its investigation, MAIB recommended that the vessel operator undertake a risk assessment on the vulnerability of its vessels to parametric rolling and implement control measures should significant risk exist. One control measure was the inclusion of vessel-specific guidance to masters on when parametric rolling might be encountered and instructions on how to avoid it.Ibid., section 5, item 2006/196. Additionally, it was recommended that the Maritime and Coastguard Agency undertake consultations with the objective of including vessel-specific parametric rolling data in the vessel’s stability information for the use by the vessel’s crew.Ibid., section 5, item 2006/199.
APL China
Observations of parametric resonance on vessels were first done by William Froude in the 1860s, and parametrically induced roll has been of interest within the marine research community since the early 1950s. However, it was not until a report about the occurrence on board the container vessel APL China in 1998 involving significant container loss, parametric roll resonance became a priority among stability-related phenomena.R. Galeazzi, M. Blanke, and N. Kjølstad, “Early Detection of Parametric Roll Resonance on Container Ships,” IEEE Transactions on Control Systems Technology, Vol. 21, No. 2 (March 2013), pp. 489–503.
In October 1998, the APL China encountered extreme weather in the north Pacific and experienced unexpectedly violent motions, including rolls as great as 35° to 40° that were simultaneous with extreme pitching. The damage was extensive—approximately two thirds of the 1300 containers stowed on deck were damaged or lost.W. N. France, M. Levadou, T. W. Treakle et al. “An Investigation of Head-Sea Parametric Rolling and its Influence on Container Lashing Systems,” Marine Technology and SNAME News, Vol. 40, No. 1 (01 January 2003) pp. 1–19. This study reports on an investigation into an occurrence involving the vessel APL China that occurred in October 1998. The motions of the vessel during this storm event were investigated through a series of model tests and numerical analyses, confirming that the vessel likely experienced head-sea parametric rolling, which until this time had not been considered to be of practical concern; parametric rolling was deemed more important when in following seas.
It was found that vessels with flat transom sterns and significant bow flare are most prone to parametric rolling, due to the large variations in stability these vessels undergo in head and near-head seas. Furthermore, parametric rolling introduces loads into on-deck container stacks and their securing systems well in excess of those derived from classification society guidelines, or predicted through linear seakeeping analysis.
The report identified a need to educate vessel owners, operators, and crew concerning the phenomenon of head-sea parametric rolling and that safe and unsafe combinations of heading and speed for various sea state/loading combinations should be identified and presented to the master. Finally, the report recommended that the IMO enhance MSC circular 707, “Guidance to the Master for Avoiding Dangerous Situations in Following and Quartering Seas,” to include guidelines for operating vessels prone to head-sea parametric rolling.Ibid., pp. 1–19.