Collision with terrain
Valhalla Helicopters Inc.
Bell B205A-1 (helicopter)
Haig Lake, Alberta
The Transportation Safety Board of Canada (TSB) investigated this occurrence for the purpose of advancing transportation safety. It is not the function of the Board to assign fault or determine civil or criminal liability. This report is not created for use in the context of legal, disciplinary or other proceedings. See Ownership and use of content. Masculine pronouns and position titles may be used to signify all genders to comply with the Canadian Transportation Accident Investigation and Safety Board Act (S.C. 1989, c. 3).
Summary
On 19 July 2023, the Valhalla Helicopters Inc. Bell Textron Inc. 205A-1 helicopter (registration C-GRUV, serial number 30198) was conducting operations in support of firefighting efforts in north-central Alberta. At 1803 Mountain Daylight Time, the helicopter departed Haig Lake firebase, Alberta, on a visual flight rules flight to a forest fire located approximately 15 nautical miles northeast of Peace River Aerodrome (CYPE), Alberta, with 1 pilot onboard and an empty bucket suspended below the helicopter on a 150-foot longline. Shortly after departure, the helicopter experienced an engine failure. During the subsequent autorotation to a patch of muskeg, the water bucket became entangled in trees. At approximately 1805, the helicopter impacted the terrain in a nose-down, left-banked attitude and was substantially damaged. There was no post-impact fire. The pilot survived the initial impact and was able to egress from the helicopter but later died of his injuries.
1.0 Factual Information
1.1 History of the flight
On 19 July 2023, the occurrence pilot from Valhalla Helicopters Inc. was contacted at 1020All times are Mountain Daylight Time (Coordinated Universal Time minus 6 hours). by the dispatcher at Peace River Forestry for a 1200 departure to assist with firefighting efforts but was stood down at 1131. The pilot was subsequently dispatched at 1752 to support suppression of a fire located to the northeast of Peace River Aerodrome (CYPE), Alberta.
At 1803, the occurrence pilot departed Haig Lake firebase, Alberta, alone in a Bell Textron Inc. (Bell) 205A-1 helicopter, for a visual flight rules flight to aid in suppressing a wildfire. The helicopter had a full load of fuel in the main fuel tanks and a 150-foot longline with a water bucket attached to its external load hook.
The pilot informed the dispatcher that the helicopter was airborne and had turned on course to reach the fire, climbing to a height of approximately 1400 feet above ground level (AGL).
Once the helicopter was in level flight, the pilot contacted the dispatcher for information about the fire. While the pilot was reading back the information to the dispatcher, the helicopter lost approximately 300 feet of altitude.Flight path data was retrieved from the occurrence aircraft’s Garmin GPSMAP 496 GPS (global positioning system) device.
At 1804, the pilot informed the dispatcher that he was returning to the Haig Lake firebase due to an unspecified issue. This transmission was acknowledged by the dispatcher.
The helicopter began a 180° turn to the right, to a heading of approximately 025° magnetic, during which it continued to lose altitude. The helicopter then experienced a complete loss of engine power and the pilot began to autorotate into a section of muskeg to the west of his current location.
At 1805, when the helicopter was at a height of approximately 500 feet AGL, the pilot made 1 final transmission to the dispatcher of which only the helicopter’s call sign was heard.
Shortly thereafter, the water bucket contacted trees and then became entangled in a tree. The pilot released the longline using the manual release (also known as the mechanical release) and, shortly thereafter, the helicopter impacted the ground in a nose-down, left-banked attitude (Figure 1).
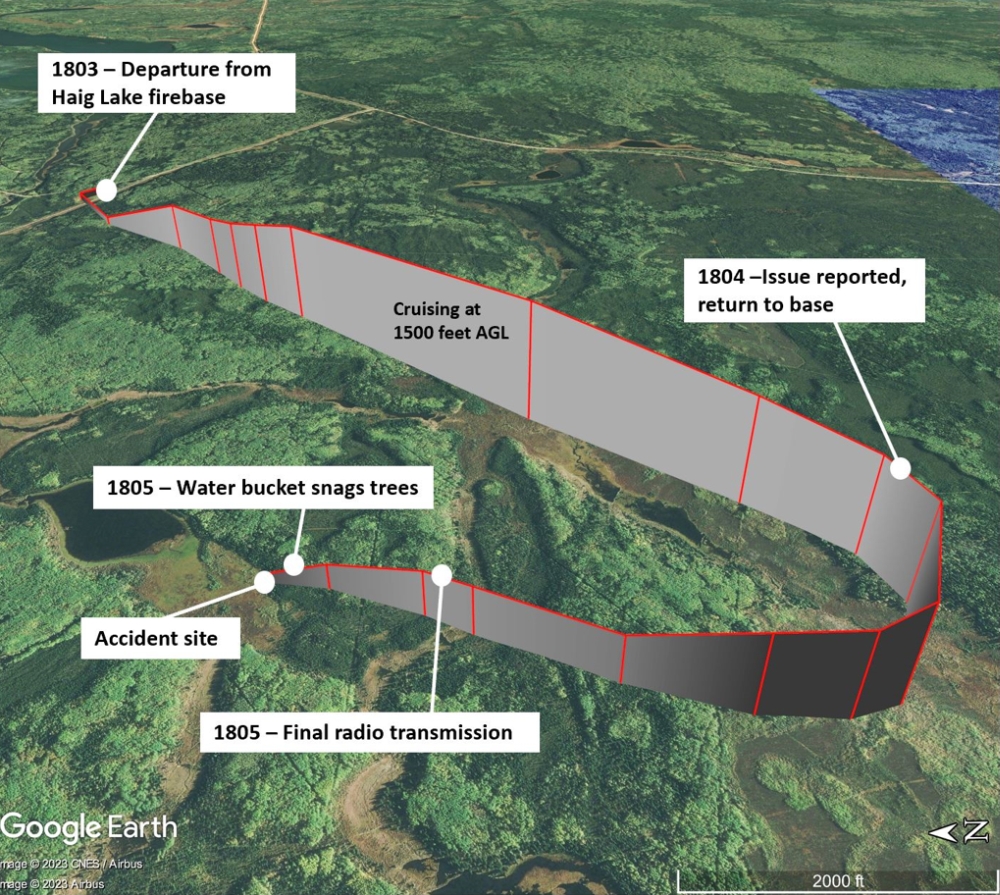
1.2 Injuries to persons
Table 1 outlines the degree of injuries received.
Degree of injury | Crew | Passengers | Persons not on board the aircraft | Total by injury |
---|---|---|---|---|
Fatal | 1 | 0 | – | 1 |
Serious | 0 | 0 | – | 0 |
Minor | 0 | 0 | – | 0 |
Total injured | 1 | 0 | – | 1 |
1.3 Damage to aircraft
The aircraft was substantially damaged by the significant impact forces when it collided with the terrain in a nose-down, left-banked attitude (Figure 2). The tail boom was hit by the main rotor blade. The condition of the main rotor blade is consistent with low rotor rpm at the time of impact.
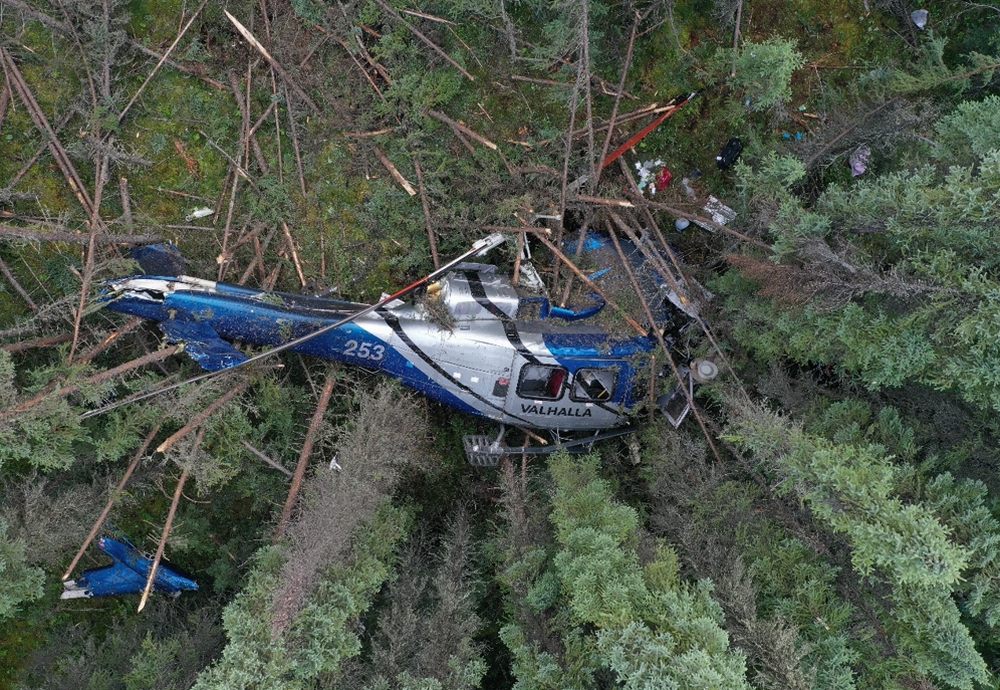
1.4 Other damage
There was no other damage.
1.5 Personnel information
The pilot held a commercial pilot licence – helicopter, with BH04 (including the Bell 205A-1), BH12, BH06, EC30, R66, RH22, and RH44 type ratings. At the time of the occurrence, the pilot had current proficiency checks on both the Bell 205A-1 and Bell 212.
The pilot completed his last Bell 205A-1 written exam on 12 March 2023. His last pilot proficiency check for the Bell 205A-1 series helicopter was conducted on 14 March 2023. The pilot held the appropriate licence and rating for the flight in accordance with existing regulations and had a valid Category 1 medical certificate.
Pilot licence | Commercial pilot licence – helicopter (CPL-H) |
---|---|
Medical expiry date | 01 February 2024 |
Total flying hours | 8711.4 |
Flight hours on BH04 (including Bell 205A-1) | 3285.6 |
Flight hours on BH12 | 2048.4 |
Flight hours in the 24 hours before the occurrence | 4.1 |
Flight hours in the 7 days before the occurrence | 49.7 |
Flight hours in the 30 days before the occurrence | 110.9 |
Flight hours in the 90 days before the occurrence | 243.6 |
Flight hours on BH04 and BH12in the 90 days before the occurrence | 243.6 |
Hours on duty before the occurrence | 9.5 |
Hours off duty before the work period | 16.5 |
Based on a review of the pilot’s work and rest schedule, there was no indication that his performance was degraded by fatigue.
1.6 Aircraft information
1.6.1 General
The Bell 205A-1 is a single-engine, single-main-rotor helicopter that can carry up to 14 passengers in addition to the pilot. The helicopter is equipped with an Ozark Aeroworks, LLC (Lycoming) T5317B free-turbine engine.
There were no recorded defects outstanding at the time of the occurrence. The aircraft’s weight and centre of gravity were within prescribed limits.
The occurrence helicopter was configured to be flown by 1 pilot from the left front seat. This configuration allows the pilot to look down the left side of the helicopter to monitor the external load (see Section 1.6.6, Design and location of aircraft system controls).
Manufacturer | Bell Textron Inc. |
---|---|
Type, model, and registration | 205A-1, C-GRUV |
Year of manufacture | 1975 |
Serial number | 30198 |
Certificate of airworthiness issue date | 12 July 2010 |
Total airframe time | 12 637.2 |
Engine type (number of engines) | Ozark Aeroworks, LLC T5317B (1) |
Rotor type (number of rotor blades) | Semi-rigid (2) |
Maximum allowable take-off weight | 10 500 lb (4627 kg)Bell Helicopters Inc., Flight manual supplement for external cargo operation to 10500 lbs gross weights (15 September 1995), section 1: Operating limitations, p. 1. |
Recommended fuel type(s) | Jet A, Jet A1, Jet B |
Fuel type used | Jet A |
1.6.2 Engine
The T53 series gas turbine engine has a 2-stage free-type power turbine, an external annular atomizing type combustor, and a 2-stage gas-producer turbine that drives a combination axial centrifugal compressor. The power shaft runs from the power turbines through the compressor section to the reduction carrier assembly.
The forward end of the compressor section is supported by the No. 1 main ball bearing (radial and axial support). The aft end of the compressor and the 2 gas-producer turbine wheels are supported by the No. 2 main roller bearing (radial support).
The T53 series engine in the occurrence aircraft (Figure 3) is rated at a take-off power of 1500 shaft horsepower and a maximum continuous power of 1350 shaft horsepower at sea level and in standard atmospheric conditions.
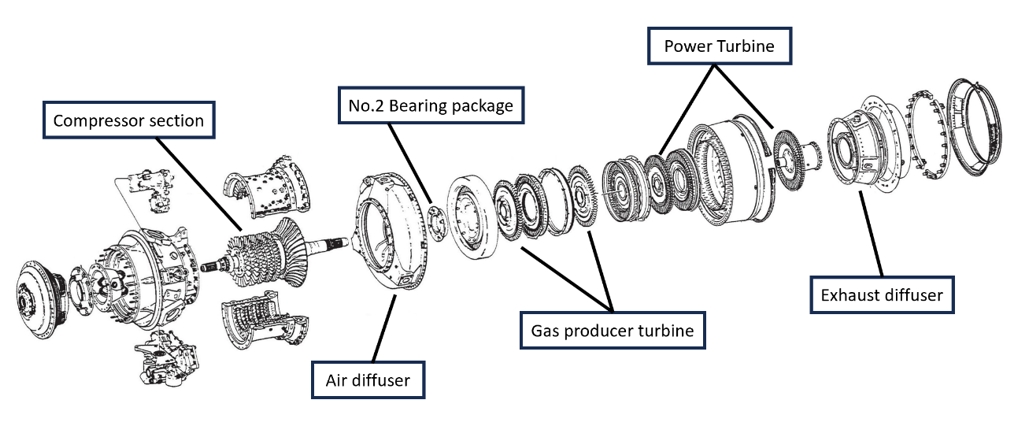
1.6.2.1 Engine examination
The occurrence engine was shipped to the Ozark Aeroworks, LLC facility in Springfield, Missouri, United States, for examination. The T53 series engine was originally designed and manufactured by Lycoming in the 1950s. Ozark Aeroworks, LLC is currently the type certificate holder and original equipment manufacturer (OEM) of the engine. Ozark Aeroworks, LLC also undertakes maintenance, repair, and overhaul of the engines.
Both the Transportation Safety Board (TSB) and the National Transportation Safety Board of the United States sent investigators to oversee the engine examination at Ozark Aeroworks, LLC.
The engine was then shipped to the TSB Engineering Laboratory in Ottawa, Ontario, where some of the components from the engine assembly were subjected to a more detailed examination and further analysis.
1.6.2.1.1 Manufacturing technique
Generally, metals can be bonded by welding, soldering, or brazing. Each of these methods has inherent benefits and drawbacks for any given bonding requirement. A complete study of each method is beyond the scope of this report; however, the 2 methods relevant to this investigation are described below:
- Welding: a fabrication process that joins 2 or more base components by means of extreme heat, pressure, or both, typically with the addition of a filler. It melds the parts together and allows them to cool, resulting in fusion. In essence, the parts are not just bonded, they are fused to become 1 part, mechanically.
- Brazing: a process in which metals are joined by melting a filler metal into the joint to create a permanent bond. Brazing requires the creation of a small joint space to allow capillary action to draw the filler metal into the joint when the parts reach the proper temperature, generally much cooler than the temperature required for effective welding. To function correctly, brazing requires a flux. Flux is a mixture of various minerals, chemicals, and alloying materials that primarily protect the molten weld metal from contamination by the oxygen and nitrogen and other contaminants in the atmosphere. The result can be an extremely strong bond between the materials but the 2 base metals are still separate and have not been fused together.
The principal differences between the 2 methods are as follows:
- Brazing is considered a liquid-solid process whereby the heated filler material is a liquid but the base material remains a solid at all times. In contrast, with arc welding, the added material and the base material are, at least for a period of time, both liquid due to the extreme electrically-generated heat of more than 10 000° F.
- Brazing can generally be accomplished with torched heat of less than 1000 °F; brazing can therefore be used in sensitive areas where the high heat of welding could damage the surrounding components.
- Brazing can be used to join dissimilar metals, whereas welding is generally only suitable for similar materials.
- If a mistake is made during brazing, the filler material can be reheated and the 2 parts realigned. Conversely, once 2 components are welded together they cannot be simply detached and realigned.
1.6.2.1.2 Air diffuser
The air diffuser conducts air from the compressor to the combustion chamber. It supports the rear bearing (compressor rotor rear bearing) housing, the 1st stage gas producer nozzle, the 2nd stage gas producer nozzle, and the 2nd stage gas producer cylinder. Air is bled from the aft face of the diffuser vanes, through a connecting manifold, to supply anti-icing and to bleed air (Figure 4).

Examination of the air diffuser’s components revealed that the No. 2 bearing support cone was brazed to the air diffuser casing assembly and that the entire circumference of the braze had failed in addition to the non-structural oil pressure and scavenge tubes at their outer extremities. The 2 separated components appeared to show no marks of previous disassembly or repair, such as grinding, chiselling, or other mechanical means that would have marred the surfaces. The intermittent fillet welds appeared to be the original OEM welds, consistent with the other welds on the air diffuser casing assembly.
The brazed surfaces did not show signs of liquation, porosity, or unevenness. The brazing appeared to have complete coverage of both surfaces over most of the circumference. The separation of the braze centreline (cohesive zone) was consistent throughout the circumference on both faces with only a few small, scattered areas of apparent loss of bonding between the air diffuser casing assembly and the support cone.
One area of the bond, under the scavenge oil tube location, appeared to have a larger area of bonding loss and separated from the air diffuser casing assembly surface. This area appeared to stretch over the entire width of the bonding area and measured approximately 10 mm wide.
There are many reasons that a brazing weld does not perform as required. A common issue is that the brazing alloy fails to bond 1 or both joining surfaces. This is normally caused by surface contamination but can also be the result of ineffective fluxing action or the formation of refractory oxide.
It is also possible for the brazing alloy to fail to smoothly flow into a joint. This is typically due to poorly fitting components, uneven heating, poor joint ventilation, overheating, or liquation (liquid/solid) separation.
Another indicator of a poor brazing joint can be porosity in the joint (voids) due to excessive variable clearances, insufficient or uneven heating, or poor joint ventilation. Blowholes, indicated by rounded shiny interiors, are the result of hydrogen pick-up in the molten alloy or flux entrapment.
Shrinkage is another indicator of a poor joint. Shrinkage is caused by excessive local tolerance, overheating, or excessive freezing range of the brazing alloy. Finally, if the failure is at the joint surface (i.e., close to one of the parent metals), it can be caused by contamination of the parent metal, the formation of a brittle layer, or possibly interfacial corrosion (stainless steel only).
Examination of the support cone brazing did show 1 area where the braze failed at or near the air diffuser casing assembly surface. This indicates a possible localized contamination in this area. Since the air diffuser casing assembly material is made from stainless steel, it is also possible there was some interfacial corrosion. However, the exact cause of this failed brazing is unknown.
There are 8 fillet welds that are used to hold the cone in position on the air diffuser casing assembly before the parts are brazed together. Three of the 8 fillet welds were torn away with the base metal of the air diffuser casing assembly still attached and were in a row, located roughly opposite to the vent tube and oil scavenge tubes. The remaining 5 fillet welds were separated at the throat of the fillet weld. These separated fillet welds also had a pounded appearance.
The distribution of these 8 failed fillet welds suggests that the braze weld failed first around most, or all, of the circumference of the support cone. The pounded appearance of the 5 fillet welds that each failed in the weld throat suggests that they failed before the 3 welds that were torn away, and these 5 were subsequently pounded due to repeated movement and contact between the support cone and air diffuser casing assembly. The 3 remaining fillet welds most likely failed due to overstress, after the braze and other fillet welds failed, because they do not exhibit the same impact (pounding) damage.
Evidence of impact damage was noted at the fitment lip around the entire circumference of the air diffuser casing assembly and support cone, again suggesting repeated movement between the support cone and air diffuser casing assembly. This means that the failure of this braze was a progressive failure with repeated movement between the support cone and air diffuser casing assembly over some length of time, most likely due to a deteriorating brazing bond.
The use of brazing in this application has the advantage that the lower heat and ease of reworking makes the initial assembly easier to perform; however, the lack of metal fusion means that if the brazing filler material breaks or there is a loss of bonding, the 2 base components can, and likely will, separate, as was the case (Figure 5) in the occurrence aircraft.
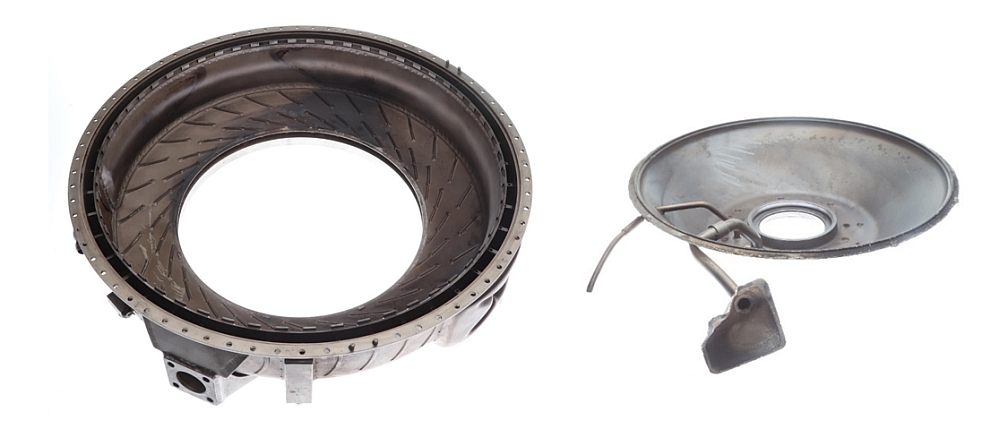
1.6.2.1.3 Exhaust diffuser
In a turboshaft engine, such as the one in this occurrence, the exhaust diffuser’s function is to reduce the back-pressure of the exhaust gas leaving the gas turbine and to redirect the hot gases. In the T53 series engine, this diffuser also acts as a support for bearings No. 3 and No. 4, which in turn support the power turbine rotor and the rear extremity of the power shaft.
The occurrence exhaust diffuser was observed to have several welding repairs and cracks. Several cracks were noted in every power turbine bearing housing inner support strut (Figure 6).
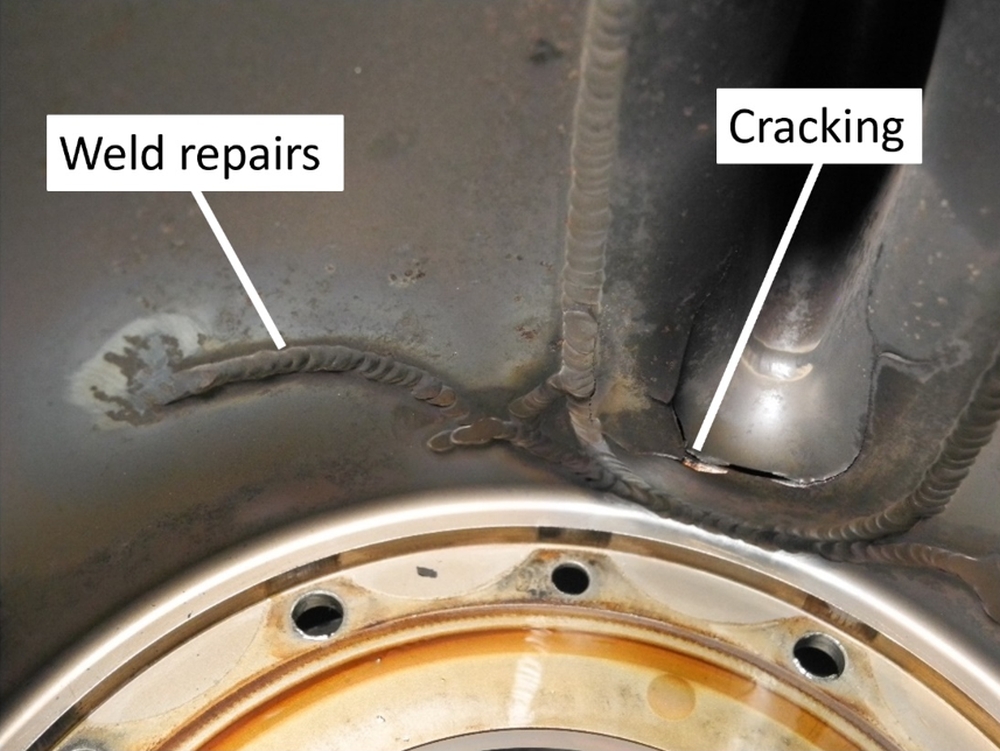
Discussions with the OEM revealed that the cracking observed on the bearing housing supports are commonly found on exhaust diffusers due to normal engine operation. The investigation determined that the occurrence exhaust diffuser had been in use for approximately 933 hours since overhaul/repair at the time of the accident.
Discussions were also held with the repair and overhaul facility (Airborne Engines Ltd.) that conducted the midlife inspection of the engine (2500 hours) and replaced the exhaust diffuser. These discussions indicated that the exhaust diffuser on this engine had been replaced due to excessive cracking at which point the occurrence diffuser was installed. The installed diffuser had been overhauled at the repair and overhaul facility.
It was also indicated that there were no limitations as to the length of cracking that can be repaired. However, if there are cracks greater than 2 inches in length in the parent metal, then the repair does require post-weld heat treatment. In the occurrence aircraft, the repaired cracks were greater than 2 inches in length and were heat-treated post-weld.
However, in this occurrence, the extensive cracking found in the exhaust diffuser was related to the loss of the No. 2 bearing support at the air diffuser. This would have added additional loading on the exhaust diffuser’s power turbine bearings (No. 3 and No. 4) housing inner support struts (Figure 7).
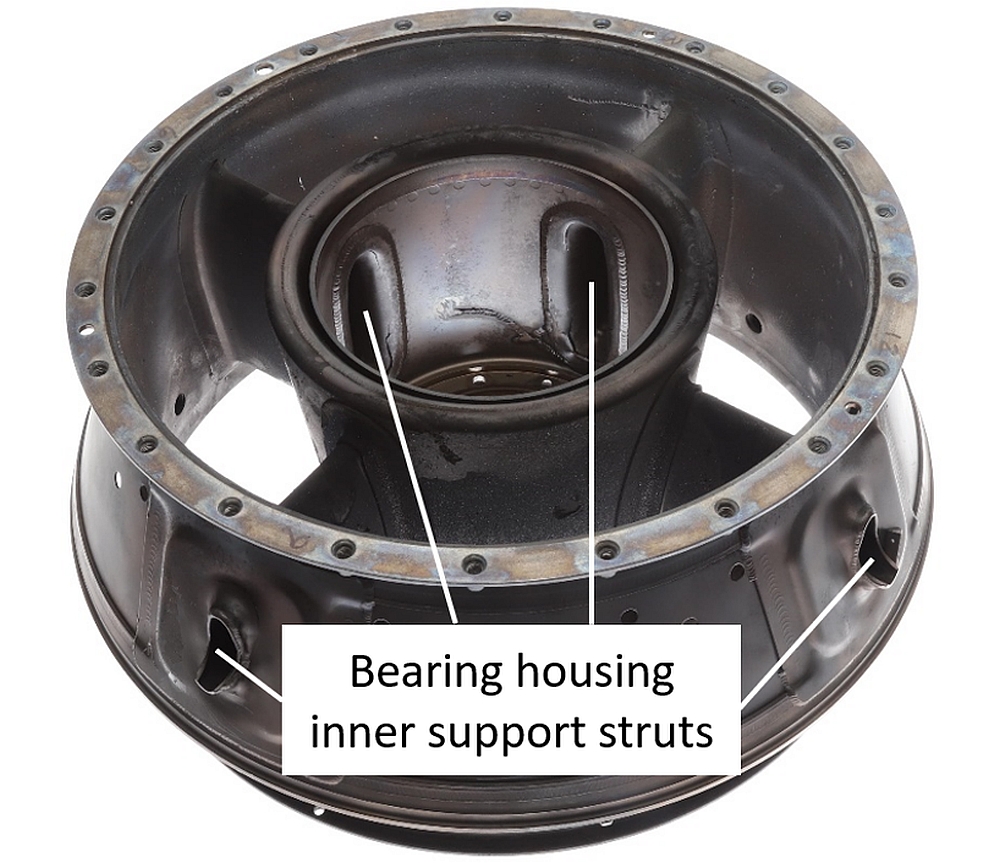
1.6.3 External load system
1.6.3.1 Suspension system
The helicopter was equipped with an Onboard Systems International, LLC (Onboard Systems International) keeperless cargo hook kit and onboard weighing system.Onboard Systems International, LLC, Document No. 121-021-00, FAA Approved Rotorcraft Flight Manual Supplement – STC SR00713SE: Cargo Hook Suspension Kits, Revision 7 (15 February 2022). The suspension system is approved for loads up to 5000 pounds on the hook and is tested to 2.5 times the rated load (12 500 pounds).
The system attaches to the existing Bell hard point and hangs at approximately the centre of gravity, attached to a lateral beam. It extends through an opening in the bottom of the lower fuselage. The cargo hook unit is a keeperless type with provisions for both an electrical- and a manual-controlled release.
The suspension system is equipped with a multi-channel slip-ring assembly that can be used to supply electrical power and control signals to accessory equipment suspended from the rotating cargo hook (Figure 8).
The primary elements of the Cargo Hook are the load beam, the internal mechanism, and a DC solenoid. The load beam supports the load and is latched through the internal mechanism. The DC solenoid and an external manual release cable provide the means for unlatching the load beam.
The load beam is normally held in the open position by a spring-loaded detent. […] In the closed position, a latch automatically engages the load beam and latches it in this position.
To release the load, the latch is disengaged from the load beam. With the latch disengaged, the weight of the load causes the load beam to swing to its open position, and the load ring slides off the load beam. The load beam then remains in the open position…Onboard Systems International, LLC, Cargo Hook Suspension System with TALON MC Keeperless Hook STC SR00713SE, Owner’s Manual, Revision 35 (25 October 2022), section 1: Theory of Operation, p. 1-6.
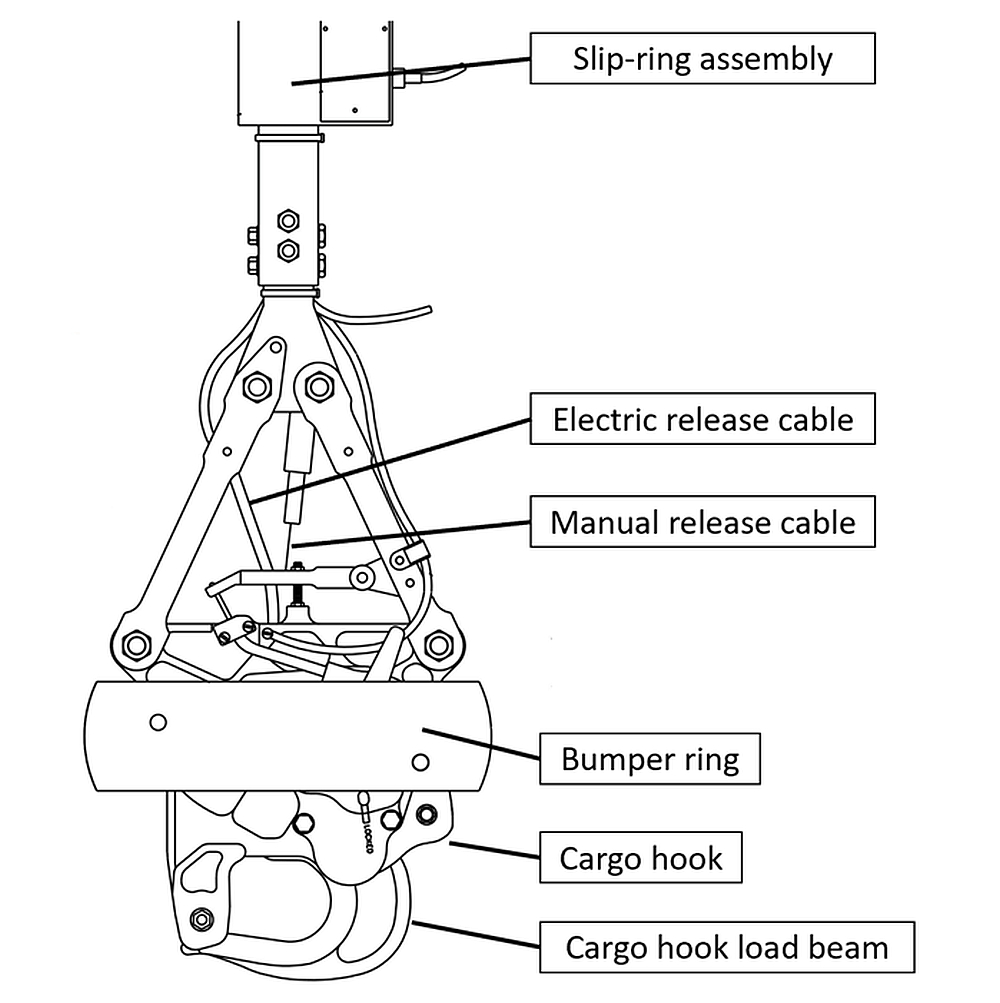
The pilot may initiate a load release by 2 different methods: either pressing the electric cargo release push button or by using the manual release pedal.Ibid.
The occurrence suspension system showed signs of deformation consistent with a strong aft-ward force being applied (Figure 9).
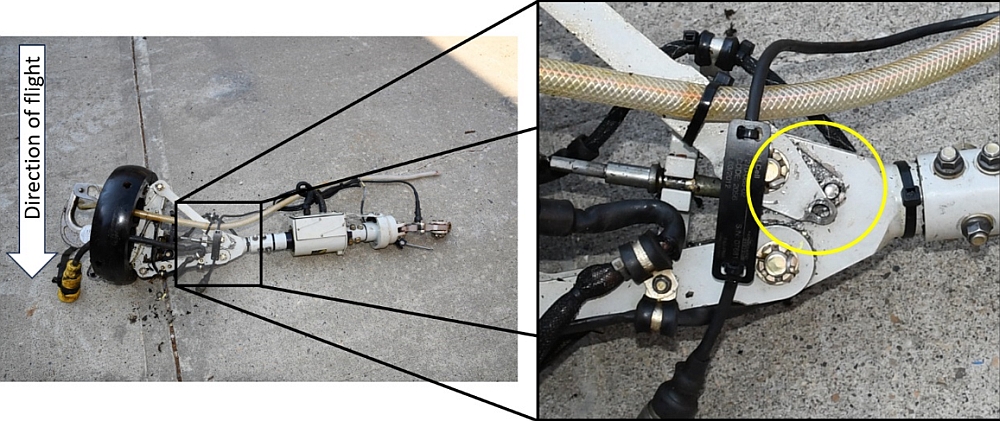
Post-accident, the cargo hook showed no damage and still functioned as designed with the manual release.
1.6.3.1.1 Electric release
TSB discussions with other helicopter operators indicate that it appears to be an industry norm to not place the CARGO REL switch in the ARM position in order to prevent an accidental electric release. This is likely because there is a perception that sufficient time would be available to either arm and then press the electric switch or activate the manual release, if required.
The risks related to the normalization of workplace practices are well known. According to the United States Air Force:
Workplace practices develop over time, through experience, and often under the influence of a specific workplace culture. These practices can be both, good and bad, safe and unsafe. They are referred to as “the way we do things round here,” which become norms. Unfortunately, such practices follow unwritten rules or behaviors, which deviate from the required rules, procedures and instructions. These norms can then be enforced through peer pressure and force of habit. It is important to understand that most norms have not been designed to meet all circumstances and, therefore, are not adequately tested against potential threats. They also lack flexibility when the broader situation changes.Air Force Safety Center, “The Dirty Dozen: Common human error factors in aircraft maintenance mishaps,” Section Norms at https://www.safety.af.mil/News/Article-Display/Article/3474731/the-dirty-dozen-common-human-error-factors-in-aircraft-maintenance-mishaps/ (last accessed on 16 December 2024).
![Figure 11. CARGO REL [cargo release] switch, as found post-accident, on the overhead panel of the occurrence helicopter. DC Power and Battery switches were selected OFF, post-accident, for safety reasons. (Source: TSB) Figure 11. CARGO REL [cargo release] switch, as found post-accident, on the overhead panel of the occurrence helicopter. DC Power and Battery switches were selected OFF, post-accident, for safety reasons. (Source: TSB)](/sites/default/files/2025-02/a23w0082-figure-11-BIL.jpg)
1.6.3.1.2 Manual release
The manual release pedal is located on the floor between the anti-torque pedals (Figure 12) on both the left and right pilot’s seats. Pressing the pedal applies tension to a metal cable that releases the internal mechanism of the cargo hook and allows it to open. Pilots remove their foot from an anti-torque pedal to depress the manual release pedal.
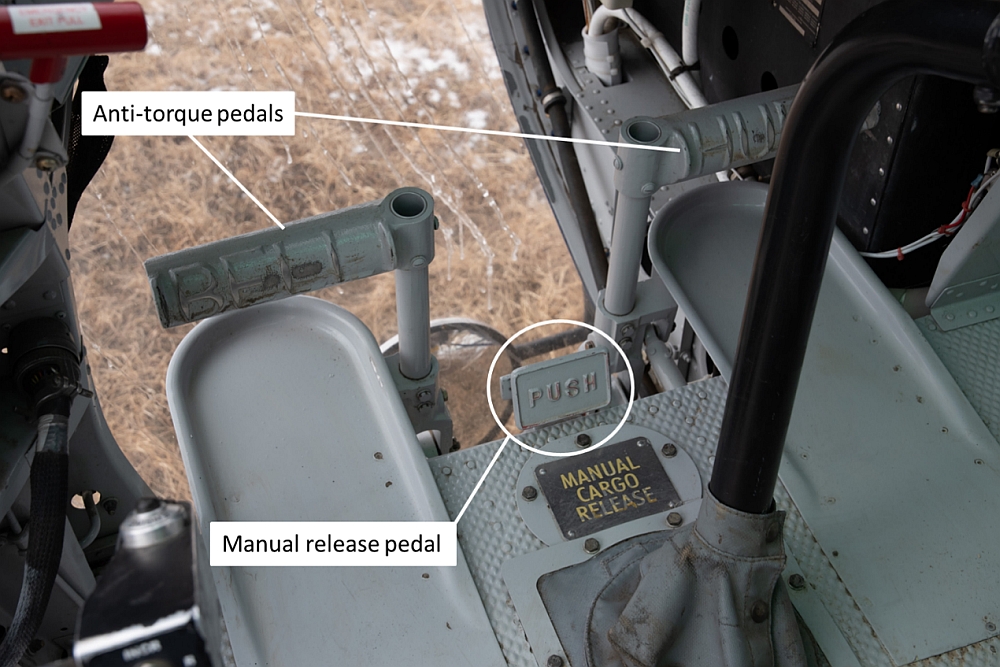
According to the rotorcraft flight manual supplement, in an emergency, such as a snagged load or engine failure, the manual release system should be the first option used to release the external load, as this system provides greater load release authority in overload conditions. If the manual release option fails, the electric release should be tried next.Onboard Systems International, LLC, Document No. 121-021-00, FAA Approved Rotorcraft Flight Manual Supplement – STC SR00713SE: Cargo Hook Suspension Kits, Revision 7 (15 February 2022), section 2-9: In-flight Operations, subsection 3: Emergency Procedures, p. 20 of 22.
1.6.3.1.3 Bell 205/212 helicopter operating differences
The pilot held valid type ratings on both the Bell 205 and Bell 212 aircraft. The normal procedures for external cargo are different between the 2 similar helicopter types.The Bell 205 and Bell 212 helicopters both possess the same airframe and rotor system. However, the Bell 212 has 2 engines and a combining gearbox that drives the single main rotor. In the Bell 205, the CARGO REL switch is to be set to ARM for electrical release, with no further guidance given.Bell Helicopters Inc., Flight manual supplement for external cargo operation to 10500 lbs gross weights (15 September 1995), section 2: Normal procedures, p. 5.
In the Bell 212, the CARGO REL switch is set to the ARM position for takeoff and landing and set to the OFF position for in-flight operations.Bell Helicopters Inc., Document No. 212-706-103, Bell 212 Rotorcraft flight manual supplement cargo hook (29 October 1970), section 2, pp. 5-6.
1.6.3.2 Longline
A 150-foot longline was attached to the helicopter’s cargo suspension system. Investigators found the line wrapped around treetops in the vicinity of the impact site. The longline was stretched with enough force to meltH. A. McKenna, J. W. S. Hearle, N. O’Hear, Handbook of Fibre Rope Technology (06 May 2004), section 9.7.3: Excessive tension / Shock Loading, p. 283. and subsequently solidify portions of the Kevlar line.
1.6.3.3 Water bucket
An SEI Industries Ltd., Bambi Bucket BB2732 was attached to the longline to assist with firefighting operations. The bucket has an overall length of 23 feet and has a capacity of 1230 L of water. It was attached to the end of the longline by means of a metal shackle and bolt that are rated to 5 times the gross weight of the bucket (14 200 pounds). The investigation determined that this connection showed no signs of stress, post-accident.
1.6.4 Annunciator panel
The filaments of the annunciator panel were examined at the TSB laboratory. The investigation was unable to determine which cockpit lights were illuminated at the time of impact.
1.6.5 Modification for flying from the left seat
The helicopter had been modified in accordance with a supplemental type certificate that allowed it to be operated from the left seat. This certificate requires the installation of several redundant systems on the left side of the cockpit to bring the pilot position to the same operational level as the right pilot position.
Included in the required items listed in the Rotorcraft Flight Manual Supplement are both electric and manual cargo releases on the left side. The electric release is mounted on the left cyclic and the manual pedal-operated release is located between the anti-torque pedals.DART Aerospace USA Inc, Rotorcraft Flight Manual Supplement for Bell 205/212/412 Models with Left Hand Pilot in Command (15 January 2023), section 0: Introduction, p. 3 of 9.
The position of the CARGO REL switch remains unchanged and is located on the left side of the overhead panel.
1.6.6 Design and location of aircraft system controls
Both the design of aircraft system controls and their location aim to balance functionality, effectiveness, usability, and safety. The location of the cockpit controls takes into consideration their importance, frequency of use, sequence of use, and grouping by function. The consequences of unintentional activation or movement of a control can create confusion or distraction and can therefore affect flight safety.
There are options to protect against an unintentional activation or movement of a control by the pilot. However, the proper balance must be found between measures to prevent unintentional activation or movement and the usability and functionality of the controls, because such measures may make the controls more difficult to activate or operate.
This is particularly important in emergencies, which are time-critical. Design options to prevent accidental activation of controls generally include the following: isolating controls or positioning them outside the normal reach of the pilot, recessing controls, orientating the axis of movement of controls to restrict movement, providing control resistance, requiring complex motions to operate a control, locking or interlocking mechanisms, or restricting access via a physical guard.Federal Aviation Administration (FAA), HF-STD-001, Human Factors Design Standard For Acquisition of Commercial-Off-The-Shelf Subsystems, Non-Developmental Items, and Developmental Systems (May 2003), chapter 6: Control and Visual Indicators.,D. Harris, Human Performance on the Flight Deck (Ashgate Publishing, Ltd., 01 October 2012), pp. 97–98.,U.S. Army Research Laboratory, ARL-MR-337 Inadvertent Activation of Controls Literature Search (October 1996).
Control switches can be mounted on the collective or the cyclic for rapid access without having to remove either hand from the flight controls. The cyclic is the most sensitive control and, since the collective can often be set to a desired level and released, there is a preference for pilots to keep their right hand on the cyclic and use their left hand to make inputs to controls not positioned on either flight controls.E. L. Wiener, D. C. Nagel, Human factors in Aviation, Academic Press Inc. (1988), pp. 606-608.
1.7 Meteorological information
At 1800, the aerodrome routine meteorological report (METAR) for CYPE, located 55 nautical miles southeast of the occurrence site, provided the following weather information:
- Wind direction variable at 5 knots
- Visibility of 6 statute miles in smoke with showers in the vicinity
- Broken ceiling at 5000 feet AGL
- Broken cloud layer at 10 000 feet AGL and overcast cloud layer at 23 000 feet AGL
- Temperature 23 °C, dew point 14 °C
- Altimeter setting 30.14 inches of mercury
At 1800, a weather station at Red Earth Creek, Alberta, which is 36 nautical miles southeast of the occurrence site, indicated the following:
- Winds from 320 ° true at 3 knots
- Temperature 19 °C and dew point 16 °C
Weather was not considered to be a factor in this occurrence.
The investigation was unable to determine what weather information the pilot obtained or reviewed before the occurrence.
1.8 Aids to navigation
Not applicable.
1.9 Communications
Not applicable.
1.10 Aerodrome information
Not applicable.
1.11 Flight recorders
The helicopter was not equipped with a flight data recorder or a cockpit voice recorder nor was either required by regulation.
The helicopter was equipped with a Garmin GPSMAP 496 device, which provided the investigation with information about its flight path. It was also equipped with an engine monitoring gauge, but the gauge was ejected from the helicopter during the accident sequence and could not be located.
1.12 Wreckage and impact information
The terrain at the occurrence site was moss-covered, forested soft ground (muskeg). The helicopter collided with the terrain in a nose-down attitude, banked to the left. The helicopter’s fuselage dug approximately 2 feet into the ground during the impact.
Both main rotor blades were still attached to the hub, with approximately 8 feet of 1 blade buried into the ground.
The majority of components were found within a small radius of the helicopter, with the exception of 1 section of the tail rotor driveshaft, which was found 170 feet from the occurrence site. The helicopter was substantially damaged due to the impact with the terrain.
The water bucket was located tangled in a tree approximately 206 feet from the helicopter with the longline still attached (Figure 13). The longline was wrapped in the treetops away from the direction of flight.
Several patches of trees were missing treetops along the helicopter’s final approach flight path, near where the water bucket was located.
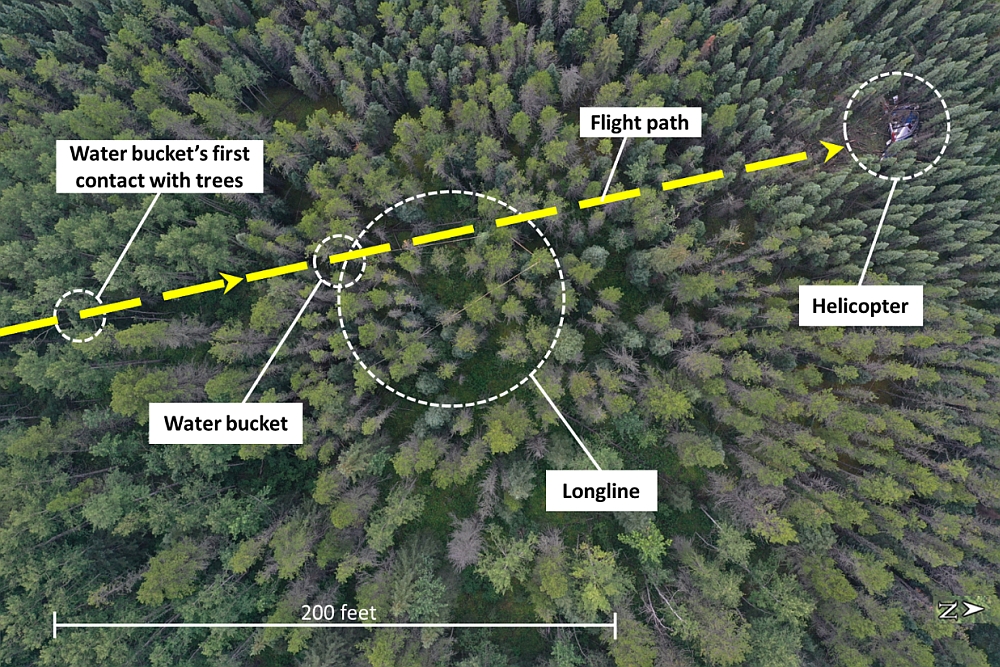
1.13 Medical and pathological information
1.14 Fire
There was no indication of fire either before or after the occurrence.
1.15 Survival aspects
The pilot was wearing a helmet at the time of the accident, which likely reduced head trauma during the impact. The post-mortem examination determined that the accident was not survivable.
1.15.1 Emergency locator transmitter
The helicopter was equipped with an ARTEX ME-406 HM emergency locator transmitter (ELT). The ELT activated on impact, and the signal was received by the COPAS/SARSAT satellite system at 1816. This information was relayed by the Canadian Mission Control Centre to the Joint Rescue Coordination Centre in Trenton, Ontario.
The Joint Rescue Coordination Centre then contacted the air operator and dispatched a Hercules search and rescue aircraft at 1833. First responders arrived at the accident site at 1956, approximately 1 hour and 51 minutes after the accident. The Hercules arrived over the accident site at 2017. The ELT was deactivated by a first responder at 2049.
1.16 Tests and research
1.16.1 TSB laboratory reports
The TSB completed the following laboratory reports in support of this investigation:
- LP018/2024 – Engine Teardown External Report Review
- LP104/2023 – NVM Data Recovery - Various
- LP141/2023 – Annunciator Panel Analysis
- LP163/2023 – T5317B Engine Air Diffuser Assembly Failure Examination
- LP164/2023 – T5317B Engine Exhaust Diffuser Assembly Failure Examination
1.17 Organizational and management information
1.17.1 Valhalla Helicopters Inc.
Valhalla Helicopters Inc. is a privately owned company providing commercial helicopter services. It holds an air operator certificate issued by Transport Canada for operations under Canadian Aviation Regulations (CARs) Subpart 702 (Aerial Work) and Subpart 703 (Air Taxi Operations).
The company operates a fleet of 14 single-engine and twin-engine helicopters and has approximately 55 employees. Its headquarters is located in Kelowna, British Columbia.
At the time of the occurrence, the company was approved by Transport Canada for Class B, C, and D external load operations (see Section 1.18.1 Helicopter external loads).Valhalla Helicopters Inc., Air Operator Certificate, 05 July 2022.
1.17.1.1 Company training
Helicopter training at the company is divided into 2 broad categories: technical ground training and flight training. Technical ground training ensures that a pilot is knowledgeable of helicopter systems and all normal, abnormal, and emergency procedures.
Flight training includes standard operating procedures for normal, abnormal, and emergency operations of the helicopter’s systems and components. With annual recurrent training, 1 hour of flight time is allotted for each single- or twin-engine helicopter type.
Valhalla Helicopters Inc. requires external load training when the pilot “has not received training for the Class of external load to be carried or has not conducted the Class of external load within the previous 24 calendar months.”Valhalla Helicopters Inc., Operations Manual, Issue 12 (20 June 2022), section 6.18.1: Class B and C External Loads, p. 6-11.
The external load training program has 1 hour allotted for ground training and 30 minutes allotted for training in the air.
The syllabus for flight training is as follows:
- Restrictions related to external load operations over built-up areas;
- Preparation of loads, load rigging procedures and attaching of Class B and Class C loads as applicable;
- Steps to be taken before starting operations, including flight and ground crew briefings, and instructions, inspection of suspension cables and pre-flight checking of jettison system;
- Precautions related to aerodynamics of Class B and Class C external loads, including oscillation and carriage of un-weighted cables;
- Flight training in the pick-up, departure, approach and delivery of representative Class B external loads as applicable;
- Flight training in manoeuvring with Class C external loads as applicable; and
- Instruction on the applicable external load flight manual supplement.Ibid.
The investigation determined that the company’s training program was in compliance with Transport Canada’s (TC’s) prescribed requirements.Transport Canada, SOR/96-433, Commercial Air Service Standards, Standard 722: Aerial Work, Division VIII: Training, subsection 722.76: Training Program.
1.18 Additional information
1.18.1 Helicopter external loads
Helicopters are used for a variety of aerial work, including external load operations. External load operations are categorized into 4 groups, depending on the work performed and the design limitations of the helicopter. TC defines external loads as follows:
helicopter Class A external load means an external load that cannot move freely, cannot be jettisoned and does not extend below the landing gear
helicopter Class B external load means an external load that can be jettisoned and that is not in contact with land, water or any other surface
helicopter Class C external load means an external load that can be jettisoned and that remains in contact with land, water or any other surface
helicopter Class D external load means an external load with a person carried externally or any external load, other than a Class A, B or C external loadTransport Canada, SOR/96-433, Canadian Aviation Regulations, subsection 101.01(1).
A water bucket is classified as a Class B external load. The 205A-1 helicopter is approved for Class B external load operations in accordance with the Bell model 205A-1 flight manual supplement for external cargo operations.Bell Helicopters Inc., Flight manual supplement for external cargo operation to 10500 lbs gross weights (15 September 1995).
1.18.1.1 Emergency procedures
1.18.1.1.1 Onboard Systems International, LLC
Onboard Systems International is a supplier of external cargo handling equipment for both civilian and military helicopters and provides the following guidance for emergency procedures while conducting external cargo operations:
3. Emergency Procedures
Consult the Flight Manual Supplement for External Cargo Operation issued by the type certificate holder for emergency procedures during external load operations.
[WARNING]
In an emergency such as snagged load or engine failure, the manual release system should be the first option for release of the external load as this system provides greater load release authority in an overload condition. If the manual release option fails, NEXT try the electrical release.Onboard Systems International, LLC, Document No. 121-021-00, FAA Approved Rotorcraft Flight Manual Supplement – STC SR00713SE: Cargo Hook Suspension Kits, Revision 7 (15 February 2022), section 2-9: In-flight Operations, subsection 3: Emergency Procedures, p. 20 of 22.
1.18.1.1.2 Bell 205A-1 flight manual
The aircraft flight manual emergency procedures section has no reference to emergencies while conducting external cargo operations nor does it mention the electric or manual cargo release systems in the helicopter.Bell Helicopters Inc., 205A-1 Flight manual, Revision 16 (18 October 1968).
1.18.1.1.3 Bell supplement for external cargo operations to 10 500 pounds gross weight
The Bell supplement for external cargo operations provides no additional guidance to existing emergency procedures found in the aircraft flight manual, Section 3: Emergency Procedures.Bell Helicopters Inc., Flight manual supplement for external cargo operation to 10500 lbs gross weights (15 September 1995).
1.18.1.2 Aerial work - emergency training
Subpart 702 of the CARs requires that “[a]n air operator shall […] include a detailed syllabus of its ground and flight training program in its company operations manual.”Transport Canada, SOR/96-433, Canadian Aviation Regulations, paragraph 702.76(3)(a).
Per the Commercial Air Service Standards (CASS):
(6) Aerial Work Training
- Pilot training shall be provided where the aerial work requires particular flight manoeuvres, aircraft performance considerations or knowledge of equipment to safely conduct the operation.
Training shall include, as applicable:
- training related to contents and requirements of flight manual supplements or airworthiness approvals;
- pre-flight inspection requirements of aerial work equipment;
- procedures for handling malfunctions and emergencies related to the aerial work equipment;
- operational preparation procedures related to reconnaissance of aerial work areas before low level flight operations;
- operational restrictions; and
- flight training and practice in required flight manoeuvres.Transport Canada, SOR/96-433, Commercial Air Service Standards, Standard 722: Aerial Work, Division VIII – Training, subsection 722.76(6): Aerial Work Training.
There is no guidance about the amount of time required on any part of, or the entirety of, the required training. The standards don’t explicitly describe a requirement for conducting training for common emergencies, such as an engine failure, that might occur while conducting aerial work, such as carrying an external load. Also, TC does not provide guidance on how to train pilots in these procedures, and many operators interpret the standard to mean that it does not require that common airborne emergencies be practised during aerial work training or be completed before conducting aerial work.
The TSB approached 2 air operators with similar fleets to discuss emergency training for external load operations. Neither had conducted emergency training for external load operations. Moreover, almost none of their pilots had ever attempted to activate the manual cargo release in flight, let alone during an autorotation.
1.18.1.3 Motor skill development
The development of motor skills follows a systematic process. Initially, learners focus on understanding the basic components of a skill, a phase known as the cognitive stage. This phase requires significant cognitive effort and results in frequent, often significant, errors. With practice, learners enter the associative stage, refining their performance while beginning to recognize and correct their errors, leading to more consistent and accurate execution of their skill. Ultimately, they reach the autonomous stage, where the skill becomes almost automatic, requiring minimal cognitive effort and allowing for fine-tuning and adaptation to varying conditions, as well as the ability to deal with other activities simultaneously.M. Martinussen and D. R. Hunter (Eds.), Aviation Psychology and Human Factors, 2nd edition (CRC Press, 2018), p. 156-162.
The acquisition of motor skills typically follows an S-shaped learning curve, starting with slow progress as learners grasp the basics, followed by rapid improvement once the basics are understood, and eventually levelling off as mastery is approached. Retention of motor skills, once learned, tends to be long-lasting, especially if the initial learning was thorough.
Skill decay, or the loss of proficiency due to lack of practice, can be mitigated by continuous practice and training. Recurrent training is crucial for maintaining proficiency, particularly for tasks that are infrequently performed but critical for safety. Understanding these stages of skill acquisition and the importance of recurrent training ensures that pilots maintain high standards of safety and performance, making critical skills second nature through practice and repetition.
1.18.2 Power loss and autorotation
The TC Helicopter Flight Training Manual describes an autorotation as:
the condition of flight where the rotor is driven by aerodynamic forces, with no power being delivered by the engine. Autorotational flight is a basic and essential emergency procedure at which every helicopter pilot must be proficient. […] During autorotation the helicopter is still flying despite the fact that the engine is not delivering motive power to the rotors. It remains fully manoeuvrable albeit in descending flight. Remember also that the airflow is now upward through the disc rather than downward as in powered flight.Transport Canada, TP9982E, Helicopter Flight Training Manual, 2nd edition (June 2006), Exercise 7 – Autorotations 1 (upper air), p. 29.
The Bell 205 flight manual states that the following steps should be performed for entering, sustaining, and landing from an autorotation: “In event of engine failure or low RPM, below 89% plus or minus 1%, RED light will illuminate and AUDIO will signal when AUDIO switch is in AUDIO position. Immediately execute an autorotative descent. Investigate power failure.”Bell Helicopters, Inc., 205A-1 Flight Manual, Revision 16 (18 October 1968), section 3: Emergency procedures, Engine failure, p. 3-3.
And subsequently:
Collective Pitch Control - Adjust as required to maintain rotor RPM.
[…]
Establish an autorotative glide at minimum airspeed of 55 knots for less than 7500 pounds gross weight and to 55 to 60 knots for gross weights above 7500 pounds.
Execute a flare by application of aft cyclic control at an altitude of 35 to 45 feet, dependent on gross weight, to reduce rate of descent and forward speed.
At an altitude of 10 feet above surface, level flare sufficiently to allow helicopter to land at a near level attitude. [emphasis in original]
At about 4 feet above surface, increase collective pitch to cushion landing.Ibid., Autorotation pp. 3-9 and 3-10.
1.18.3 Helicopter main rotor stall
As described in the Federal Aviation Administration (FAA) Helicopter Flying Handbook,Federal Aviation Administration, FAA-H-8083-21B, Helicopter Flying Handbook (2019), Chapter 11: Helicopter Emergencies and Hazards, Low Rotor RPM and Rotor Stall p. 11-15. the main rotor rpm is critical to the safe operation of a helicopter. If the main rotor rpm falls below the safe operating range and continues to decrease, the main rotor will aerodynamically stall.
As the speed of the helicopter rotor decreases, the rotor blade’s angle of attack (AOA) must be increased to support the weight of the helicopter. At a critical angle (about 15°), the airflow over the rotor blade separates, causing a sudden loss of lift and an increase in drag.
During the ensuing descent, the helicopter experiences upward airflow through the rotor disk, and the resulting AOA is so high that even the application of full down collective, which reduces the AOA of the main rotor blade, cannot restore the normal airflow.
The rotor does not stall symmetrically because any forward airspeed produces a higher airflow on the advancing side than on the retreating side. This causes the retreating blade to stall first, and its insufficient lift makes it descend as it moves aft while the advancing blade climbs as it goes forward.
The resulting low aft blade and high forward blade lead to a rapid aft-ward tilting of the rotor disk sometimes referred to as rotor “blowback” or “flapback.” As the helicopter begins to descend, the upward flow of air acting on the bottom surfaces of the tail boom and any horizontal stabilizers tends to pitch the aircraft nose down.
These 2 effects, combined with any aft cyclic input by the pilot in an attempt to keep the aircraft level, allow the rotor blades to blowback and contact the tail boom and, in some cases, actually sever it. Because the tail rotor is geared to the main rotor, in many helicopters, the loss of main rotor rpm also causes a significant loss of tail rotor thrust and a corresponding loss of directional control.
The FAA Helicopter Flying Handbook states:
Rotor stalls in helicopters are not recoverable. At low altitude, rotor stall will result in an accident with significant damage to the helicopter, and at altitudes above approximately 50 feet the accident will likely be fatal.Ibid., p. 11-16.
For these reasons, the early recognition of a low main rotor rpm condition and the application of the proper recovery technique are imperative.
2.0 Analysis
2.1 Introduction
Both pilot licensing and training were compliant with current regulations. It was also determined that neither medical nor physiological factors, including fatigue, contributed to the accident. Also, weather was not considered a factor in this occurrence.
Consequently, the analysis will focus on the cause of the helicopter’s engine power loss, the load release mechanisms onboard the aircraft, and the emergency training requirements for external load operations.
2.2 Loss of power
A teardown of the occurrence aircraft’s engine was completed as part of the investigation. It was determined that the failure of the air diffuser’s No. 2 bearing support cone brazing resulted in an unsupported No. 2 bearing and air diffuser casing assembly, and the compressor rotor made contact with the power shaft. In addition, the loss of support experienced by the gas producer nozzles and cylinder allowed contact with the rotating gas producer components. The failure of the brazing was precipitated by an undetermined defect at the time of manufacture.
This loss of support allowed the assembly to have a significant loss of concentricity and lateral power shaft displacement, also known as dynamic runout with corresponding high levels of vibration.
The result was a loss of clearance of many rotating parts within the engine. The damage observed in the power turbine and gas producer sections was consistent with this loss of concentricity and lateral compressor rotor displacement, and, in conjunction with the effects of mechanical damage caused by the separation of the air diffuser’s bearing support cone, would have severely compromised the supply of compressed air to support combustion, which would have led to the engine failure.
2.3 Water bucket contact and entanglement with trees
During the autorotation following the engine failure, the water bucket connected to the longline contacted the trees and became entangled. The snagged water bucket resulted in forward momentum being translated to a circular acceleration vector toward the ground, increasing the helicopter’s rate of descent.
To counteract this, the pilot likely pulled aft on the cyclic and increased the collective to arrest the descent. With the engine no longer producing power, these actions would have led to a decay in main rotor rpm in the final moments of flight.
The main rotor blades slowed to the point that the main rotor rpm would not have been recoverable. As the main rotor slowed, the retreating blade (left side) would have stalled, causing a roll to the left and a pitch forward in the final seconds before impact.
Finding as to causes and contributing factors
During the helicopter’s autorotation, the water bucket became entangled in trees and led to the loss of control and collision with terrain.
2.4 External load release
For unknown reasons, the pilot did not jettison the external load using either the electrical or the manual release methods at the beginning of the autorotation.
2.4.1 Electric release
The investigation learned that it is common practice within the industry for pilots, including those at Valhalla Helicopters Inc., to conduct external load operations with the CARGO REL (cargo release) switch in the OFF position. This is done to reduce the risk of an accidental release of the external load but adds complexity to the procedure when an emergency release is required.
With the CARGO REL switch in the OFF position, releasing the cargo electrically with the cyclic’s electric cargo release push button becomes a 2-step procedure and involves releasing momentarily 1 of the flight controls. This is not ideal in an emergency, particularly when the focus is on maintaining aircraft control.
Additionally, although there is an amber CARGO RELEASE ARMED annunciator illuminated on the lower right side of the forward instrument panel, a pilot may try the electric switch before recalling that the CARGO REL switch is not in the ARM position. This may result in a delay in releasing the load.
The investigation was unable to determine if the pilot in this occurrence attempted to release the water bucket using the electric cargo release push button after the engine failed.
Given that the CARGO REL switch was in the OFF position, it would have been very difficult to jettison the load using this switch in the short time between the engine failure and the impact with terrain.
To re-arm the electric release, the pilot would have had to either remove his right hand from the cyclic or his left hand from the collective and reach up above his body to the overhead panel to move the CARGO REL switch. These options would have been very difficult during the high workload and given the precision required for a successful autorotation.
If a helicopter is operated with the electric cargo release switch in the OFF position, in an emergency there is a risk that the cargo release may be delayed when the pilot is required to maintain contact with the primary flight controls rather than activating the manual cargo release.
The investigation was unable to determine in which position, either ARM or OFF, the cargo switch was typically placed by the occurrence pilot when he flew. Because of the similarities in types between the Bell 205 and Bell 212, the pilot may have implemented the Bell 212 cargo hook procedures while flying the Bell 205, which would have had him disarm the cargo release switch in cruise flight.
When a pilot flies similar aircraft types that have different cargo release procedures, there is a risk that they will choose to follow a procedure that is not meant for the aircraft type they are flying.
2.4.2 Manual release
The manual release pedal is located between the anti-torque pedals. Its location and the force required to push the release pedal down reduces the risk of accidental activation. As noted in the Onboard Systems International, LLC flight manual supplement, the manual release should be used first as it provides greater load release authority than the electric release.Onboard Systems International, LLC, Document No. 121-021-00, FAA Approved Rotorcraft Flight Manual Supplement – STC SR00713SE: Cargo Hook Suspension Kits, Revision 7 (15 February 2022), section 2-9: In-flight Operations, subsection 3: Emergency Procedures, p. 20
However, in an emergency, using the manual release requires the helicopter pilot to momentarily remove a foot from a primary flight control. This may be difficult to accomplish successfully during manoeuvres that require constant input from the pilot, such as an autorotation.
Finding as to risk
If a pilot relies on an external load release system that interferes with their ability to manipulate a primary flight control, it reduces the likelihood of a successful load release during an emergency.
It could not be determined why the load was not released before it contacted the trees. It is possible that the pilot attempted to release the load with the electric release; however, this release was disabled by the switch being in the OFF position. It is also possible that the pilot may have been focused on maintaining control of the helicopter, which delayed using either the manual or electric release.
In the final moments of the flight, the pilot successfully released the external load using the manual (mechanical) foot pedal.
2.5 Training
2.5.1 Emergency training
The Canadian Aviation Regulations (CARs) currently mandate both emergency training and external load training; however they do not specifically stipulate a requirement for conducting training of emergencies unrelated to external load equipment while conducting Class B and C external load training.
Of the 2 air operators surveyed that operate a similar fleet, both operators had conducted emergency training related to the helicopters’ load suspension system; however, neither had conducted standard emergency procedures training while conducting external load operations. Moreover, almost none of their pilots had ever attempted to activate the manual cargo release in flight, let alone during an autorotation.
Without practising an emergency procedure, such as an external load release, in a controlled environment, it is not realistic to expect a pilot to effectively perform it during an actual emergency. The development of motor skills during training involves progressing from understanding basic components to refining and eventually automating the skill. This process highlights the importance of initial and recurrent training to maintain proficiency and ensure that critical skills remain second nature, particularly for tasks that are infrequently performed but are crucial for safety during an emergency.
The Canadian Aviation Regulations do not require emergency training for Class B and C external load operations. Without this training, there is an increased risk that pilots will not effectively manage emergencies encountered during these types of external load operations.
3.0 Findings
3.1 Findings as to causes and contributing factors
These are conditions, acts or safety deficiencies that were found to have caused or contributed to this occurrence.
- A defect in a braze bond in the engine’s air diffuser, which occurred for an undetermined reason at the time of manufacture, created a localized stress concentration that, over time, resulted in the progressive failure of the braze bond and led to an engine failure.
- During the helicopter’s autorotation, the water bucket became entangled in trees and led to the loss of control and collision with terrain.
3.2 Findings as to risk
These are conditions, unsafe acts or safety deficiencies that were found not to be a factor in this occurrence but could have adverse consequences in future occurrences.
- If a helicopter is operated with the electric cargo release switch in the OFF position, in an emergency there is a risk that the cargo release may be delayed when the pilot is required to maintain contact with the primary flight controls rather than activating the manual cargo release.
- When a pilot flies similar aircraft types that have different cargo release procedures, there is a risk that they will choose to follow a procedure that is not meant for the aircraft type they are flying.
- If a pilot relies on an external load release system that interferes with their ability to manipulate a primary flight control, it reduces the likelihood of a successful load release during an emergency.
- The Canadian Aviation Regulations do not require emergency training for Class B and C external load operations. Without this training, there is an increased risk that pilots will not effectively manage emergencies encountered during these types of external load operations.
3.3 Other findings
These items could enhance safety, resolve an issue of controversy, or provide a data point for future safety studies.
- In the final moments of the flight, the pilot successfully released the external load using the manual (mechanical) foot pedal.
4.0 Safety action
4.1 Safety action taken
4.1.1 Valhalla Helicopters Inc.
After the occurrence, Valhalla Helicopters Inc. issued a company memo reminding flight crews that the electric cargo hook be armed for any external load operations and that both the manual and electric releases be checked before the 1st flight of the day.
This report concludes the Transportation Safety Board of Canada’s investigation into this occurrence. The Board authorized the release of this report on 29 January 2025. It was officially released on 27 February 2025.